Magnetron sputtering is a widely used technique for thin film deposition, offering advantages such as high-quality coatings and versatility in material selection. However, it also comes with several limitations that can impact its efficiency, cost, and suitability for specific applications. These limitations include poor deposition rates for dielectric materials, high system complexity and cost, substrate heating, plasma instability, low target utilization, and challenges in stoichiometry control. Additionally, magnetron sputtering may not be ideal for liftoff applications due to heating and sidewall coverage issues. Understanding these limitations is crucial for selecting the appropriate deposition method for specific industrial or research needs.
Key Points Explained:
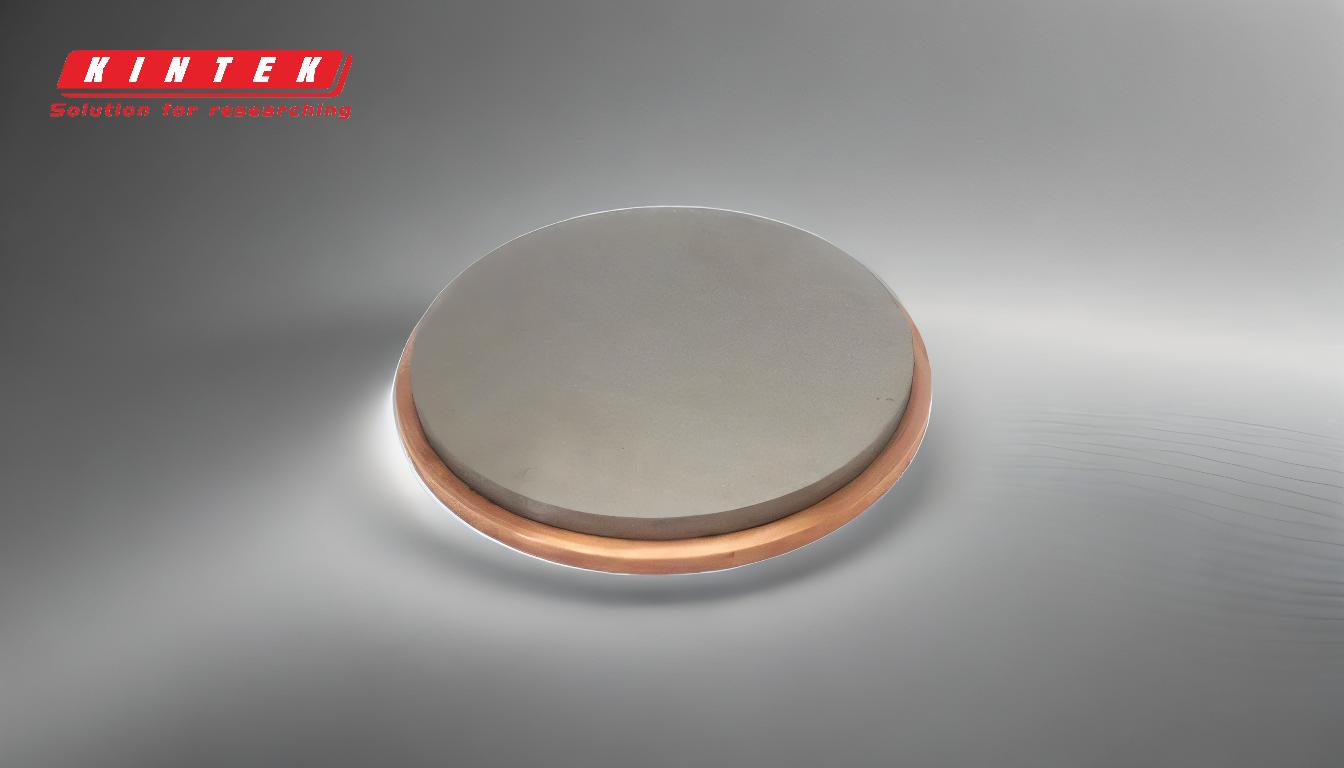
-
Poor Deposition Rate for Dielectrics:
- Magnetron sputtering struggles with achieving high deposition rates for dielectric materials. This is due to the insulating nature of dielectrics, which can lead to charge buildup on the target surface, disrupting the sputtering process. As a result, the deposition rate for dielectric films is often slower compared to conductive materials, making it less efficient for applications requiring thick dielectric layers.
-
High System Cost and Complexity:
- Magnetron sputtering systems are expensive and complex to operate. The need for specialized equipment, such as RF power supplies and matching transformers, adds to the overall cost. RF magnetron sputtering, in particular, requires additional components like transformers between the power supply and the load, increasing both complexity and expense. The inefficiency of RF power supplies (typically less than 70% efficient) further contributes to higher operational costs.
-
Substrate Heating:
- The sputtering process involves the ejection of energetic target material, which can lead to significant heating of the substrate. This heating can be problematic for temperature-sensitive materials or substrates, potentially causing thermal damage or altering the properties of the deposited film. Careful temperature management is required to mitigate this issue.
-
Plasma Instability:
- Magnetron sputtering relies on maintaining a stable plasma for consistent film deposition. However, plasma instability can occur due to factors such as fluctuations in power supply, target material properties, or gas pressure. This instability can lead to inconsistent film quality and deposition rates, affecting the overall reliability of the process.
-
Low Target Utilization:
- The utilization rate of the target material in magnetron sputtering is often low. The sputtering process typically erodes the target in a non-uniform manner, leading to significant material waste. This inefficiency increases the cost of consumables and reduces the overall economic viability of the process, especially for expensive target materials.
-
Challenges in Stoichiometry Control:
- Achieving precise stoichiometry in compound films can be challenging with magnetron sputtering, particularly in reactive sputtering processes. Variations in gas composition, pressure, and power can lead to undesired outcomes, such as off-stoichiometric films or the formation of secondary phases. This limitation is critical for applications requiring specific material properties, such as optical or electronic devices.
-
Unsuitability for Liftoff Applications:
- Magnetron sputtering is less desirable for liftoff applications due to issues with heating and sidewall coverage. The process can cause excessive heating of the photoresist used in liftoff, leading to deformation or premature removal. Additionally, the conformal nature of sputter deposition can result in unwanted sidewall coverage, complicating the liftoff process.
-
Film Contamination:
- The sputtering process can introduce impurities into the deposited film, either from the target material or the sputtering environment. Contamination can degrade the quality of the film, affecting its electrical, optical, or mechanical properties. Careful selection of target materials and stringent control of the sputtering environment are necessary to minimize contamination.
-
Material Selection Limitations:
- The selection of coating materials in magnetron sputtering is limited by their melting temperature and compatibility with the sputtering process. Materials with very high melting points or those that are prone to decomposition under high-energy conditions may not be suitable for sputtering, restricting the range of available materials for specific applications.
-
Directionality and Conformality:
- While magnetron sputtering offers some degree of directionality, it is generally less directional compared to other deposition techniques like evaporation. This can result in less precise control over film thickness and uniformity, particularly for complex geometries. However, the conformal nature of sputter deposition can be advantageous for applications requiring uniform coatings on irregular surfaces.
By understanding these limitations, users can make informed decisions about when and how to use magnetron sputtering, balancing its advantages against its drawbacks for specific applications.
Summary Table:
Limitation | Description |
---|---|
Poor Deposition Rate for Dielectrics | Slow deposition rates for dielectric materials due to charge buildup on the target surface. |
High System Cost and Complexity | Expensive and complex systems requiring specialized equipment like RF power supplies. |
Substrate Heating | Energetic target material ejection causes substrate heating, problematic for sensitive materials. |
Plasma Instability | Fluctuations in power or gas pressure lead to inconsistent film quality and deposition rates. |
Low Target Utilization | Non-uniform target erosion results in material waste and higher costs. |
Challenges in Stoichiometry Control | Difficulties in achieving precise stoichiometry in compound films. |
Unsuitability for Liftoff | Heating and sidewall coverage issues complicate liftoff applications. |
Film Contamination | Impurities from target or environment degrade film quality. |
Material Selection Limitations | Limited by melting temperature and compatibility with sputtering process. |
Directionality and Conformality | Less directional compared to evaporation, but conformal for irregular surfaces. |
Need help choosing the right thin film deposition method? Contact our experts today for tailored solutions!