Sputtering is a widely used thin film deposition technique, but it comes with several drawbacks that can affect its efficiency, cost, and application suitability. These limitations include issues like film contamination, material selection restrictions, challenges in film thickness control, and difficulties in combining with other processes such as lift-off. Additionally, sputtering can suffer from low deposition rates, high energy costs due to cooling requirements, and complications like overheating in RF sputtering or charge build-up in DC sputtering. Understanding these drawbacks is crucial for optimizing the sputtering process and selecting the appropriate deposition method for specific applications.
Key Points Explained:
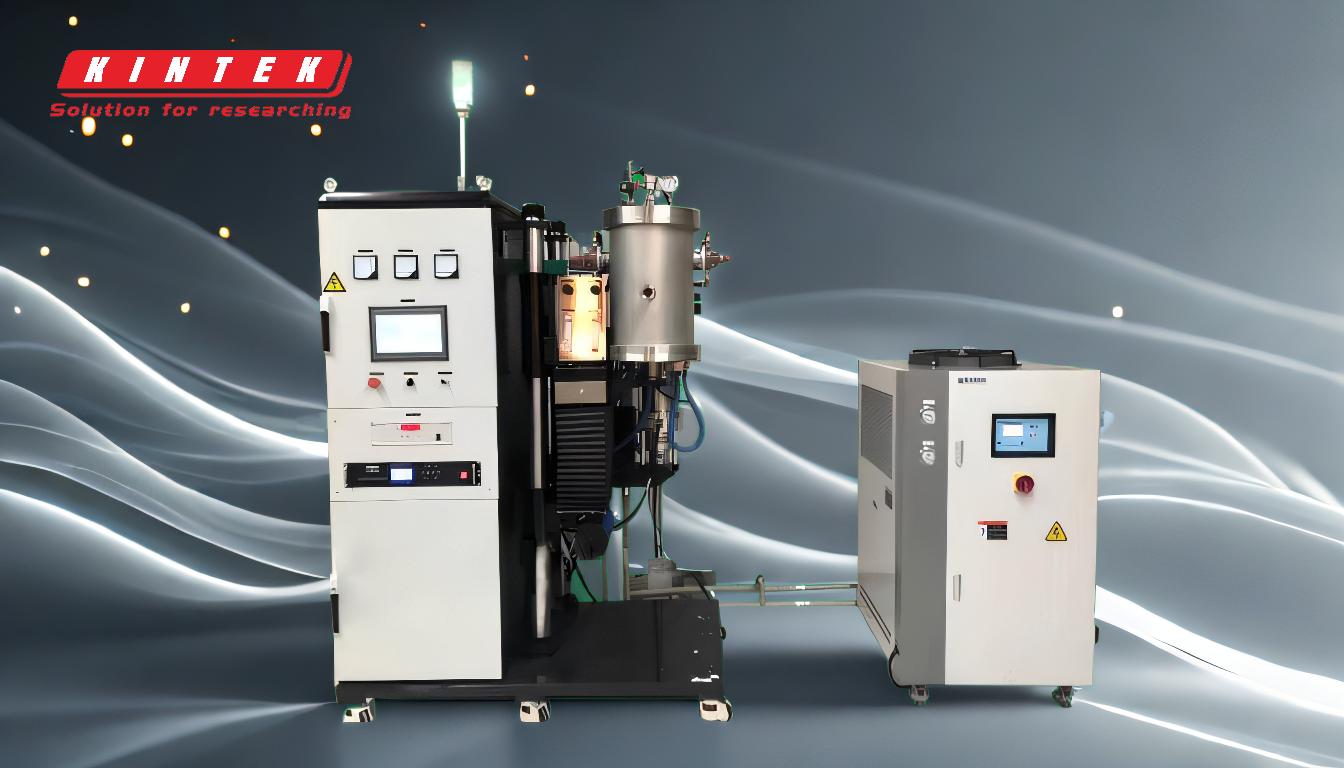
-
Film Contamination:
- Sputtering can lead to film contamination due to the diffusion of impurities from the source material. This is particularly problematic when high-purity films are required, as even minor contamination can degrade the film's performance.
- Inert sputtering gases, such as argon, can also become impurities in the growing film, further complicating the deposition process.
-
Material Selection Restrictions:
- The sputtering process is limited by the melting temperature properties of the target material. Materials with very high melting points can be challenging to sputter, as they may not efficiently dislodge atoms under typical sputtering conditions.
- Insulating materials are particularly difficult to sputter, as they can accumulate charge, leading to process instability.
-
Challenges in Film Thickness Control:
- Sputtering does not allow for precise control of film thickness, which can be a significant drawback in applications requiring highly uniform or specific thicknesses.
- The diffuse transport of atoms during sputtering makes it difficult to achieve sharp interfaces or controlled layer-by-layer growth, which is more easily achieved with other deposition methods like pulsed laser deposition.
-
Low Deposition Rates:
- Sputtering typically has lower deposition rates compared to other thin film deposition techniques. This can increase production time and costs, especially for large-scale or high-throughput applications.
- The need for a cooling system to manage heat generated during sputtering further reduces production rates and increases energy consumption.
-
High Substrate Heating Effects:
- The sputtering process can cause significant heating of the substrate, which may be detrimental to temperature-sensitive materials or substrates.
- Overheating is a common issue in RF sputtering, where higher power inputs are required to generate radio waves, leading to increased thermal stress on the system.
-
Difficulty in Combining with Lift-Off Processes:
- Sputtering is challenging to combine with lift-off processes for film structuring due to the diffuse nature of atom transport. This makes full shadowing impossible, leading to contamination issues and reduced patterning accuracy.
- The inability to achieve sharp shadowing can limit the resolution and precision of patterned films, which is critical in applications like semiconductor manufacturing.
-
Charge Build-Up in DC Sputtering:
- In DC sputtering, the accumulation of charge on the target material can lead to process instability and arcing, which can damage the target and the deposited film.
- This issue is particularly pronounced when sputtering insulating materials, where charge build-up can disrupt the plasma and reduce deposition efficiency.
-
Maintenance and Process Parameter Limitations:
- Sputtering systems require regular maintenance to achieve and maintain pristine thin films. The vacuum system and other components must be kept in optimal condition to avoid contamination and ensure consistent deposition.
- The process parameters in sputtering are often limited by the capabilities of the vacuum system, which can restrict the range of materials and conditions that can be effectively sputtered.
In conclusion, while sputtering is a versatile and widely used thin film deposition technique, it is not without its challenges. Understanding these drawbacks is essential for optimizing the process and selecting the appropriate deposition method for specific applications. By addressing issues such as contamination, material selection, and process control, it is possible to mitigate some of these limitations and improve the overall efficiency and effectiveness of sputtering.
Summary Table:
Drawback | Description |
---|---|
Film Contamination | Impurities from source material or sputtering gases can degrade film quality. |
Material Selection Restrictions | High melting point or insulating materials are difficult to sputter effectively. |
Challenges in Thickness Control | Precise control of film thickness is difficult due to diffuse atom transport. |
Low Deposition Rates | Sputtering has slower rates compared to other deposition methods. |
High Substrate Heating | Substrate heating can damage temperature-sensitive materials. |
Difficulty with Lift-Off | Combining sputtering with lift-off processes is challenging. |
Charge Build-Up in DC Sputtering | Insulating materials can accumulate charge, causing instability. |
Maintenance & Parameter Limits | Regular maintenance and vacuum system limitations affect process efficiency. |
Need help optimizing your sputtering process? Contact our experts today for tailored solutions!