Electronic coating, often referred to as e-coating or electrocoating, is a process where a paint or coating is applied to a conductive surface using electrical current. This method is widely used across various industries due to its efficiency, uniformity, and superior protective qualities. The process involves immersing the object to be coated in a paint bath, where an electric current is applied, causing the paint particles to deposit evenly on the surface. This technique is particularly valued for its ability to provide excellent coverage, adhesion, and corrosion resistance, making it a popular choice in industries such as automotive, aerospace, and electronics.
Key Points Explained:
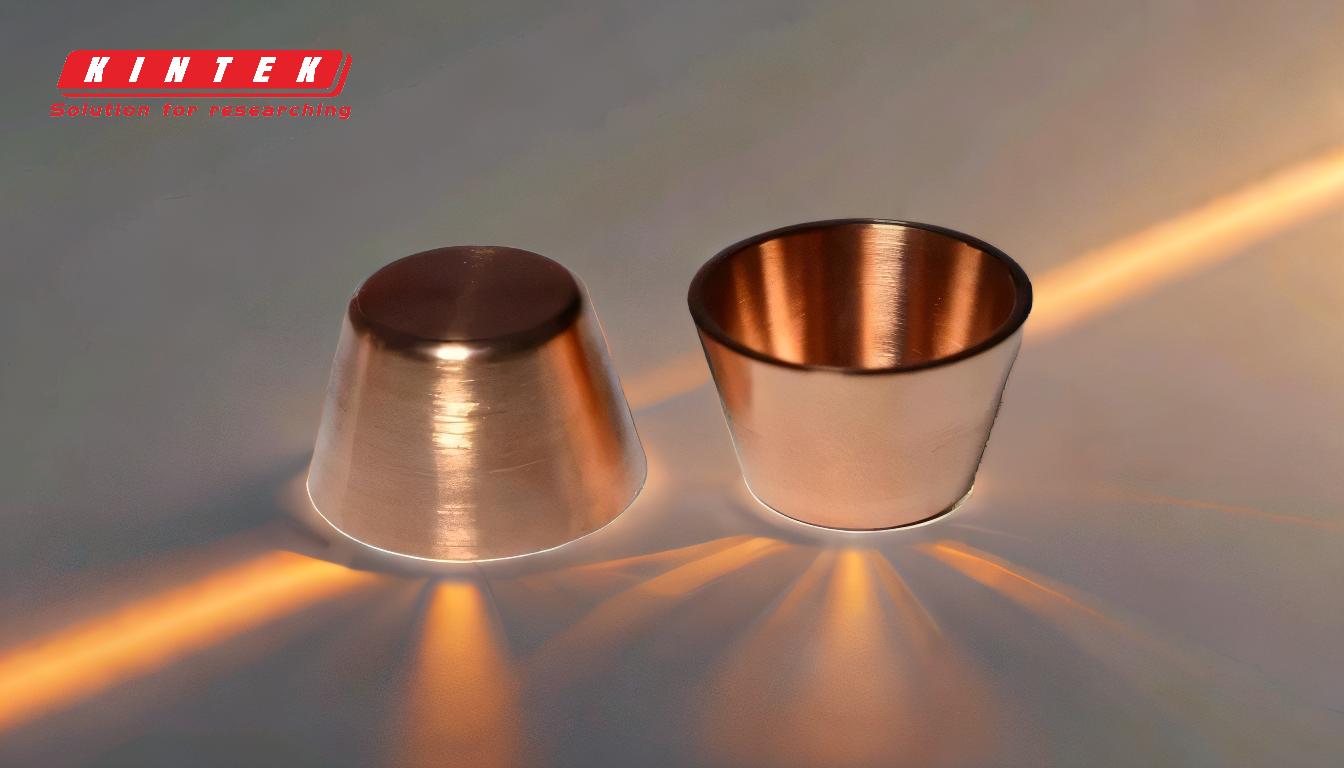
-
Definition and Process of Electronic Coating:
- Electronic coating, or e-coating, is a method of applying paint or coating to a conductive surface using electrical current.
- The process involves immersing the object in a paint bath and applying an electric current, which causes the paint particles to deposit uniformly on the surface.
- This method ensures even coverage and strong adhesion, making it highly effective for protecting metal surfaces.
-
Applications in Various Industries:
- Automotive Industry: E-coating was originally developed for the automotive industry due to its economical nature and superior protective qualities. It is used to coat various metals like aluminum, zinc, brass, and steel, providing excellent corrosion resistance.
- Electronics: Conductive coatings are used to shield electronic devices, especially plastic ones, from electromagnetic interference, enhancing their performance and longevity.
- Aerospace and Medical: Vacuum coating processes are employed in aerospace and medical applications, offering high-performance coatings for critical components.
- General Manufacturing: Coating technology is applied in fields like semiconductors, optoelectronics, and machinery, adding value by enabling the creation of advanced products and generating higher economic value.
-
Types of Coatings and Their Uses:
- Electron Beam Coatings: These are used in a variety of applications, including solid colors for materials like particleboard and medium density fiberboard, low COF coatings for treadmill decking, and flooring coatings that are ESD and anti-skid.
- Special Effects Coatings: These include clear coatings for foil and paper, exterior coatings for signage, and special effects coatings for store fixtures.
- Antimicrobial Coatings: Used in environments where hygiene is critical, these coatings help prevent the growth of bacteria and other microorganisms.
-
Advantages of Electronic Coating:
- Uniform Coverage: The electrical application ensures that the coating is evenly distributed, even on complex shapes and hard-to-reach areas.
- Superior Adhesion: The process results in a strong bond between the coating and the substrate, enhancing durability.
- Corrosion Resistance: E-coating provides excellent protection against corrosion, extending the lifespan of coated products.
- Cost-Effectiveness: The method is economical, especially for large-scale production, due to its efficiency and reduced waste.
-
Future Trends and Innovations:
- Advanced Materials: Ongoing research is focused on developing new coating materials that offer enhanced properties, such as higher conductivity, better thermal resistance, and improved environmental sustainability.
- Automation and Precision: Advances in automation and precision coating technologies are expected to further improve the efficiency and quality of electronic coatings.
- Environmental Considerations: There is a growing emphasis on developing eco-friendly coatings that minimize environmental impact while maintaining high performance.
In summary, electronic coating is a versatile and efficient method of applying protective and functional coatings to various materials. Its applications span multiple industries, offering benefits such as uniform coverage, superior adhesion, and excellent corrosion resistance. As technology advances, we can expect further innovations in coating materials and processes, enhancing their effectiveness and environmental sustainability.
Summary Table:
Aspect | Details |
---|---|
Definition | Applying paint/coating to conductive surfaces using electrical current. |
Applications | Automotive, electronics, aerospace, medical, and general manufacturing. |
Types of Coatings | Electron beam, special effects, antimicrobial coatings. |
Advantages | Uniform coverage, superior adhesion, corrosion resistance, cost-effective. |
Future Trends | Advanced materials, automation, eco-friendly coatings. |
Learn how electronic coating can benefit your industry—contact us today for expert advice!