Sputtering, while a widely used technique for thin-film deposition, has several notable disadvantages that can impact its efficiency, cost, and suitability for certain applications. These drawbacks include low deposition rates, high substrate heating, difficulties in combining with lift-off processes, contamination risks, and high capital expenses. Additionally, sputtering is less effective for insulating materials and organic solids, and it often requires complex equipment and careful control of process parameters. Understanding these limitations is crucial for equipment and consumable purchasers to make informed decisions.
Key Points Explained:
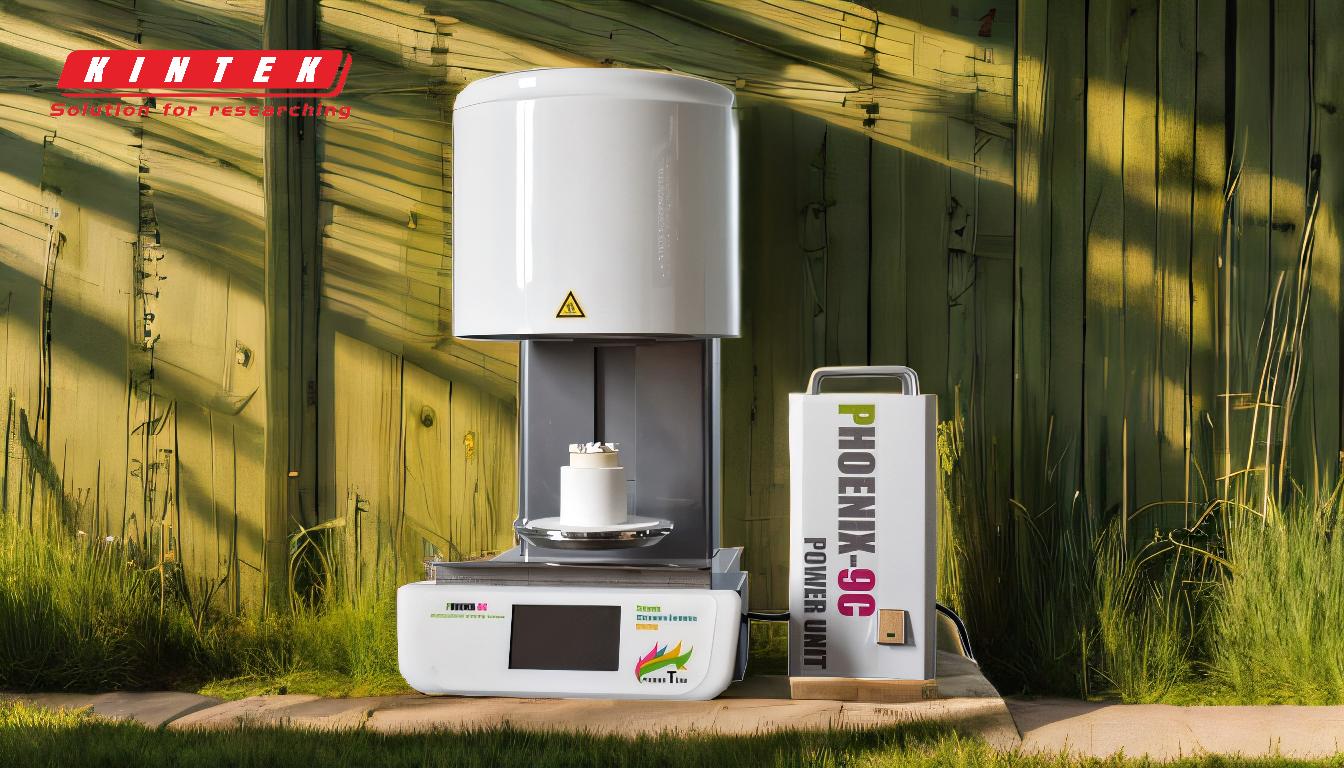
-
Low Deposition Rates:
- Sputtering typically has lower deposition rates compared to other methods like thermal evaporation. This can be a significant drawback when high throughput is required.
- For example, materials such as SiO2 have particularly low deposition rates, which can slow down production processes.
-
High Substrate Heating Effects:
- The sputtering process generates significant heat, which can lead to high substrate temperatures. This can be problematic for temperature-sensitive materials or when precise thermal control is necessary.
- High substrate temperatures can also cause thermal stress and affect the quality of the deposited film.
-
Difficulty with Insulating Materials:
- Sputtering is not well-suited for insulating materials because they can accumulate charge, leading to arcing and other issues that disrupt the deposition process.
- This limitation necessitates the use of alternative methods or additional equipment to handle insulating materials effectively.
-
Challenges in Combining with Lift-Off Processes:
- The diffuse transport characteristic of sputtering makes it difficult to achieve full shadowing, which is essential for lift-off processes used in film structuring.
- This can lead to contamination problems and complicate the patterning of thin films.
-
Contamination Risks:
- Sputtering operates under a lesser vacuum range compared to evaporation, which increases the risk of introducing impurities into the substrate.
- Gaseous contaminants can be activated in the plasma, further increasing the risk of film contamination.
-
High Capital Expenses:
- The equipment required for sputtering is often complex and expensive, leading to high initial capital costs.
- Maintenance and operational costs can also be significant, adding to the overall expense.
-
Material Degradation:
- Organic solids and other sensitive materials can be easily degraded by ionic bombardment during the sputtering process.
- This limits the range of materials that can be effectively deposited using sputtering.
-
Complex Equipment and Process Control:
- Sputtering systems often require high-pressure devices and careful control of process parameters, such as gas composition in reactive sputter deposition.
- The complexity of the equipment and the need for precise control can increase the difficulty and cost of operation.
-
Inefficient Material Use:
- Sputtering targets are often expensive, and the process can be inefficient in terms of material use.
- Most of the energy incident on the target becomes heat, which must be removed, further adding to the inefficiency.
-
Uniformity Issues:
- The deposition flux distribution in sputtering is often non-uniform, requiring the use of moving fixtures to achieve uniform film thickness.
- This can complicate the deposition process and affect the quality of the final film.
By understanding these disadvantages, purchasers can better evaluate whether sputtering is the right choice for their specific needs and explore alternative methods if necessary.
Summary Table:
Disadvantage | Description |
---|---|
Low Deposition Rates | Slower compared to methods like thermal evaporation, especially for materials like SiO2. |
High Substrate Heating | Generates significant heat, causing thermal stress and affecting temperature-sensitive materials. |
Difficulty with Insulators | Insulating materials accumulate charge, leading to arcing and process disruptions. |
Lift-Off Process Challenges | Diffuse transport complicates film structuring and increases contamination risks. |
Contamination Risks | Lesser vacuum range increases impurities; plasma activates gaseous contaminants. |
High Capital Expenses | Complex and expensive equipment with significant maintenance and operational costs. |
Material Degradation | Organic solids and sensitive materials degrade due to ionic bombardment. |
Complex Equipment & Control | Requires high-pressure devices and precise parameter control, increasing operational difficulty. |
Inefficient Material Use | Expensive targets and energy inefficiency, as most energy becomes heat. |
Uniformity Issues | Non-uniform deposition flux requires moving fixtures for uniform film thickness. |
Need help choosing the right thin-film deposition method? Contact our experts today for tailored solutions!