Molds are complex organisms with a unique structure that allows them to thrive in various environments. Their primary structural components are hyphae, which are branching, tubular structures that form the main body of the mold. These hyphae are multinucleated and often divided into cell-like units by septa. The collective mass of hyphae is known as a mycelium, which is responsible for nutrient absorption and growth. Understanding the structure of molds is essential for fields such as microbiology, mycology, and industrial applications like food production and bioremediation.
Key Points Explained:
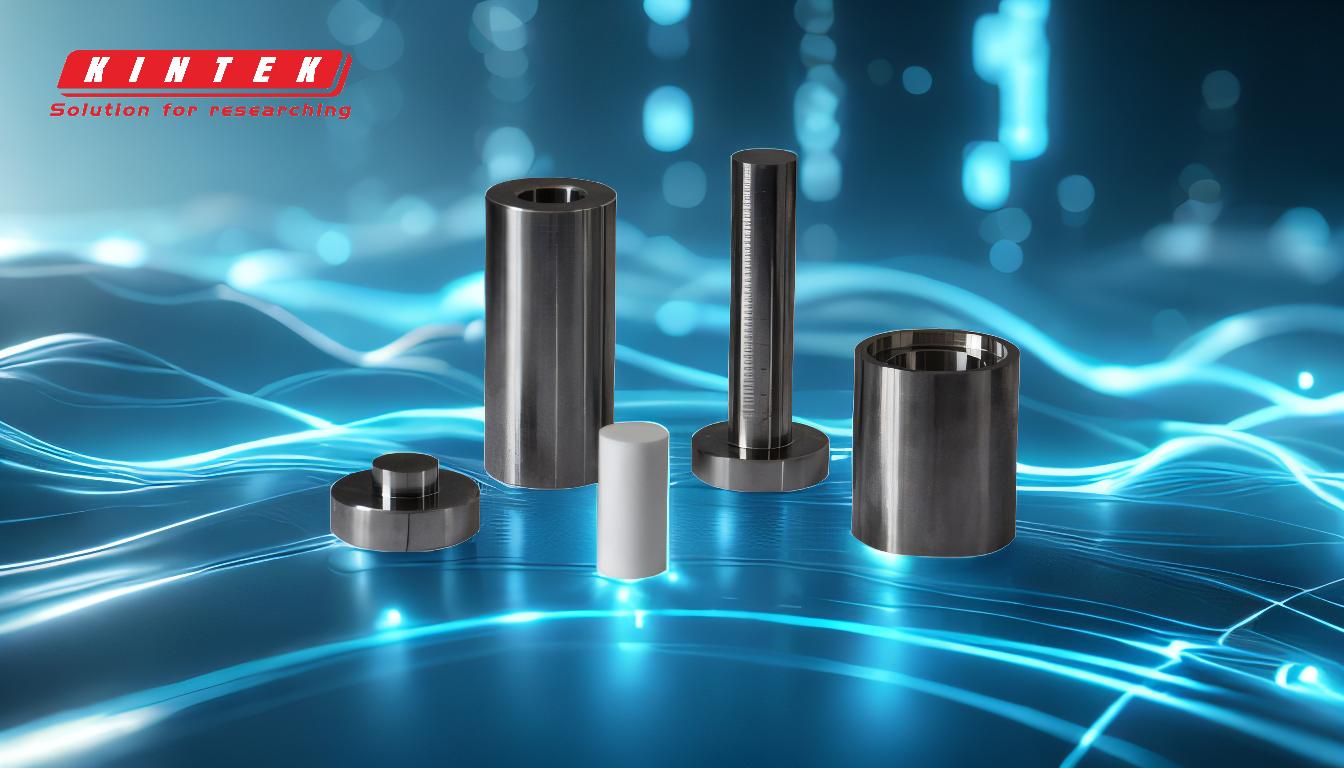
-
Hyphae: The Building Blocks of Molds
- Definition: Hyphae are tubular, branching structures that form the main body of molds. They are typically 2-10 µm in diameter.
- Function: Hyphae are responsible for nutrient absorption and growth. They extend and branch out to explore and colonize new areas.
- Multinucleation: Each hypha contains multiple nuclei, which allows for rapid growth and adaptation to environmental changes.
-
Septa: The Dividing Walls
- Definition: Septa are crosswalls that divide hyphae into cell-like units. Not all hyphae are septate; some are coenocytic, meaning they lack septa and are continuous tubes.
- Function: Septa provide structural support and help compartmentalize the hyphae, which can be important for controlling the flow of nutrients and organelles.
-
Mycelium: The Collective Mass
- Definition: The mycelium is the total mass of hyphae that make up the mold. It is the vegetative part of the fungus.
- Function: The mycelium is responsible for the majority of the mold's growth and nutrient absorption. It spreads out to form a network that can cover large areas.
- Appearance: Mycelium often appears as a fuzzy or cottony mass, which is visible to the naked eye.
-
Reproductive Structures
- Spores: Molds reproduce through spores, which can be produced sexually or asexually. These spores are often released into the environment to colonize new areas.
- Conidia: In some molds, specialized hyphae called conidiophores produce conidia, which are asexual spores that can be dispersed by wind or water.
-
Environmental Adaptations
- Growth Conditions: Molds can grow in a wide range of environments, from soil to decaying organic matter. They are particularly adept at thriving in moist conditions.
- Resilience: The structure of molds allows them to be highly resilient. They can survive in harsh conditions and quickly colonize new areas when conditions become favorable.
-
Industrial and Ecological Importance
- Bioremediation: Molds play a crucial role in breaking down organic matter, making them important for nutrient cycling in ecosystems.
- Food Production: Certain molds are used in the production of foods like cheese and soy sauce. They contribute to flavor development and preservation.
- Pathogenicity: Some molds are pathogenic and can cause diseases in plants, animals, and humans. Understanding their structure helps in developing control measures.
Understanding the structure of molds is fundamental for various scientific and industrial applications. From their hyphal networks to their reproductive strategies, molds are fascinating organisms with complex and adaptive structures.
Summary Table:
Component | Definition | Function |
---|---|---|
Hyphae | Tubular, branching structures (2-10 µm in diameter) forming the mold's body. | Nutrient absorption, growth, and exploration of new areas. |
Septa | Crosswalls dividing hyphae into cell-like units (some hyphae lack septa). | Structural support and compartmentalization of nutrients and organelles. |
Mycelium | Collective mass of hyphae, visible as a fuzzy or cottony mass. | Primary growth and nutrient absorption network. |
Reproductive Structures | Spores (sexual/asexual) and conidia produced by specialized hyphae. | Colonization of new areas through spore dispersal. |
Environmental Adaptations | Thrives in moist conditions, resilient in harsh environments. | Rapid colonization and survival in diverse habitats. |
Industrial Importance | Used in food production (e.g., cheese, soy sauce) and bioremediation. | Nutrient cycling, flavor development, and organic matter breakdown. |
Learn more about the fascinating world of molds and their applications—contact our experts today!