Autoclaves require regular cleaning and maintenance to ensure proper functionality and prevent contamination. The frequency of cleaning depends on the usage and application, but general guidelines include daily, weekly, monthly, quarterly, and annual tasks. For clinical applications, daily water changes, weekly empty sterilization runs, and internal chamber cleaning are recommended to maintain hygiene and prevent cross-contamination. Routine maintenance, such as inspecting components like heating coils, steam traps, and safety valves, should be conducted monthly, quarterly, or annually. Proper record-keeping and using manufacturer-approved contractors for maintenance are also critical to ensure compliance and equipment longevity.
Key Points Explained:
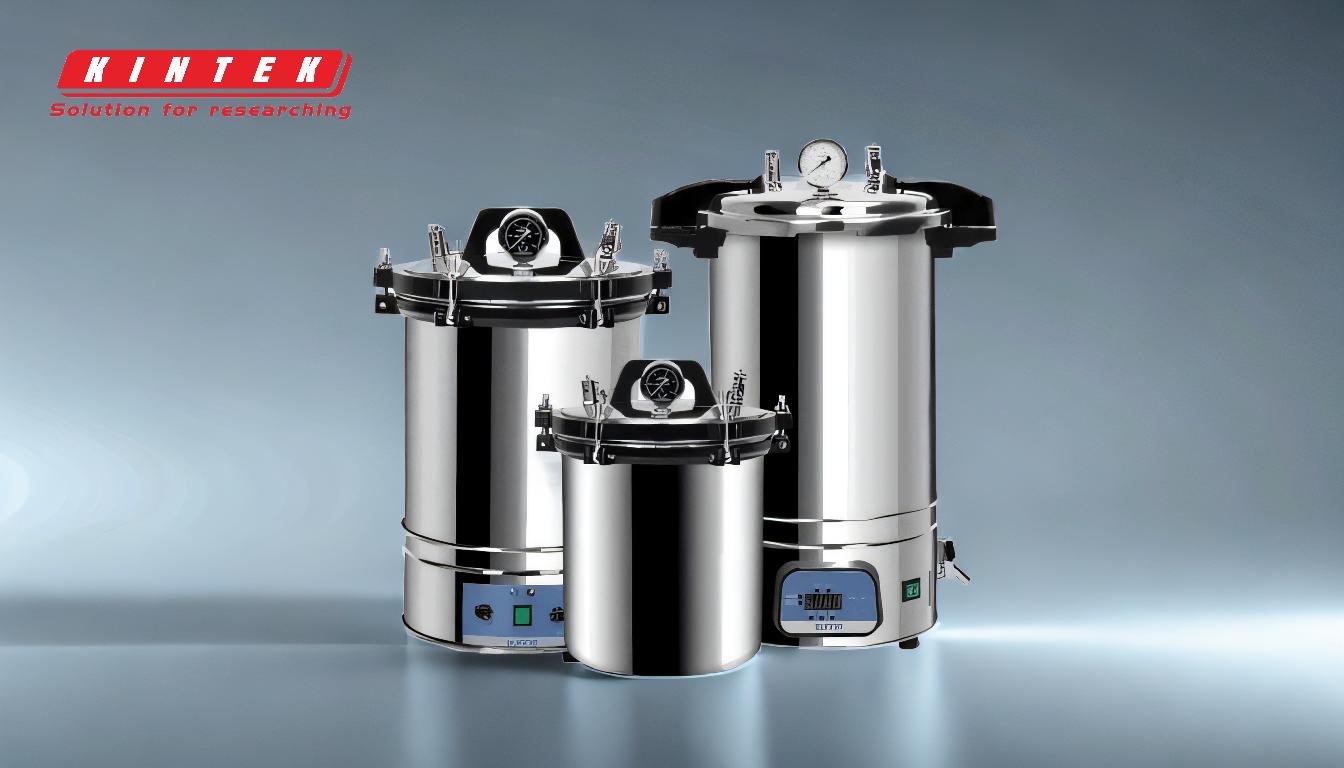
-
Daily Cleaning and Maintenance
- Water Changes: In clinical settings, it is recommended to change the autoclave's water daily. This prevents the buildup of contaminants and ensures the quality of steam used for sterilization.
- Surface Wiping: Wipe down external surfaces and the sterilization chamber door to remove any residue or debris.
-
Weekly Cleaning and Maintenance
- Empty Sterilization Runs: Perform an empty sterilization cycle (without any items) weekly to flush out any residual contaminants and ensure the autoclave is functioning correctly.
- Internal Chamber Cleaning: Clean the sterilization chamber thoroughly to remove any deposits or residues that may have accumulated during use.
- Door Gasket Inspection: Check the door gasket for wear or damage and clean it to ensure a proper seal during sterilization cycles.
-
Monthly Maintenance
- Component Inspection: Inspect critical components such as heating coils, contactors, and steam traps for signs of wear or damage.
- Drain Line Cleaning: Clean the drain lines to prevent blockages and ensure proper drainage after each cycle.
- Safety Valve Check: Verify that safety valves are functioning correctly to maintain operational safety.
-
Quarterly Maintenance
- Comprehensive Inspection: Conduct a more detailed inspection of all components, including steam traps and safety valves, to ensure they are in good working condition.
- Water Quality Check: Assess the quality of the water used in the autoclave to prevent damage from particulates or poor water quality.
-
Annual Maintenance
- Full System Check: Perform a thorough inspection and servicing of the entire autoclave system, including replacing any worn or damaged parts.
- Professional Servicing: Engage manufacturer-approved contractors to conduct the annual maintenance to ensure compliance with standards and prolong the equipment's lifespan.
-
Record-Keeping and Contractor Compliance
- Maintenance Records: Keep detailed records of all maintenance activities, including dates, tasks performed, and any issues identified. This helps track the autoclave's performance and ensures accountability.
- Approved Contractors: Only use maintenance contractors approved by the autoclave manufacturer to ensure proper servicing and adherence to warranty requirements.
By following this structured cleaning and maintenance schedule, autoclave users can ensure the equipment remains in optimal working condition, minimizes the risk of cross-contamination, and extends its operational life.
Summary Table:
Frequency | Key Tasks |
---|---|
Daily | - Change water in clinical settings - Wipe external surfaces and chamber door |
Weekly | - Perform empty sterilization runs - Clean internal chamber - Inspect and clean door gasket |
Monthly | - Inspect heating coils, contactors, and steam traps - Clean drain lines - Check safety valves |
Quarterly | - Conduct comprehensive component inspection - Assess water quality |
Annually | - Perform full system check - Engage manufacturer-approved contractors for servicing |
Ongoing | - Maintain detailed maintenance records - Use approved contractors for compliance |
Ensure your autoclave operates at peak performance—contact our experts today for tailored maintenance solutions!