Batch reactors are widely used in industries such as food, pharmaceuticals, and chemicals due to their versatility, ease of operation, and suitability for small-scale production. They offer high conversion rates per unit volume, flexibility in operating conditions, and low initial costs. However, they also have notable drawbacks, including high labor costs, inefficiency in large-scale production, long idle times, and potential safety risks. Understanding the pros and cons of batch reactors is crucial for selecting the right equipment for specific applications.
Key Points Explained:
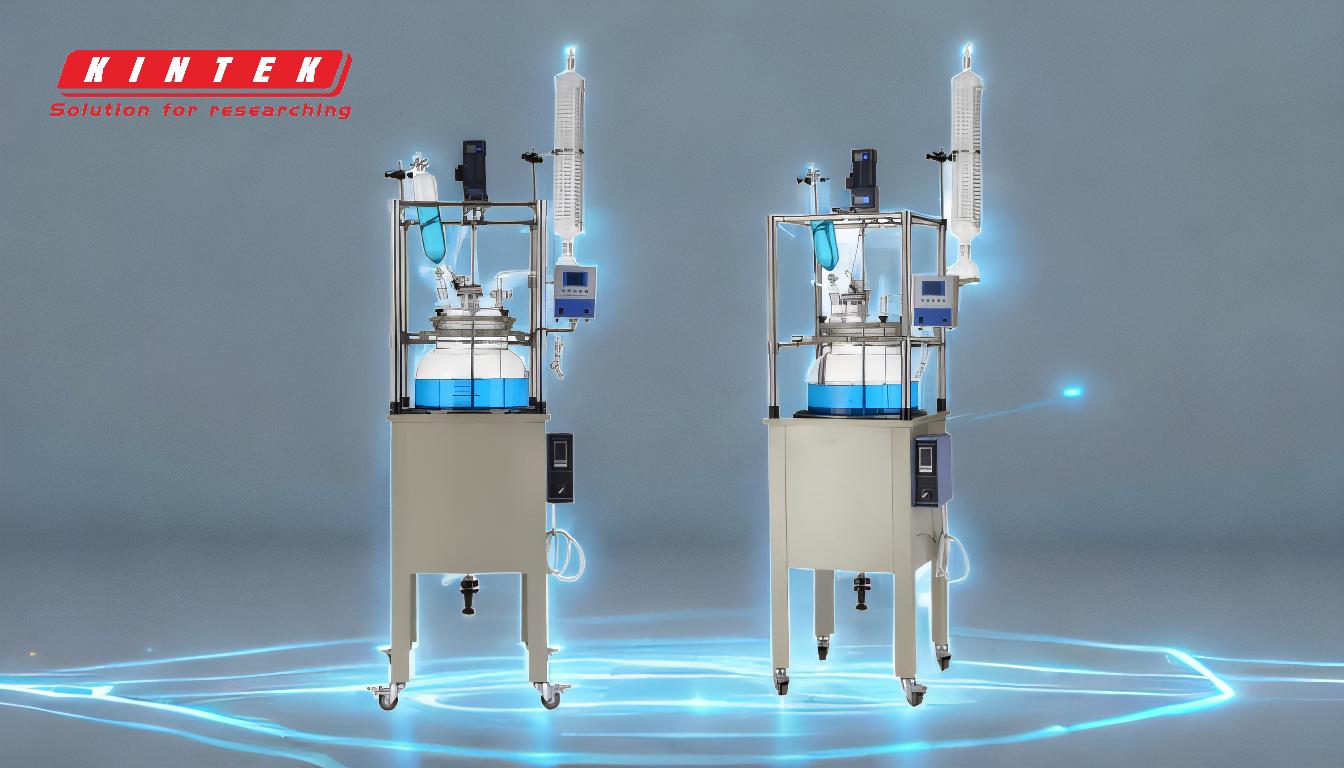
1. Advantages of Batch Reactors
- High Conversion per Unit Volume: Batch reactors are efficient in achieving high conversion rates, making them ideal for reactions where maximizing yield is critical.
- Ease of Cleaning: Their design allows for straightforward cleaning between batches, which is essential in industries like pharmaceuticals and food processing to prevent cross-contamination.
- Low Cost: Batch reactors generally have lower initial capital costs compared to continuous reactors, making them accessible for small-scale and intermediate production.
- Versatility: A single batch reactor can handle multiple operations without breaking containment, which is particularly beneficial for processing toxic or highly potent compounds.
- Flexibility in Operating Conditions: They can accommodate a wide range of temperatures, pressures, and reaction times, making them suitable for diverse applications.
- Suitability for Small-Scale Production: Batch reactors are ideal for small-scale and intermediate production, as well as for use in developing countries where infrastructure may be limited.
- No Redesign Required During Optimization: They allow for process optimization without the need for redesigning the reactor, saving time and resources.
2. Disadvantages of Batch Reactors
- High Labor Costs: Batch reactors require significant manual intervention for charging, discharging, and cleaning, leading to higher labor costs per unit of production.
- Difficulty in Large-Scale Production: They are less efficient for large-scale production due to the need for repeated batch cycles, which can be time-consuming and resource-intensive.
- Long Idle Times: The process of charging and discharging materials results in long idle times, reducing overall productivity.
- Lack of Instrumentation: Batch reactors often have limited instrumentation, making it challenging to monitor and control the reaction process precisely.
- Poor Product Quality: Inconsistent reaction conditions between batches can lead to variations in product quality.
- Safety Risks: The process of emptying batch reactors, especially for volatile or explosive materials, can pose significant safety risks.
- Limited to Homogeneous Reactions: Batch reactors are generally preferred for homogeneous reactions, limiting their applicability in more complex processes.
3. Applications of Batch Reactors
- Food and Pharmaceutical Industries: Batch reactors are widely used in these industries due to their ability to handle sensitive materials and maintain strict hygiene standards.
- Toxic or Potent Compounds: Their containment capabilities make them suitable for processing toxic or highly potent compounds without risking contamination.
- Small-Scale and Intermediate Production: They are ideal for producing small quantities of specialized products, such as custom chemicals or pharmaceuticals.
4. Considerations for Equipment Purchasers
- Scale of Production: Batch reactors are best suited for small-scale or intermediate production. For large-scale operations, continuous reactors may be more efficient.
- Labor Availability: The high labor costs associated with batch reactors should be weighed against the availability and cost of skilled labor.
- Safety Requirements: Purchasers should consider the safety risks, especially when dealing with volatile or explosive materials, and ensure proper safety measures are in place.
- Process Flexibility: If the production process requires frequent changes or optimization, batch reactors offer the necessary flexibility without requiring significant redesign.
- Product Quality Consistency: For industries where product quality consistency is critical, the limitations of batch reactors in maintaining uniform conditions should be carefully evaluated.
In conclusion, batch reactors offer significant advantages in terms of versatility, flexibility, and cost-effectiveness for small-scale and intermediate production. However, their limitations in large-scale production, labor intensity, and potential safety risks must be carefully considered. Equipment purchasers should evaluate their specific production needs, labor availability, and safety requirements to determine whether batch reactors are the right choice for their operations.
Summary Table:
Aspect | Advantages | Disadvantages |
---|---|---|
Conversion Efficiency | High conversion per unit volume | Limited to homogeneous reactions |
Cost | Low initial capital costs | High labor costs |
Versatility | Handles multiple operations without breaking containment | Inefficient for large-scale production |
Flexibility | Accommodates wide temperature, pressure, and reaction time ranges | Long idle times between batches |
Cleaning | Easy to clean, ideal for sensitive industries | Poor product quality due to inconsistent conditions |
Safety | Suitable for toxic or potent compounds | Safety risks during emptying, especially with volatile materials |
Applications | Ideal for food, pharmaceuticals, and small-scale production | Limited instrumentation for precise control |
Need help selecting the right reactor for your needs? Contact our experts today for personalized advice!