Reactive sputtering is a specialized form of sputter deposition that combines the benefits of traditional sputtering with chemical reactions to create thin films with unique properties. This method involves introducing a reactive gas, such as oxygen or nitrogen, into the sputtering process, which reacts with the target material to form compounds like oxides or nitrides. The advantages of reactive sputtering include enhanced film properties, improved adhesion, and the ability to deposit complex materials. Below, we explore the key advantages of reactive sputtering in detail.
Key Points Explained:
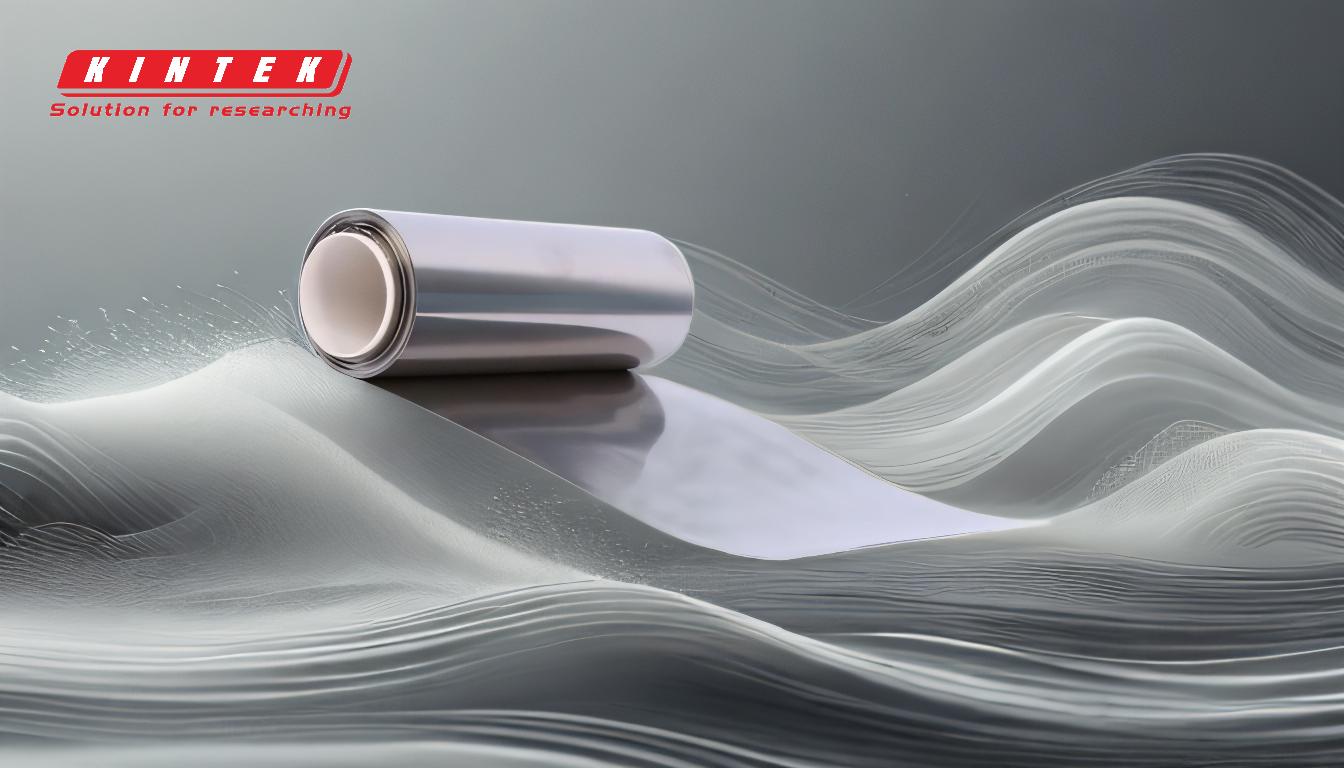
-
Enhanced Film Properties
- Reactive sputtering allows for the deposition of compound materials, such as oxides, nitrides, and carbides, which are difficult or impossible to achieve with traditional sputtering.
- The introduction of reactive gases during the process enables the formation of films with tailored optical, electrical, and mechanical properties. For example, titanium nitride (TiN) films deposited via reactive sputtering are widely used for their hardness and wear resistance.
-
Improved Adhesion
- Sputtered atoms possess higher kinetic energy compared to evaporated materials, resulting in better adhesion to the substrate. Reactive sputtering further enhances this by creating chemical bonds between the film and the substrate, improving durability and longevity.
- This is particularly beneficial for applications requiring robust coatings, such as in the semiconductor and optical industries.
-
Versatility in Material Deposition
- Reactive sputtering enables the deposition of a wide range of materials, including high-melting-point metals and complex alloys.
- It can also produce multi-component films with precise stoichiometry, making it ideal for advanced applications like solar panels, microelectronics, and optical devices.
-
Uniform and Dense Films
- The process produces highly uniform and dense films, even at relatively low temperatures. This uniformity is critical for applications requiring precise thickness control, such as in semiconductor manufacturing.
- The dense packing of atoms in the film reduces porosity, enhancing the film's mechanical and barrier properties.
-
Cost-Effectiveness
- Reactive sputtering is relatively inexpensive compared to other thin-film deposition techniques, such as chemical vapor deposition (CVD).
- The ability to deposit high-quality films with minimal material waste makes it an economical choice for large-scale industrial applications.
-
Flexibility in Deposition Geometry
- Unlike evaporation deposition, which is limited to bottom-up configurations, reactive sputtering can be performed in various geometries, including top-down and side deposition.
- This flexibility allows for coating complex shapes and structures, expanding its applicability in industries like aerospace and automotive.
-
Advancements in Magnetron Sputtering
- The integration of magnetron sputtering with reactive processes has further improved deposition rates and control over film properties.
- This combination is particularly useful for depositing dielectric and nitride films, which are essential in microelectronics and semiconductor applications.
-
Environmental and Safety Benefits
- Reactive sputtering is performed in a controlled vacuum environment, minimizing the release of harmful byproducts into the atmosphere.
- The use of inert gases like argon and reactive gases like oxygen or nitrogen is generally safer and more environmentally friendly compared to some chemical deposition methods.
In summary, reactive sputtering offers a unique combination of versatility, precision, and cost-effectiveness, making it a preferred method for depositing high-quality thin films in various industries. Its ability to produce complex materials with enhanced properties ensures its continued relevance in advanced manufacturing and research.
Summary Table:
Advantage | Description |
---|---|
Enhanced Film Properties | Deposits compound materials like oxides, nitrides, and carbides with tailored properties. |
Improved Adhesion | Creates chemical bonds for better durability and longevity. |
Versatility in Deposition | Enables deposition of high-melting-point metals and complex alloys. |
Uniform and Dense Films | Produces highly uniform, dense films with precise thickness control. |
Cost-Effectiveness | More economical than other methods like CVD, with minimal material waste. |
Flexibility in Geometry | Allows coating of complex shapes in various deposition geometries. |
Magnetron Sputtering | Improves deposition rates and control over film properties. |
Environmental Safety | Minimizes harmful byproducts and uses safer gases like argon and oxygen. |
Unlock the potential of reactive sputtering for your applications—contact our experts today!