Sputtering is a highly versatile and precise thin-film deposition technique with numerous advantages, making it a preferred choice for various applications in industries such as semiconductors, optics, and coatings. Its key benefits include the ability to deposit a wide range of materials, even those with high melting points, at reduced temperatures. It ensures high-quality films with excellent adhesion, uniformity, and density, while also enabling precise control over film properties. Additionally, sputtering is cost-effective, compatible with reactive gases, and supports advanced processes like epitaxial growth. Its ability to clean substrates and deposit coatings in the same vacuum chamber further enhances its efficiency and practicality.
Key Points Explained:
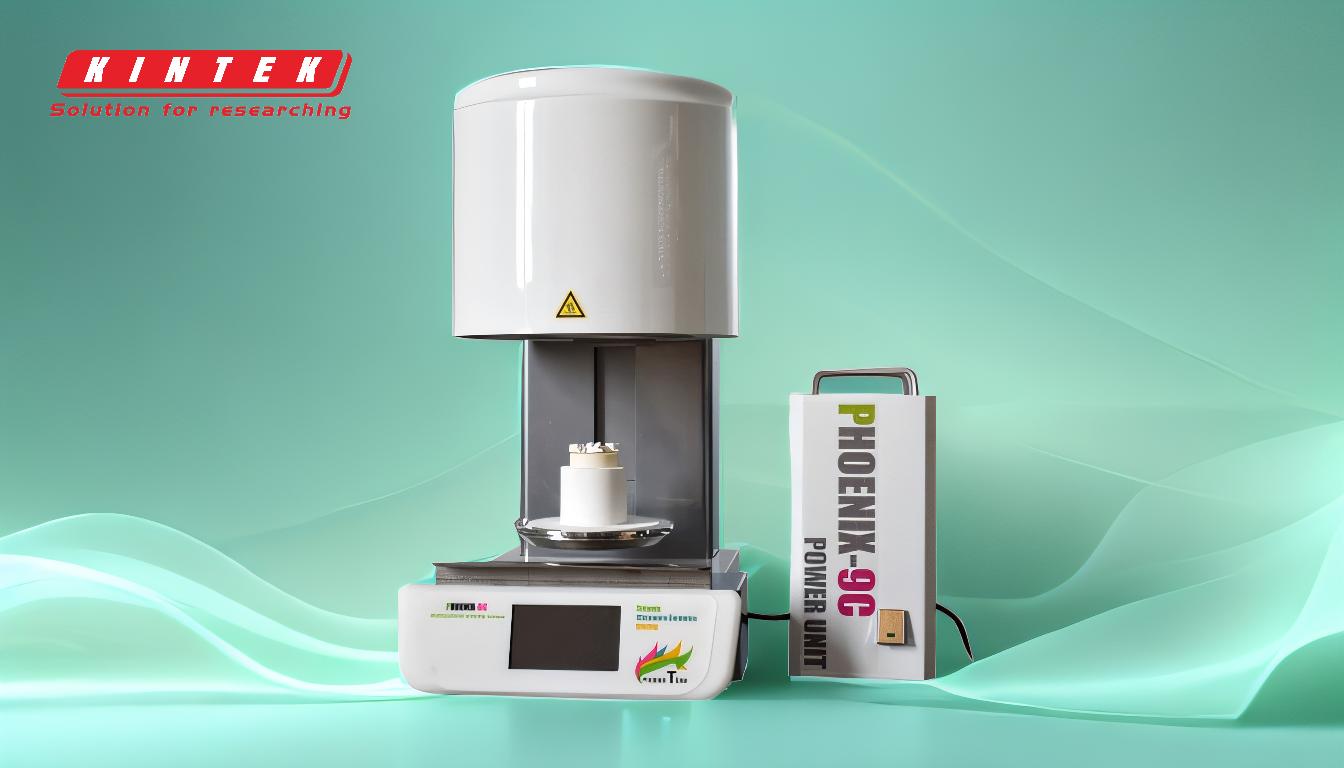
-
Versatility in Material Deposition:
- Sputtering can deposit a wide range of materials, including plastics, organics, glass, metals, and even materials with very high melting points that are difficult to evaporate.
- It is compatible with diverse mixtures and alloys, making it suitable for complex material systems.
-
Molecular-Level Precision and Film Quality:
- Sputtering enables atomic-level precision in film deposition, resulting in pristine interfaces between materials.
- Films produced by sputtering exhibit better adhesion, higher packing densities, and more uniform coverage compared to other methods like thermal evaporation.
-
Low-Temperature Deposition:
- The process can be performed at reduced or medium temperatures, which is particularly advantageous for temperature-sensitive substrates like plastics or organics.
- Low-temperature deposition reduces residual stresses on the substrate, improving the overall quality of the film.
-
High Deposition Rates and Scalability:
- Sputtering offers high deposition rates without thickness limitations, making it suitable for both thin and thick film applications.
- It supports large-scale production and is relatively inexpensive compared to other deposition methods.
-
Enhanced Adhesion and Densification:
- Sputter-ejected atoms possess higher kinetic energies than evaporated materials, leading to better adhesion and denser films.
- The process ensures good step or via coverage and can achieve concurrent double-sided coating with the right mechanical configuration.
-
Compatibility with Reactive Gases and Advanced Processes:
- Sputtering is compatible with reactive gases, allowing for the deposition of optical films by oxidizing or nitriding sputtered metal ions to form oxide or nitride layers.
- It supports advanced techniques like epitaxial growth, enabling the creation of high-quality crystalline films.
-
Reproducibility and Automation:
- Sputtering offers excellent reproducibility and is easier to automate compared to methods like E-Beam or thermal evaporation.
- This makes it ideal for industrial applications requiring consistent and reliable film properties.
-
Maintenance-Free and Ultrahigh Vacuum Compatibility:
- The process is maintenance-free and can be performed in ultrahigh vacuum conditions, ensuring clean and contamination-free deposition environments.
- Substrates can be cleaned and coated in the same vacuum chamber, improving efficiency and reducing processing time.
In summary, sputtering stands out as a highly effective and flexible deposition method, offering superior film quality, material versatility, and process efficiency. Its ability to meet the demands of modern technology and industrial applications makes it a cornerstone of thin-film fabrication.
Summary Table:
Advantage | Description |
---|---|
Versatility in Material Deposition | Deposits a wide range of materials, including high-melting-point substances. |
Molecular-Level Precision | Ensures pristine interfaces, better adhesion, and uniform coverage. |
Low-Temperature Deposition | Ideal for temperature-sensitive substrates, reducing residual stresses. |
High Deposition Rates | Suitable for thin and thick films, with scalable and cost-effective production. |
Enhanced Adhesion and Densification | Produces denser films with superior adhesion and step coverage. |
Reactive Gas Compatibility | Enables optical film deposition via oxidation or nitridation. |
Reproducibility and Automation | Consistent and reliable film properties, ideal for industrial applications. |
Maintenance-Free and UHV Compatibility | Clean, contamination-free deposition in ultrahigh vacuum environments. |
Unlock the full potential of sputtering for your applications—contact us today to learn more!