Agitated thin film evaporators (ATFEs) are widely used in various industries for their ability to handle heat-sensitive materials and achieve high evaporation rates. However, they come with several disadvantages that can impact their efficiency, cost, and suitability for certain applications. Key drawbacks include contamination risks, cleaning challenges, limitations in handling specific sample types, and high operational and maintenance costs. Additionally, they may struggle with complex surfaces, large-scale uniformity, and energy efficiency. Understanding these limitations is crucial for equipment purchasers to make informed decisions.
Key Points Explained:
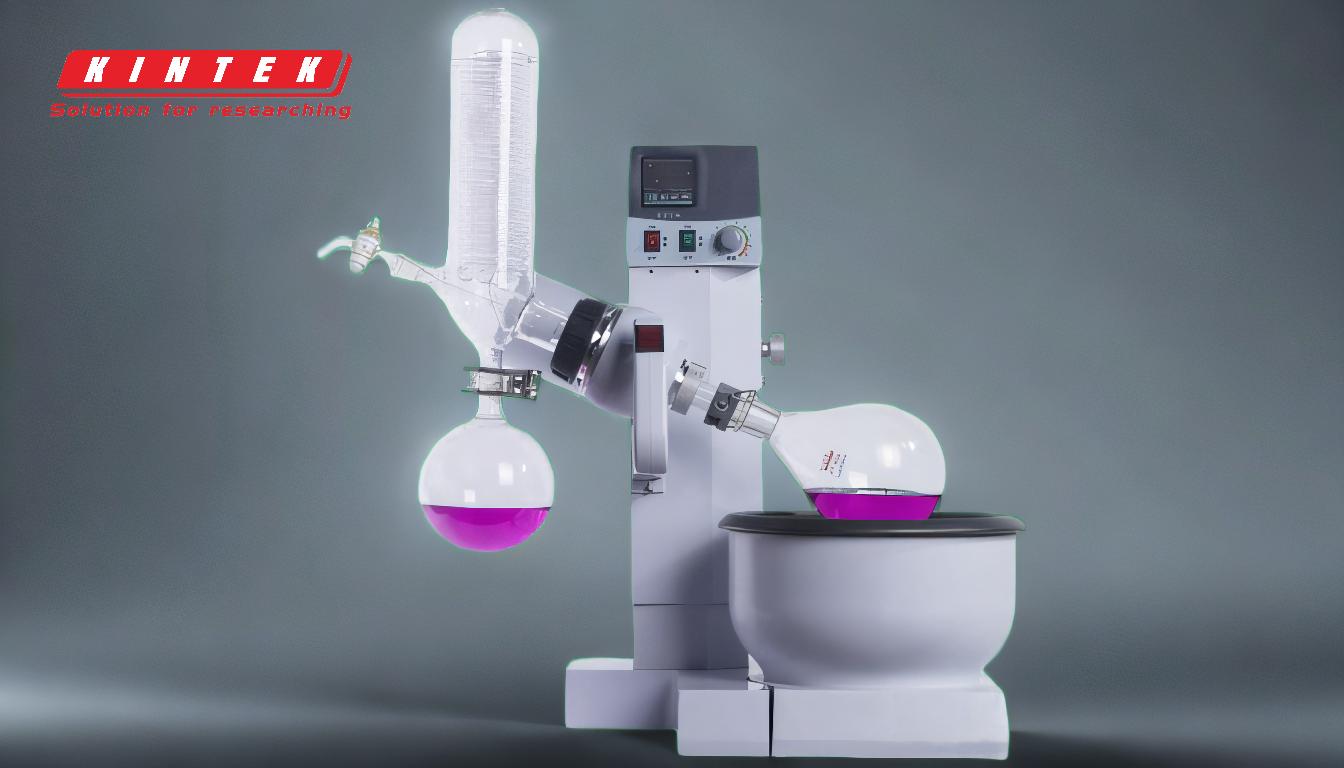
-
Contamination Risks:
- Crucible Impurities: Similar to thermal evaporation, ATFEs can face contamination issues due to impurities in the crucible or other components. For high-temperature operations, graphite crucibles might be necessary, which can introduce carbon contamination into the material.
- Material Compatibility: Certain materials may react with the evaporator's components, leading to contamination or degradation of the product.
-
Cleaning and Sanitization Challenges:
- Complex Structure: The intricate design of ATFEs makes them difficult to clean thoroughly, increasing the risk of cross-contamination between batches.
- Sanitization Costs: Regular sanitization is essential but can be time-consuming and costly, especially in industries requiring high purity standards.
-
Handling Specific Sample Types:
- Foaming Samples: ATFEs are not ideal for foaming samples unless specialized defoamers or condensers are used, which adds to the complexity and cost.
- Boiling and Bumping: Similar to rotary evaporators, ATFEs can experience boiling or bumping, leading to sample loss. Mitigation strategies include adjusting vacuum strength, temperature, or using additives, but these solutions may not always be effective.
-
Operational and Maintenance Costs:
- High Initial Investment: ATFEs are expensive to purchase and install, making them less accessible for smaller operations.
- Energy Consumption: They often require significant energy input, leading to high operational costs.
- Maintenance Requirements: Regular maintenance is necessary to ensure optimal performance, adding to the total cost of ownership.
-
Limitations in Surface Coverage and Uniformity:
- Complex Surfaces: ATFEs may struggle to provide uniform coverage on complex or irregular surfaces without specialized fixturing.
- Large-Scale Uniformity: Achieving consistent film thickness over large areas can be challenging, limiting their use in applications requiring high precision.
-
Energy Efficiency and Heat Load:
- High Radiant Heat Loads: ATFEs can generate significant radiant heat, which may require additional cooling systems, increasing energy consumption and costs.
- Vacuum Requirements: The need for large-volume vacuum chambers further adds to energy demands and operational complexity.
-
Film Quality and Stress:
- Impurity Levels: ATFEs may produce films with higher impurity levels compared to other physical vapor deposition (PVD) methods.
- Film Stress: The films produced can exhibit moderate stress, which may affect their performance in certain applications.
-
Single-Sample Nature:
- Batch Processing: ATFEs typically process one sample at a time, which can be inefficient for high-throughput applications.
- Sample Loss: The risk of sample loss due to bumping or boiling is a significant drawback, particularly for valuable or limited-quantity samples.
In conclusion, while agitated thin film evaporators offer several advantages, their disadvantages must be carefully considered. Potential contamination, cleaning challenges, handling limitations, high costs, and energy inefficiencies are critical factors that can impact their suitability for specific applications. Equipment purchasers should weigh these drawbacks against their operational needs and explore alternative solutions if necessary.
Summary Table:
Disadvantage | Details |
---|---|
Contamination Risks | Crucible impurities, material compatibility issues |
Cleaning Challenges | Complex structure, high sanitization costs |
Handling Specific Samples | Foaming samples, boiling/bumping risks |
Operational Costs | High initial investment, energy consumption, maintenance requirements |
Surface Coverage | Struggles with complex surfaces, large-scale uniformity |
Energy Efficiency | High radiant heat loads, vacuum requirements |
Film Quality | Higher impurity levels, moderate film stress |
Single-Sample Processing | Inefficient for high-throughput, risk of sample loss |
Need help selecting the right equipment for your needs? Contact our experts today to explore alternatives!