Chemical reactors are essential equipment in chemical engineering, used to facilitate chemical reactions under controlled conditions. They come in various types, each designed for specific applications and operating conditions. The main types include Plug Flow Reactors (PFR), Continuous Stirred-Tank Reactors (CSTR), Batch Reactors, Catalytic Reactors, and Semi-batch Reactors. Additionally, reactors can be constructed from materials like glass or stainless steel, depending on the chemical process requirements. Lab-scale reactors, such as stirred, high-pressure, and mini reactors, are also widely used for research and development. Custom configurations, like those designed for biofuels research, highlight the versatility of reactors in addressing diverse industrial needs.
Key Points Explained:
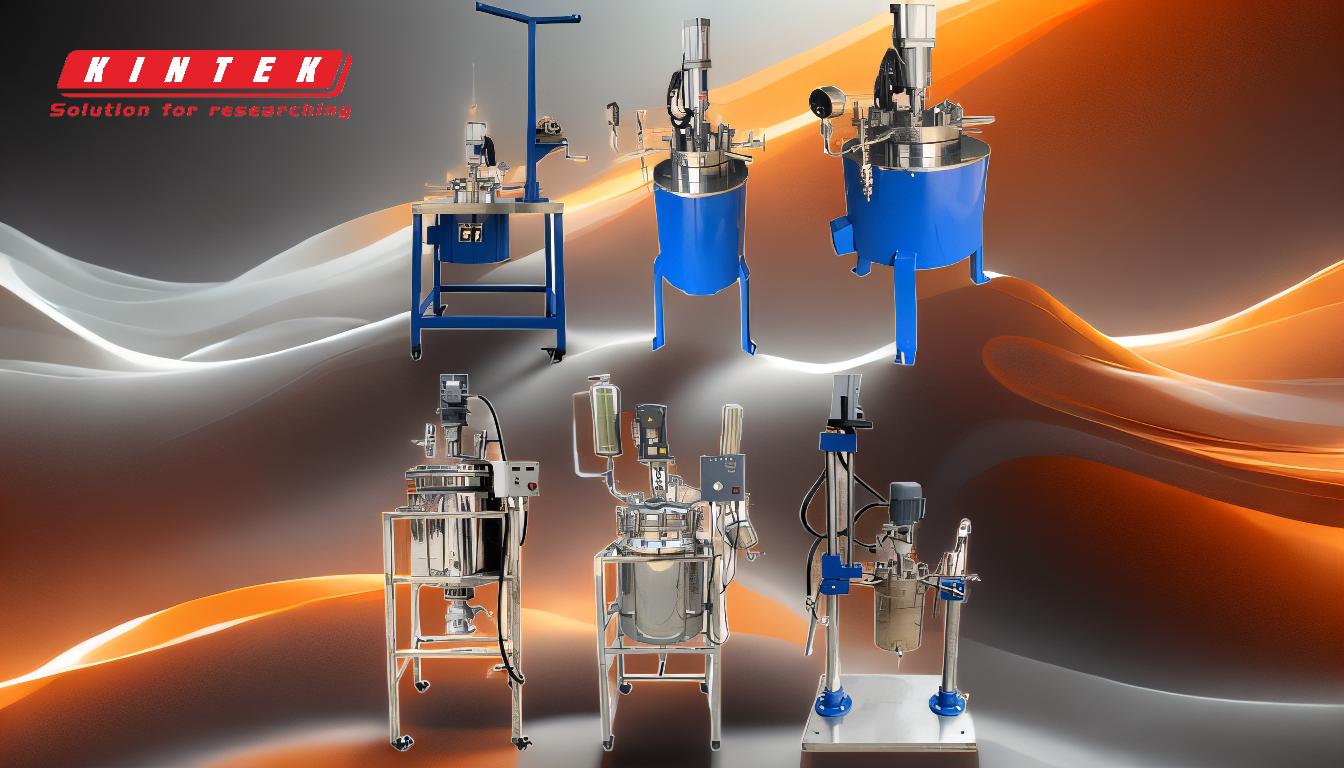
-
Types of Chemical Reactors:
- Plug Flow Reactor (PFR): Ideal for continuous processes where reactants flow through a tube, allowing for a steady-state reaction with minimal back-mixing.
- Continuous Stirred-Tank Reactor (CSTR): Features continuous input and output of materials, with constant stirring to maintain uniform composition and temperature.
- Batch Reactor: Operates in a closed system where all reactants are added at the start, and the reaction proceeds without further input until completion.
- Catalytic Reactor: Designed to house catalysts that speed up chemical reactions, often used in petrochemical and pharmaceutical industries.
- Semi-batch Reactor: Combines features of batch and continuous reactors, allowing for controlled addition of reactants during the process.
-
Materials Used in Reactors:
- Glass Reactors: Commonly used in laboratories due to their transparency, chemical resistance, and ease of cleaning. Examples include glass jacketed reactors and filter reactors.
- Stainless Steel Reactors: Preferred for industrial applications due to their durability, high-temperature resistance, and ability to handle corrosive substances.
-
Lab-Scale Reactors:
- Stirred Reactors: Equipped with agitators to ensure uniform mixing and heat distribution.
- High-Pressure Reactors: Designed to handle reactions requiring elevated pressures, often used in research involving gases or supercritical fluids.
- Mini Reactors: Compact versions used for small-scale experiments and process optimization.
-
Custom Configurations:
- Reactors can be tailored for specific applications, such as biofuels research, where specialized designs are needed to handle unique reaction conditions and materials.
-
Applications of Reactors:
- Extraction and Winterization: Used to separate desired compounds from raw materials.
- Distillation and Post-Processing: Facilitate purification and refinement of chemical products.
- Homogenization: Ensure uniform mixing of components in a mixture.
- Stand-Alone Extraction Vessels: Serve as independent units for specific extraction processes.
By understanding the different types, materials, and applications of reactors, chemical engineers can select the most appropriate reactor for their specific needs, ensuring efficient and safe chemical processes.
Summary Table:
Category | Details |
---|---|
Types of Reactors | Plug Flow Reactor (PFR), Continuous Stirred-Tank Reactor (CSTR), Batch Reactor, Catalytic Reactor, Semi-batch Reactor |
Materials | Glass (transparent, chemical-resistant) and Stainless Steel (durable, high-temperature resistant) |
Lab-Scale Reactors | Stirred, High-Pressure, Mini Reactors |
Applications | Extraction, Winterization, Distillation, Homogenization, Biofuels Research |
Need help selecting the right chemical reactor for your project? Contact our experts today!