Three-plate molds are specialized tools used in injection molding, primarily for manufacturing round parts or components where filling from the outer edges is challenging, suboptimal, or impossible. These molds allow for more precise gate placement, often using a hot runner system, which improves part quality but comes at a higher cost. Their design enables efficient material flow and reduces waste, making them ideal for complex geometries and high-precision applications. Below, we explore the key applications and advantages of three-plate molds in detail.
Key Points Explained:
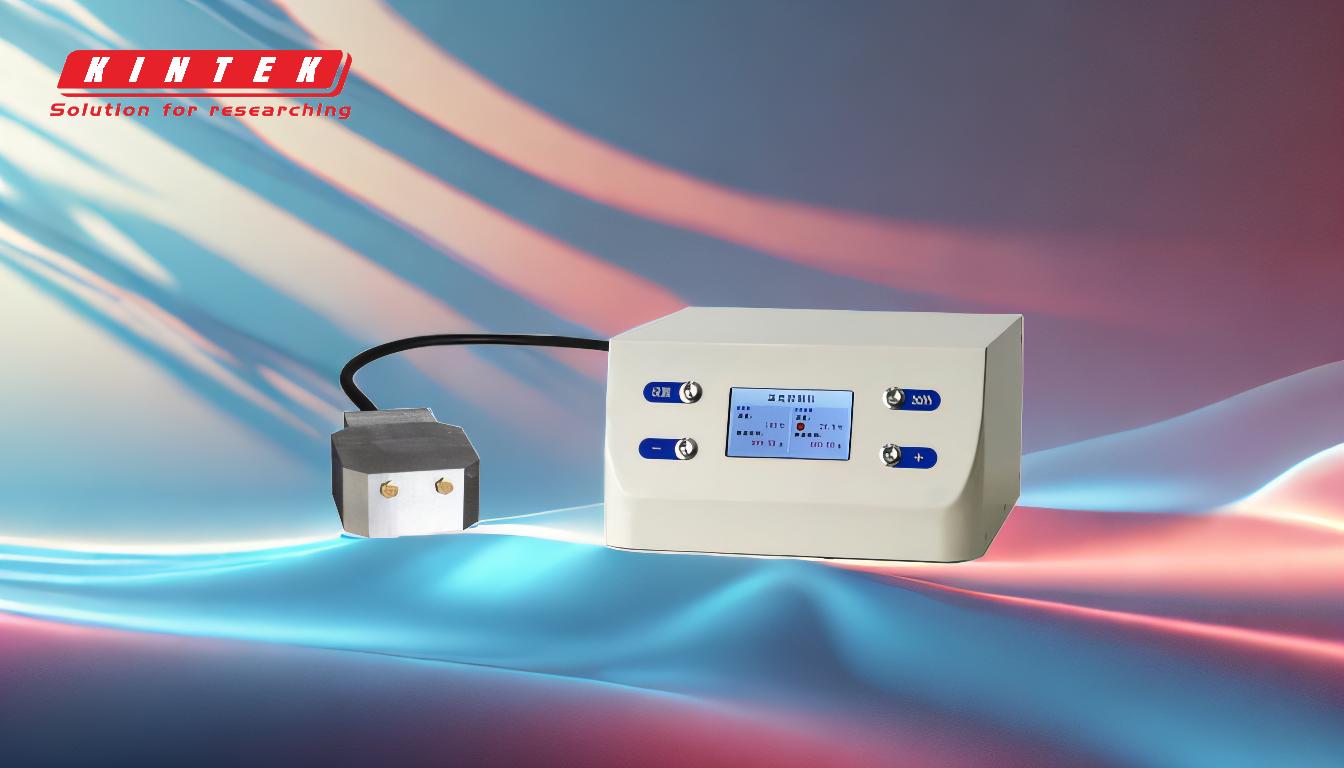
-
Applications in Round or Complex Parts
- Three-plate molds are particularly suited for manufacturing round parts or components with intricate geometries.
- They address challenges in filling molds from the outer edges, ensuring uniform material distribution and reducing defects like warping or incomplete filling.
- Examples include caps, closures, and cylindrical components where precision and consistency are critical.
-
Optimal Gate Location for Improved Part Quality
- The design of three-plate molds allows for gate placement at the most optimal location on the part, often near the center or other critical areas.
- This ensures better material flow, minimizes stress points, and enhances the overall quality of the molded part.
- A hot runner system is frequently used in conjunction with three-plate molds to further improve gate performance, though it increases costs.
-
Cost Considerations and Trade-offs
- While three-plate molds offer superior performance for complex parts, they are more expensive to design and manufacture compared to two-plate molds.
- The additional cost is justified for applications requiring high precision, reduced waste, and improved part quality.
- Businesses must weigh the benefits against the higher upfront investment when choosing three-plate molds for their projects.
-
Reduction of Material Waste
- Three-plate molds are designed to minimize material waste by separating the runner system from the molded part more efficiently.
- This separation occurs automatically during the ejection process, reducing the need for manual trimming and improving production efficiency.
- The reduced waste is particularly beneficial for high-volume production runs, where even small savings per part can lead to significant cost reductions.
-
Versatility in Manufacturing
- These molds are versatile and can be used for a wide range of materials, including thermoplastics and thermosetting polymers.
- Their adaptability makes them suitable for industries such as automotive, medical devices, consumer goods, and electronics, where precision and reliability are paramount.
-
Enhanced Ejection and Cooling
- The three-plate design allows for better control over the ejection process, reducing the risk of part damage during removal.
- Improved cooling channels can be integrated into the mold, ensuring faster cycle times and higher production rates.
- This is especially advantageous for parts with thin walls or complex geometries that require precise cooling to maintain dimensional stability.
In summary, three-plate molds are indispensable for producing high-quality, complex parts with precise gate placement and minimal waste. While they come at a higher cost, their benefits in terms of part quality, material efficiency, and production versatility make them a valuable investment for industries requiring advanced injection molding solutions.
Summary Table:
Key Feature | Description |
---|---|
Applications | Ideal for round or complex parts like caps, closures, and cylindrical components. |
Gate Placement | Optimal gate location ensures better material flow and minimizes stress points. |
Cost | Higher upfront cost but justified for high-precision, low-waste applications. |
Material Waste Reduction | Efficient runner separation minimizes waste, especially in high-volume production. |
Versatility | Suitable for thermoplastics, thermosetting polymers, and various industries. |
Ejection & Cooling | Improved ejection and cooling channels enhance production efficiency. |
Ready to optimize your injection molding process? Contact us today to learn more about three-plate molds!