Blown film extrusion, while widely used in the production of plastic films, has several disadvantages that can impact its efficiency and suitability for certain applications. The process is complex, making it difficult to control film thickness accurately, and it is prone to various production issues. Additionally, the manufacturing rates for blown films are generally lower compared to cast films, which can affect productivity. These challenges can lead to increased costs and reduced quality, making it essential for manufacturers to carefully consider these drawbacks when choosing a film production method.
Key Points Explained:
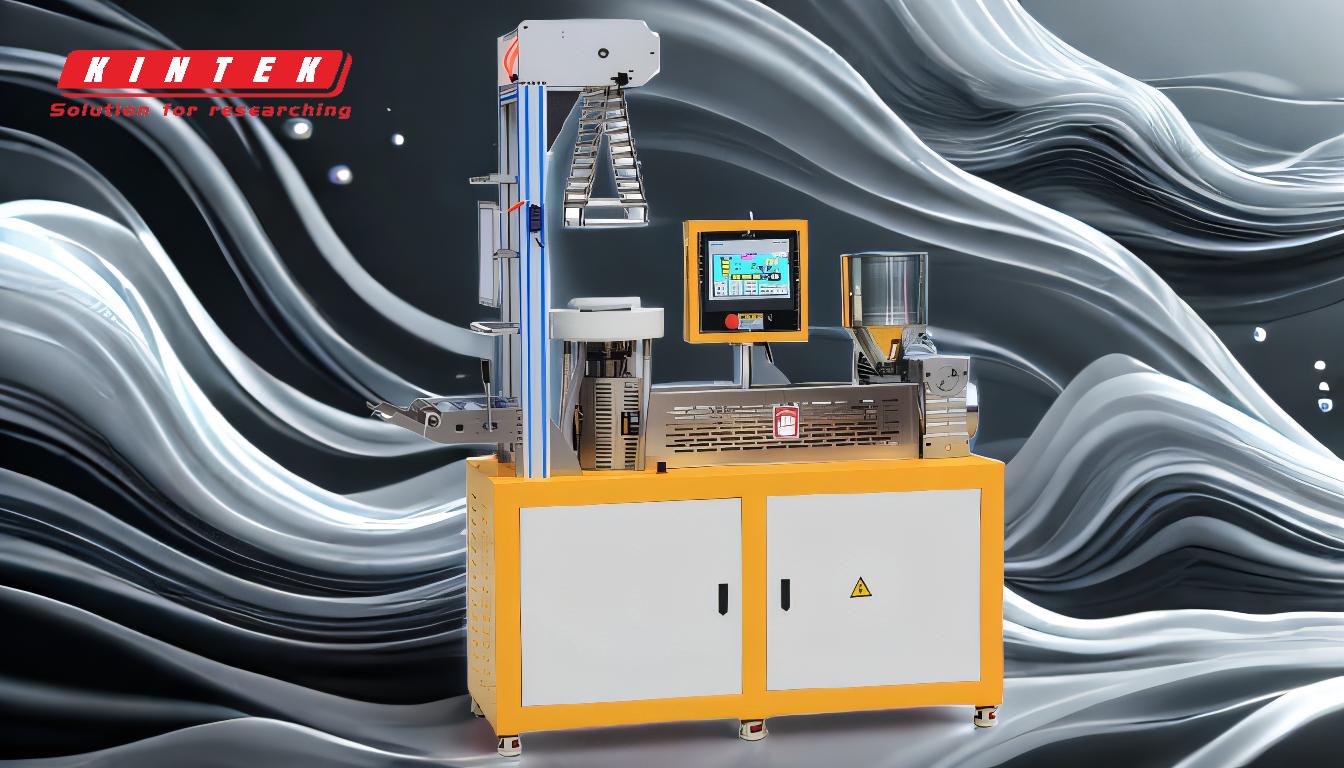
-
Difficulty in Controlling Film Thickness:
- Explanation: One of the primary disadvantages of blown film extrusion is the difficulty in maintaining precise control over the film's thickness. The process involves extruding a molten polymer through a circular die, which is then inflated into a bubble and cooled. The thickness of the film can vary due to fluctuations in the extrusion process, such as changes in temperature, pressure, or the rate of extrusion. This lack of precision can result in uneven film thickness, which can affect the film's performance and suitability for specific applications.
-
Complexity of the Process:
- Explanation: Blown film extrusion is a highly complex method that involves multiple steps and variables. The process requires careful coordination of various factors, including the extrusion rate, cooling rate, and bubble inflation. Any deviation in these parameters can lead to defects in the film, such as wrinkles, gels, or uneven surfaces. The complexity of the process also means that it requires skilled operators and sophisticated equipment, which can increase the overall cost of production.
-
Higher Risk of Production Issues:
- Explanation: Due to the intricate nature of blown film extrusion, there is a higher risk of encountering production issues. Common problems include bubble instability, which can cause the film to tear or collapse, and variations in film properties, such as tensile strength or barrier properties. These issues can lead to increased waste and lower yields, further impacting the cost-effectiveness of the process.
-
Lower Manufacturing Rates Compared to Cast Films:
- Explanation: Blown film extrusion typically has lower manufacturing rates compared to cast film extrusion. Cast film extrusion involves extruding the polymer through a flat die onto a chilled roll, which allows for faster cooling and higher production speeds. In contrast, blown film extrusion requires the film to be cooled gradually as it is inflated into a bubble, which slows down the production process. This difference in manufacturing rates can make blown film extrusion less efficient for high-volume production.
-
Impact on Cost and Quality:
- Explanation: The combination of difficulty in controlling film thickness, the complexity of the process, higher risk of production issues, and lower manufacturing rates can lead to increased costs and reduced quality. Manufacturers may need to invest in additional quality control measures or more advanced equipment to mitigate these issues, which can further drive up production costs. Additionally, the potential for defects and inconsistencies in the film can affect its performance and marketability.
In summary, while blown film extrusion is a versatile and widely used method for producing plastic films, it comes with several disadvantages that can impact its efficiency, cost-effectiveness, and the quality of the final product. Manufacturers must carefully weigh these drawbacks against the benefits of the process when deciding on the most appropriate method for their specific needs.
Summary Table:
Disadvantage | Explanation |
---|---|
Difficulty in Controlling Film Thickness | Uneven thickness due to fluctuations in temperature, pressure, or extrusion rate. |
Complexity of the Process | Requires skilled operators and advanced equipment, increasing production costs. |
Higher Risk of Production Issues | Bubble instability and defects like wrinkles or tears can lead to increased waste. |
Lower Manufacturing Rates | Slower production compared to cast films, impacting efficiency for high volumes. |
Impact on Cost and Quality | Higher costs and potential defects reduce overall quality and marketability. |
Struggling with blown film extrusion challenges? Contact our experts today for tailored solutions!