Bioreactor design is a critical aspect of bioprocessing, influencing the efficiency, scalability, and success of biological production systems. Key considerations include the type of bioreactor (e.g., stirred-tank, airlift, or packed-bed), the choice of materials (e.g., stainless steel or single-use systems), and the integration of advanced monitoring and control systems. Design must also account for the specific biological process, such as cell culture or fermentation, and ensure scalability from lab to industrial scale. Factors like sterility, mixing efficiency, oxygen transfer, and heat management are essential to optimize performance. Additionally, regulatory compliance, cost-effectiveness, and sustainability play significant roles in the design process.
Key Points Explained:
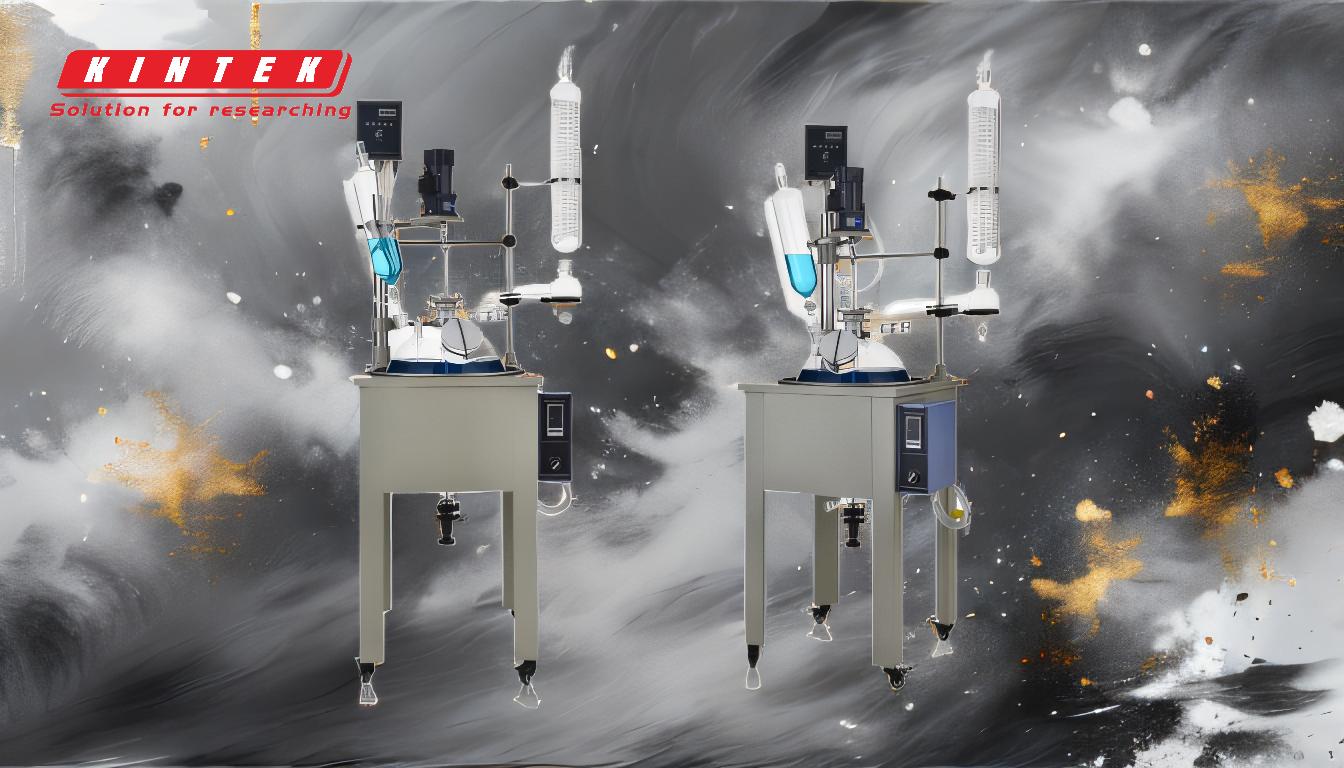
-
Type of Bioreactor:
- Stirred-Tank Bioreactors: Commonly used due to their versatility and ability to handle a wide range of processes. They are ideal for cell cultures and microbial fermentations.
- Airlift Bioreactors: Suitable for processes requiring gentle mixing and low shear stress, such as plant cell cultures.
- Packed-Bed Bioreactors: Used for immobilized cell systems, offering high cell density and efficient substrate utilization.
-
Material Selection:
- Stainless Steel: Durable and reusable, suitable for large-scale industrial applications. It offers excellent resistance to corrosion and high temperatures.
- Single-Use Systems: Increasingly popular for their flexibility and reduced risk of contamination. They are cost-effective for small to medium-scale productions and eliminate the need for cleaning and sterilization.
-
Monitoring and Control Systems:
- Advanced Sensors: Integration of pH, temperature, dissolved oxygen, and biomass sensors for real-time monitoring.
- Automation: Use of automated control systems to maintain optimal conditions, ensuring consistent product quality and process efficiency.
-
Biological Process Considerations:
- Cell Culture: Requires precise control over nutrient supply, oxygen levels, and waste removal to maintain cell viability and productivity.
- Fermentation: Needs efficient mixing and aeration to support microbial growth and metabolite production.
-
Scalability:
- Lab to Pilot Scale: Design must allow for easy scaling from small laboratory setups to larger pilot plants, ensuring process parameters remain consistent.
- Industrial Scale: Focus on cost-effectiveness, energy efficiency, and the ability to handle large volumes without compromising performance.
-
Sterility and Contamination Control:
- Aseptic Design: Incorporation of features like sterile filters, steam-in-place systems, and clean-in-place protocols to prevent contamination.
- Single-Use Components: Reducing contamination risks by using disposable parts that are replaced after each batch.
-
Oxygen Transfer and Mixing Efficiency:
- Aeration Systems: Design of spargers and impellers to ensure adequate oxygen supply and uniform mixing, critical for cell growth and product formation.
- Shear Stress Management: Balancing mixing intensity to avoid damaging sensitive cells while ensuring efficient nutrient and oxygen distribution.
-
Heat Management:
- Cooling Jackets: Integration of cooling systems to manage heat generated during exothermic reactions, maintaining optimal temperature for biological processes.
- Insulation: Use of insulating materials to minimize heat loss and maintain stable internal conditions.
-
Regulatory Compliance:
- GMP Standards: Adherence to Good Manufacturing Practices to ensure product safety and quality.
- Documentation: Maintaining detailed records of design specifications, validation processes, and operational procedures to meet regulatory requirements.
-
Cost-Effectiveness and Sustainability:
- Energy Efficiency: Design considerations to minimize energy consumption, such as optimizing mixing and aeration systems.
- Waste Reduction: Implementation of strategies to reduce waste generation and improve resource utilization, contributing to sustainable bioprocessing practices.
By addressing these considerations, bioreactor design can be optimized to meet the specific needs of the biological process, ensuring efficient, scalable, and compliant production systems.
Summary Table:
Key Consideration | Details |
---|---|
Type of Bioreactor | Stirred-Tank, Airlift, Packed-Bed |
Material Selection | Stainless Steel (durable, reusable) or Single-Use Systems (flexible, low contamination risk) |
Monitoring & Control | Advanced sensors (pH, temperature, dissolved oxygen) and automation systems |
Biological Process | Cell Culture (nutrient control) or Fermentation (mixing, aeration) |
Scalability | Lab to industrial scale, ensuring consistent process parameters |
Sterility & Contamination | Aseptic design, single-use components |
Oxygen Transfer & Mixing | Aeration systems, shear stress management |
Heat Management | Cooling jackets, insulation |
Regulatory Compliance | GMP standards, detailed documentation |
Cost-Effectiveness | Energy efficiency, waste reduction |
Ready to optimize your bioreactor design? Contact our experts today for tailored solutions!