Chemical reactors are essential equipment in chemical processing, designed to facilitate various reactions under controlled conditions. They come in diverse types, each suited for specific applications and operational requirements. The main types of chemical reactors include Plug Flow Reactors, Continuous Stirred-Tank Reactors, Loop Reactors, Batch Reactors, Catalytic Reactors, and Semi-batch Reactors. Additionally, lab-specific reactors such as glass jacketed reactors, filter reactors, stirred reactors, high-pressure reactors, and mini reactors are widely used in research and development. These reactors are employed in processes like extraction, distillation, homogenization, and biofuels research, making them versatile tools in both industrial and laboratory settings.
Key Points Explained:
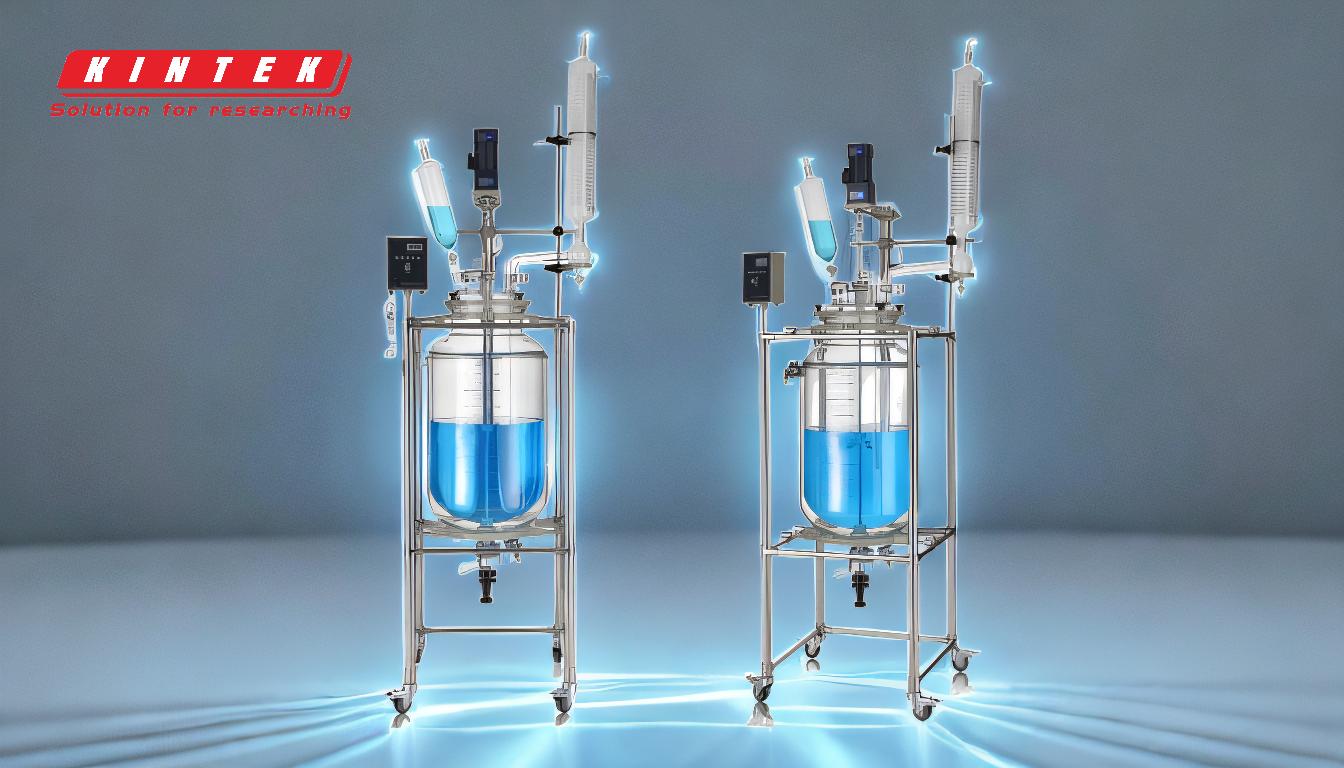
-
Plug Flow Reactor (PFR):
- A PFR is a tubular reactor where reactants flow continuously through the tube, undergoing chemical reactions as they move.
- Ideal for reactions requiring a steady-state flow and precise control over reaction time.
- Commonly used in large-scale industrial processes like petroleum refining and polymerization.
-
Continuous Stirred-Tank Reactor (CSTR):
- A CSTR is a vessel where reactants are continuously fed into the reactor, and the mixture is vigorously stirred to maintain uniformity.
- Suitable for reactions requiring thorough mixing and consistent reaction conditions.
- Often used in industries like pharmaceuticals and food processing.
-
Loop Reactor:
- A loop reactor involves circulating the reaction mixture through a loop, allowing for efficient heat and mass transfer.
- Ideal for exothermic reactions and processes requiring high mixing efficiency.
- Commonly used in polymerization and wastewater treatment.
-
Batch Reactor:
- A batch reactor processes a fixed quantity of reactants in a closed vessel, allowing the reaction to proceed over time.
- Suitable for small-scale production, research, and processes requiring precise control over reaction conditions.
- Widely used in pharmaceuticals, specialty chemicals, and food industries.
-
Catalytic Reactor:
- A catalytic reactor uses a catalyst to accelerate the reaction without being consumed in the process.
- Ideal for reactions requiring specific catalysts, such as hydrogenation, oxidation, and cracking.
- Commonly used in petrochemical and environmental industries.
-
Semi-batch Reactor:
- A semi-batch reactor combines features of batch and continuous reactors, where one reactant is added gradually while others remain in the reactor.
- Suitable for reactions requiring controlled addition of reactants, such as polymerization and crystallization.
- Often used in specialty chemical production.
-
Lab-Specific Reactors:
- Glass Jacketed Reactors: These reactors use a glass vessel with an external jacket for temperature control, making them ideal for laboratory-scale reactions.
- Filter Reactors: Designed for processes requiring filtration, such as crystallization or precipitation.
- Stirred Reactors: Equipped with mechanical stirrers for efficient mixing in small-scale experiments.
- High-Pressure Reactors: Built to withstand high pressures, suitable for reactions like hydrogenation and supercritical fluid extraction.
- Mini Reactors: Compact reactors used for small-scale testing and research.
-
Custom Configurations:
- Reactors can be customized for specific applications, such as biofuels research or specialized chemical processes.
- Custom designs may include unique heating, cooling, or mixing mechanisms tailored to the process requirements.
-
Applications of Reactors:
- Reactors are used in extraction, winterization, distillation, and post-processing.
- They are also employed for homogenizing mixtures and serving as stand-alone extraction vessels.
By understanding the types and applications of chemical reactors, purchasers can select the most suitable equipment for their specific needs, ensuring efficient and effective chemical processing.
Summary Table:
Type of Reactor | Key Features | Common Applications |
---|---|---|
Plug Flow Reactor (PFR) | Continuous flow, precise control over reaction time | Petroleum refining, polymerization |
Continuous Stirred-Tank Reactor (CSTR) | Continuous feed, vigorous stirring for uniformity | Pharmaceuticals, food processing |
Loop Reactor | Efficient heat and mass transfer, high mixing efficiency | Polymerization, wastewater treatment |
Batch Reactor | Fixed quantity processing, precise control over reaction conditions | Pharmaceuticals, specialty chemicals, food |
Catalytic Reactor | Uses catalysts for accelerated reactions | Petrochemicals, environmental industries |
Semi-batch Reactor | Controlled addition of reactants, combines batch and continuous features | Polymerization, crystallization |
Lab-Specific Reactors | Glass jacketed, filter, stirred, high-pressure, and mini reactors for research | Small-scale testing, biofuels research |
Need help selecting the right chemical reactor for your needs? Contact our experts today for personalized advice!