A batch reactor is a versatile and widely used type of reactor in chemical and biological processes. Its main components include a pressure vessel, an agitator, and an integrated heating/cooling system. Materials such as liquids, solids, vapors, and gases are introduced and discharged through specific ports, while temperature and pressure control are critical due to the lack of a steady state. Batch reactors are commonly made from durable materials like steel, stainless steel, or glass-lined steel, and their sizes can range from less than 1 liter to over 15,000 liters. These reactors are ideal for small-scale production and processes involving biological materials.
Key Points Explained:
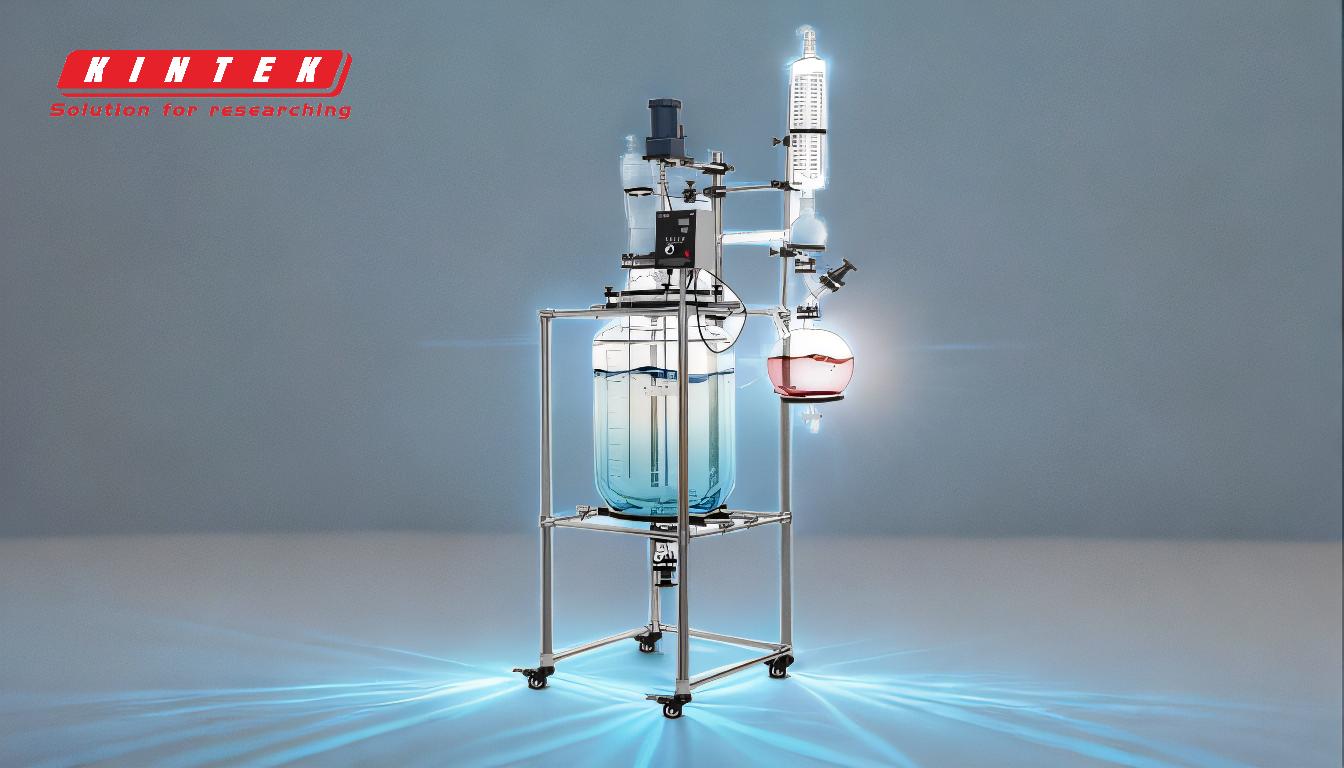
-
Pressure Vessel
- The pressure vessel is the core component of a batch reactor, designed to contain the reactants and withstand the internal pressure generated during the reaction.
- It is typically made from materials such as steel, stainless steel, glass-lined steel, glass, or exotic alloys, depending on the chemical compatibility and reaction conditions.
- The size of the vessel can vary significantly, ranging from less than 1 liter for laboratory-scale reactors to over 15,000 liters for industrial applications.
-
Agitator
- The agitator is a mechanical device used to mix the reactants, ensuring homogeneity and promoting efficient heat and mass transfer.
- It is particularly important for reactions involving viscous liquids or solid-liquid mixtures.
- The design of the agitator (e.g., paddle, propeller, or turbine) depends on the specific requirements of the reaction.
-
Heating/Cooling System
- Batch reactors are equipped with an integrated heating/cooling system to maintain the desired reaction temperature.
- This system is crucial for controlling exothermic or endothermic reactions and ensuring optimal reaction conditions.
- Common methods include jacketed vessels, internal coils, or external heat exchangers.
-
Material Input/Output Ports
- Liquids and solids are typically charged into the reactor through connections in the top cover.
- Vapors and gases are discharged through top connections, while liquids are usually drained from the bottom.
- These ports are designed to facilitate easy loading and unloading of materials while maintaining a sealed environment.
-
Sensor Ports
- Batch reactors often include ports for sensors to monitor critical parameters such as temperature, pressure, pH, and reactant concentration.
- These sensors provide real-time data, enabling precise control of the reaction process.
-
Applications and Advantages
- Batch reactors are ideal for small-scale production, research and development, and processes involving biological materials (e.g., enzyme production).
- Their simplicity and flexibility make them suitable for a wide range of chemical reactions.
- However, they require careful control of input/output materials, temperature, and pressure due to the lack of a steady state.
By understanding these key components and their functions, equipment and consumable purchasers can make informed decisions when selecting batch reactors for specific applications.
Summary Table:
Component | Description |
---|---|
Pressure Vessel | Contains reactants, withstands internal pressure, made of steel, glass, or alloys. |
Agitator | Mixes reactants for homogeneity, heat, and mass transfer; design varies by need. |
Heating/Cooling | Maintains reaction temperature via jacketed vessels, coils, or heat exchangers. |
Material Ports | Input/output for liquids, solids, vapors, and gases; ensures sealed environment. |
Sensor Ports | Monitors temperature, pressure, pH, and concentration for precise control. |
Applications | Ideal for small-scale production, R&D, and biological material processing. |
Discover the perfect batch reactor for your needs—contact our experts today!