Autoclaving is indeed used to sterilize liquids, as it is a highly effective method for eliminating microorganisms through the application of high-pressure saturated steam. The process involves heating liquids to a specific temperature (typically 121°C or 250°F) under high pressure for a set duration (15-20 minutes), ensuring the destruction of bacteria, viruses, and spores. This method is widely employed in laboratories, medical facilities, and industries where sterile liquids are critical, such as in microbiology, medicine, and food processing. However, it is essential to ensure that the liquids being autoclaved can withstand the high temperatures and pressures without degradation.
Key Points Explained:
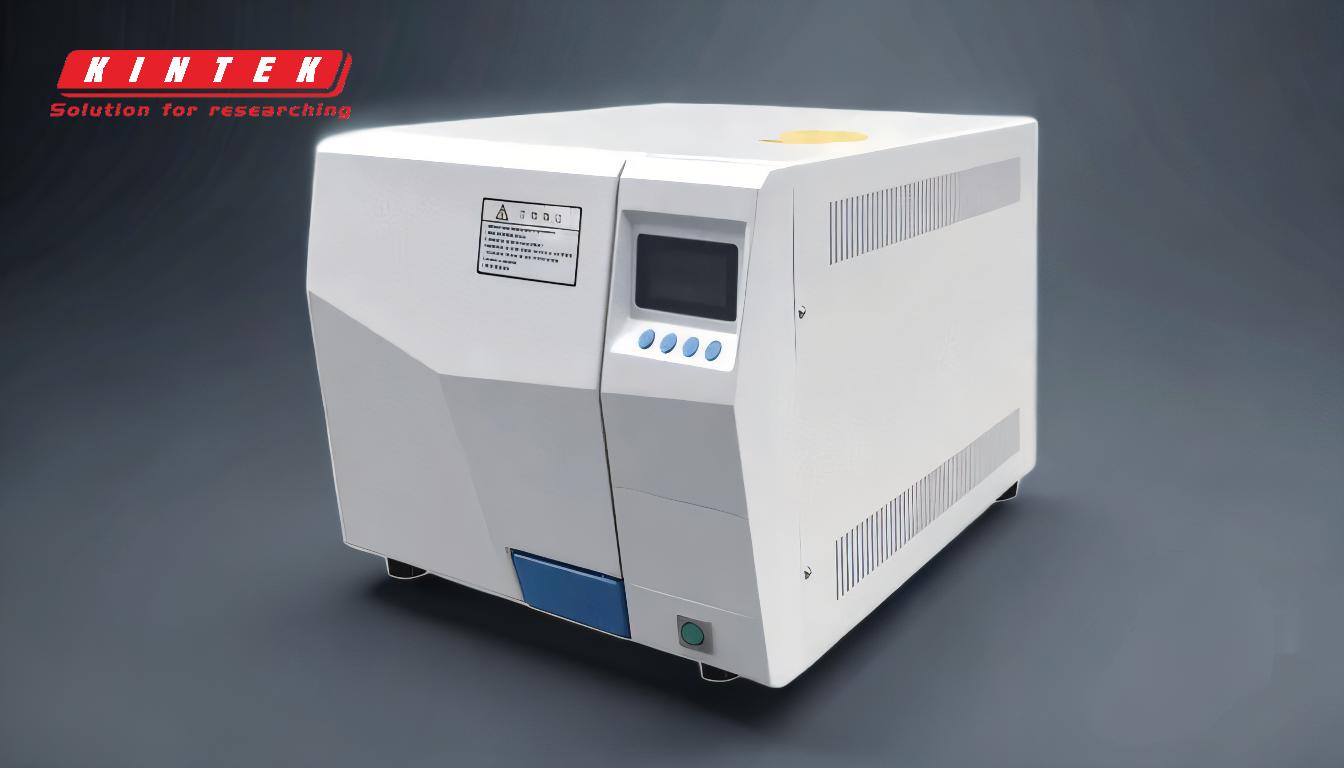
-
Autoclaving Process and Its Suitability for Liquids:
- Autoclaving uses high-pressure saturated steam to achieve sterilization.
- The standard conditions for autoclaving are 121°C (250°F) at 15-20 psi for 15-20 minutes.
- This method is effective for sterilizing liquids because the high temperature and pressure ensure the destruction of all microorganisms, including heat-resistant spores.
-
Applications of Autoclaving for Liquids:
- Microbiology and Medicine: Autoclaving is commonly used to sterilize culture media, buffers, and other liquid solutions used in laboratories and medical settings.
- Food and Chemical Industries: Liquids such as broths, sauces, and chemical solutions are often autoclaved to ensure they are free from contaminants.
- Pharmaceuticals: Sterile water, saline solutions, and other liquid formulations are autoclaved to meet stringent safety standards.
-
Considerations for Autoclaving Liquids:
- Heat Sensitivity: Some liquids may degrade or lose their efficacy when exposed to high temperatures. It is crucial to verify the thermal stability of the liquid before autoclaving.
- Container Compatibility: The containers used to hold the liquids must be able to withstand the high pressure and temperature of the autoclave without breaking or leaching chemicals.
- Volume and Loading: Proper loading of the autoclave is essential to ensure even heat distribution. Overloading can lead to inadequate sterilization.
-
Advantages of Autoclaving Liquids:
- Reliability: Autoclaving provides a high level of sterility assurance, making it a trusted method for critical applications.
- Scalability: It can be used for small volumes in laboratory settings or large-scale industrial processes.
- Cost-Effectiveness: Compared to other sterilization methods like filtration, autoclaving is relatively inexpensive and requires minimal consumables.
-
Limitations of Autoclaving Liquids:
- Time-Consuming: The process can take longer than other methods, especially when considering cooling times.
- Energy Intensive: Autoclaving requires significant energy to generate and maintain high temperatures and pressures.
- Not Suitable for All Liquids: Heat-sensitive liquids, such as certain enzymes or volatile compounds, may require alternative sterilization methods.
In summary, autoclaving is a highly effective and widely used method for sterilizing liquids, provided the liquids and their containers can withstand the process conditions. It is essential to consider the specific requirements of the liquids being sterilized to ensure both efficacy and safety.
Summary Table:
Aspect | Details |
---|---|
Standard Conditions | 121°C (250°F) at 15-20 psi for 15-20 minutes |
Applications | Microbiology, medicine, food processing, pharmaceuticals |
Advantages | Reliable, scalable, cost-effective |
Limitations | Time-consuming, energy-intensive, not suitable for heat-sensitive liquids |
Key Considerations | Heat sensitivity, container compatibility, proper loading |
Need help with autoclaving liquids? Contact our experts today for tailored solutions!