Batch reactors, while versatile and widely used in laboratory and small-scale production settings, come with several significant disadvantages. These include high labor costs, challenges in scaling up production, long idle times during operations, limited instrumentation, inconsistent product quality, and safety risks such as explosions. Additionally, batch reactors are generally more suited for homogeneous reactions, limiting their applicability in more complex industrial processes. These drawbacks make them less efficient and cost-effective compared to continuous flow reactors, which offer higher yields, better control, and lower manufacturing costs.
Key Points Explained:
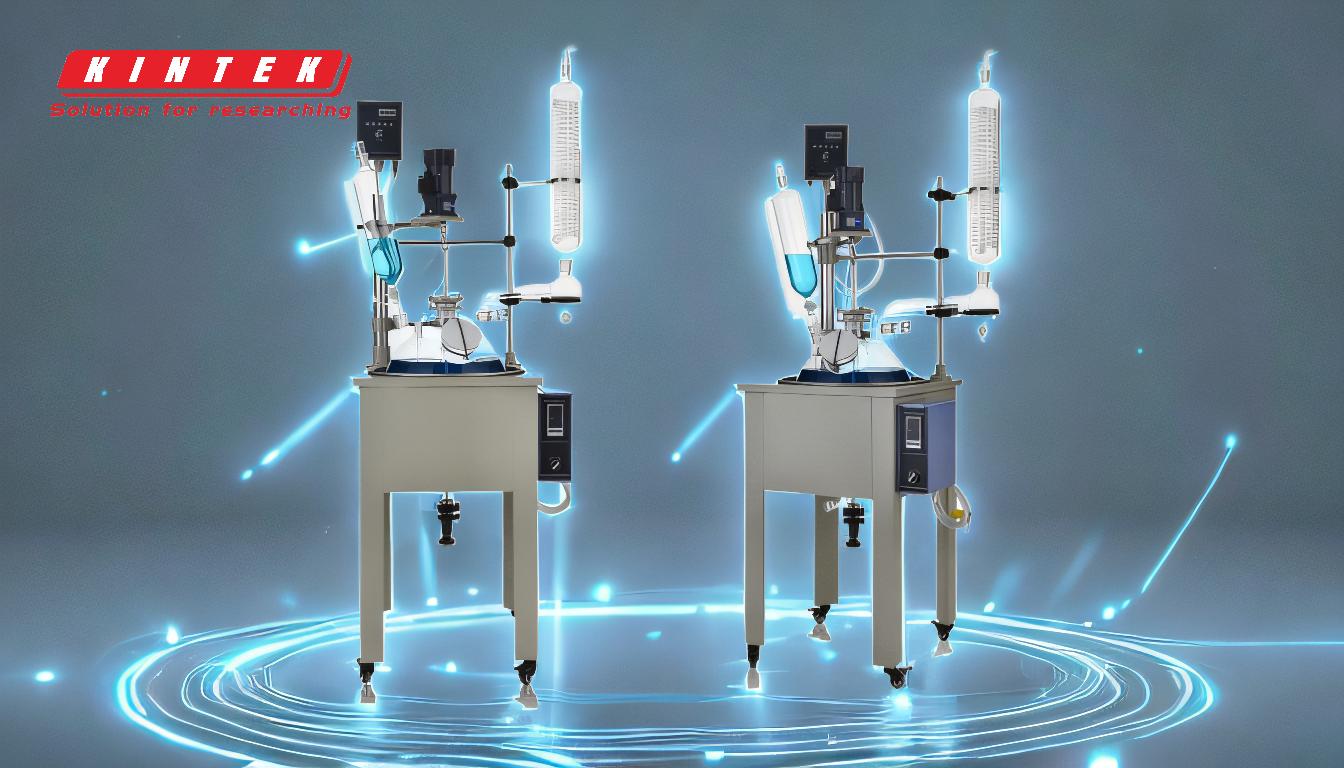
-
High Labor Costs per Unit Production
- Batch reactors require significant manual intervention for tasks such as charging, discharging, and cleaning. This increases labor costs, especially when compared to continuous flow reactors, which are more automated and require less human oversight.
- The repetitive nature of batch processes also leads to inefficiencies, as workers must perform the same tasks multiple times for each batch.
-
Difficulty in Maintaining Large-Scale Production
- Batch reactors are not well-suited for large-scale industrial production due to their limited capacity and the need for frequent start-stop cycles.
- Scaling up production with batch reactors often involves using multiple reactors, which increases costs and complexity. Continuous flow reactors, in contrast, are designed for high-volume production and can operate continuously without interruptions.
-
Long Idle Times During Charging and Discharging
- A significant portion of the production cycle in batch reactors is spent on non-productive tasks, such as loading reactants, heating or cooling the system, and unloading products.
- These idle times reduce overall efficiency and throughput, making batch reactors less suitable for time-sensitive or high-demand production processes.
-
Lack of Instrumentation and Control
- Batch reactors often lack advanced instrumentation and control systems, making it difficult to monitor and optimize reaction conditions in real time.
- This can lead to inconsistencies in product quality and reduced process reliability, as operators have less control over variables like temperature, pressure, and mixing.
-
Poor Product Quality and Consistency
- Due to the lack of precise control and the inherent variability between batches, batch reactors often produce products with inconsistent quality.
- This is particularly problematic in industries where product uniformity is critical, such as pharmaceuticals or specialty chemicals.
-
Risks of Explosion During Emptying
- Batch reactors can pose safety risks, especially during the emptying phase, when residual reactants or byproducts may react unpredictably.
- The design of batch reactors is not optimized to handle powerful explosions, making them less safe compared to continuous flow reactors, which are engineered to manage high-pressure and high-temperature conditions more effectively.
-
Limited Applicability to Homogeneous Reactions
- Batch reactors are primarily suited for homogeneous reactions, where reactants and products are in a single phase (e.g., liquid or gas).
- They are less effective for heterogeneous reactions, which involve multiple phases (e.g., solid-liquid or gas-liquid), further limiting their versatility in industrial applications.
-
Higher Fabrication and Operational Costs
- While batch reactors may save on initial fabrication costs due to their simpler design, their operational inefficiencies and higher labor requirements often result in greater long-term costs.
- Continuous flow reactors, despite their higher initial investment, offer lower manufacturing costs and higher value-to-output (VTO) ratios over time.
-
Inability to Achieve Steady-State Conditions
- Batch reactors do not reach a steady state, meaning that reaction conditions (e.g., temperature, pressure, and concentration) change over time.
- This makes it challenging to control and optimize the reaction, leading to potential inefficiencies and suboptimal product yields.
-
Outdated Design and Technology
- Batch reactors have seen minimal design changes over time, relying on traditional methods that lack the advancements seen in continuous flow reactors.
- This limits their ability to compete with modern reactor technologies, which offer better performance, higher yields, and improved safety features.
In summary, while batch reactors are simple and versatile, their disadvantages—ranging from high labor costs and poor scalability to safety risks and inconsistent product quality—make them less suitable for modern industrial applications. Continuous flow reactors, with their advanced technology and superior efficiency, are increasingly preferred for large-scale and high-demand production processes.
Summary Table:
Disadvantage | Description |
---|---|
High Labor Costs | Requires significant manual intervention, increasing operational costs. |
Poor Scalability | Not ideal for large-scale production due to frequent start-stop cycles. |
Long Idle Times | Non-productive tasks like charging and discharging reduce efficiency. |
Limited Instrumentation | Lack of real-time monitoring and control leads to inconsistent results. |
Inconsistent Product Quality | Variability between batches affects product uniformity. |
Safety Risks | Explosion risks during emptying due to unpredictable reactions. |
Limited to Homogeneous Reactions | Less effective for complex, multi-phase reactions. |
Higher Operational Costs | Long-term inefficiencies outweigh initial cost savings. |
No Steady-State Conditions | Reaction conditions change over time, making optimization difficult. |
Outdated Technology | Lacks advancements seen in modern continuous flow reactors. |
Discover how continuous flow reactors can solve your production challenges—contact us today!