Co-sputtering, a variation of the traditional sputtering process, involves the simultaneous deposition of two or more materials from separate targets onto a substrate. This technique combines the benefits of sputtering with the added advantage of creating composite or alloy films with tailored properties. Below is a detailed explanation of the advantages of co-sputtering, supported by the principles and benefits of sputtering outlined in the references.
Co-sputtering offers several advantages, making it a versatile and efficient technique for thin film deposition. It combines the benefits of traditional sputtering, such as high deposition rates, precise control, and excellent film uniformity, with the ability to create composite or alloy films with customized properties. This method is particularly useful in applications requiring tailored material characteristics, such as in microelectronics, optics, and semiconductor industries. By enabling the simultaneous deposition of multiple materials, co-sputtering allows for the creation of films with unique chemical compositions, microstructures, and functional properties that are difficult to achieve with single-target sputtering.
Key Points Explained:
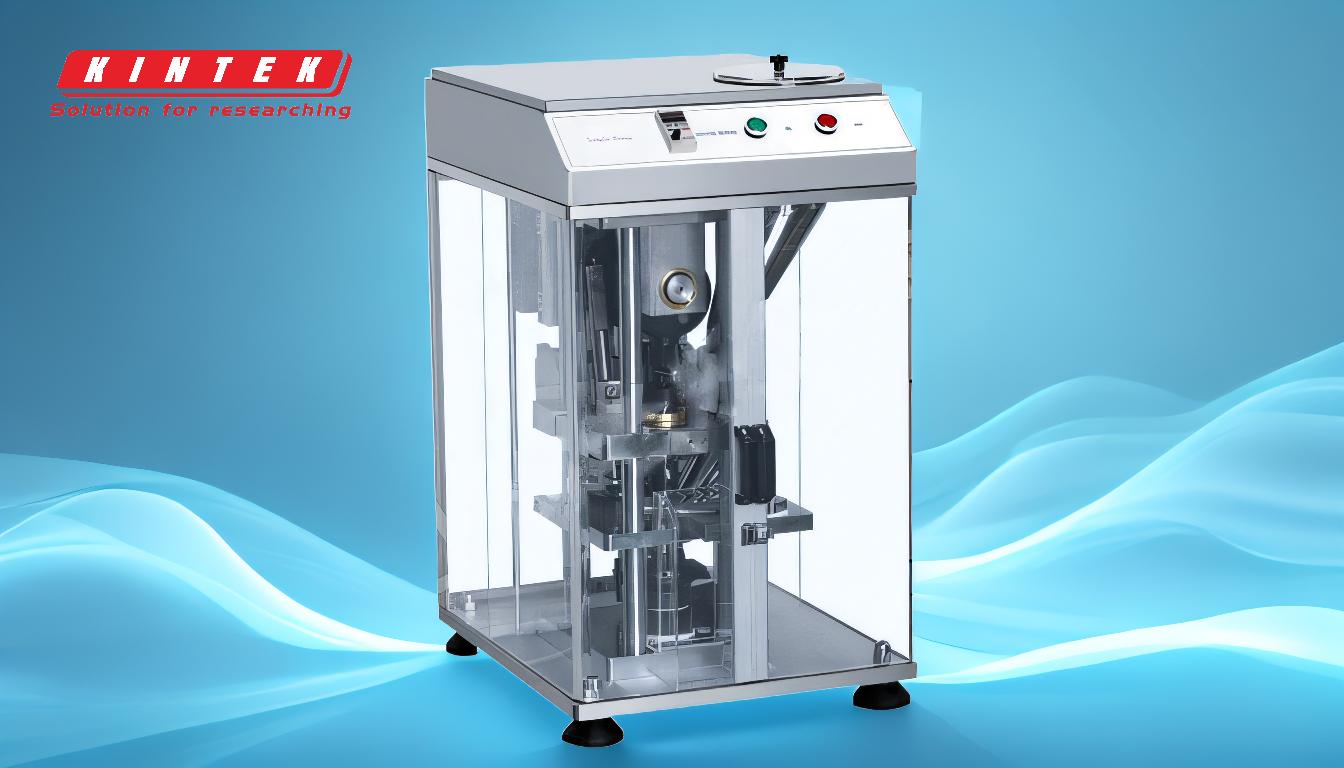
-
Tailored Material Properties
- Co-sputtering allows for the deposition of composite or alloy films by combining two or more materials in a single process. This enables the creation of films with specific chemical compositions, microstructures, and functional properties that are not achievable with single-target sputtering.
- For example, co-sputtering can be used to deposit films with graded compositions, where the ratio of materials changes gradually across the film thickness, or to create films with unique optical, electrical, or mechanical properties.
-
Enhanced Film Uniformity and Control
- Like traditional sputtering, co-sputtering provides excellent control over film thickness and uniformity. By adjusting process parameters such as target current, deposition time, and gas pressure, the composition and thickness of the deposited film can be precisely controlled.
- This level of control is particularly important in applications requiring highly reproducible and uniform films, such as in semiconductor manufacturing or optical coatings.
-
Versatility in Material Selection
- Co-sputtering can utilize a wide range of target materials, including metals, semiconductors, insulators, and compounds. This versatility allows for the deposition of films with diverse properties, such as high melting points, low vapor pressures, or specific electrical conductivities.
- The ability to combine materials with different properties (e.g., a metal and a dielectric) opens up new possibilities for creating advanced functional materials.
-
Improved Adhesion and Film Quality
- The high energy of sputtered atoms in co-sputtering enhances the adhesion between the film and the substrate, forming a diffusion layer that improves bonding.
- Additionally, co-sputtered films typically exhibit high density, fewer pinholes, and high purity, as the process avoids contamination from evaporation sources.
-
Environmental and Economic Benefits
- Co-sputtering is an environmentally friendly process, as it operates in a vacuum environment and uses inert gases like argon. This reduces the risk of contamination and minimizes waste.
- The ability to deposit multiple materials in a single process also reduces production time and costs, making it an economically viable option for industrial applications.
-
Applications in Advanced Technologies
- Co-sputtering is widely used in industries such as microelectronics, optics, and energy storage. For example, it can be used to deposit thin films for solar panels, magnetic storage devices, and optical coatings.
- The technique is also valuable in research and development, where the ability to create novel materials with tailored properties is essential for advancing technology.
In summary, co-sputtering combines the inherent advantages of sputtering—such as precise control, high deposition rates, and excellent film quality—with the added benefit of enabling the deposition of composite or alloy films. This makes it a powerful tool for creating advanced materials with tailored properties, suitable for a wide range of industrial and research applications.
Summary Table:
Advantage | Description |
---|---|
Tailored Material Properties | Create composite/alloy films with unique chemical, optical, or mechanical properties. |
Enhanced Film Uniformity & Control | Precise control over film thickness and composition for reproducible results. |
Versatility in Material Selection | Deposit a wide range of materials, including metals, semiconductors, and insulators. |
Improved Adhesion & Film Quality | High-density, pure films with excellent adhesion and fewer defects. |
Environmental & Economic Benefits | Eco-friendly process with reduced production time and costs. |
Applications in Advanced Tech | Used in microelectronics, optics, energy storage, and R&D for novel materials. |
Unlock the potential of co-sputtering for your projects—contact our experts today to learn more!