Reactive sputtering is a specialized thin-film deposition technique that combines the principles of conventional sputtering with chemical reactions to create compound thin films. It involves the use of reactive gases, such as oxygen or nitrogen, which chemically react with the sputtered metal atoms from the target material upon reaching the substrate. This process is widely used in applications requiring precise control over film stoichiometry and structure, such as in the production of optical coatings, semiconductors, and wear-resistant layers. Reactive sputtering is performed in a vacuum chamber with a low-pressure reactive gas atmosphere, making it a versatile and efficient method for depositing oxides, nitrides, and other compound films.
Key Points Explained:
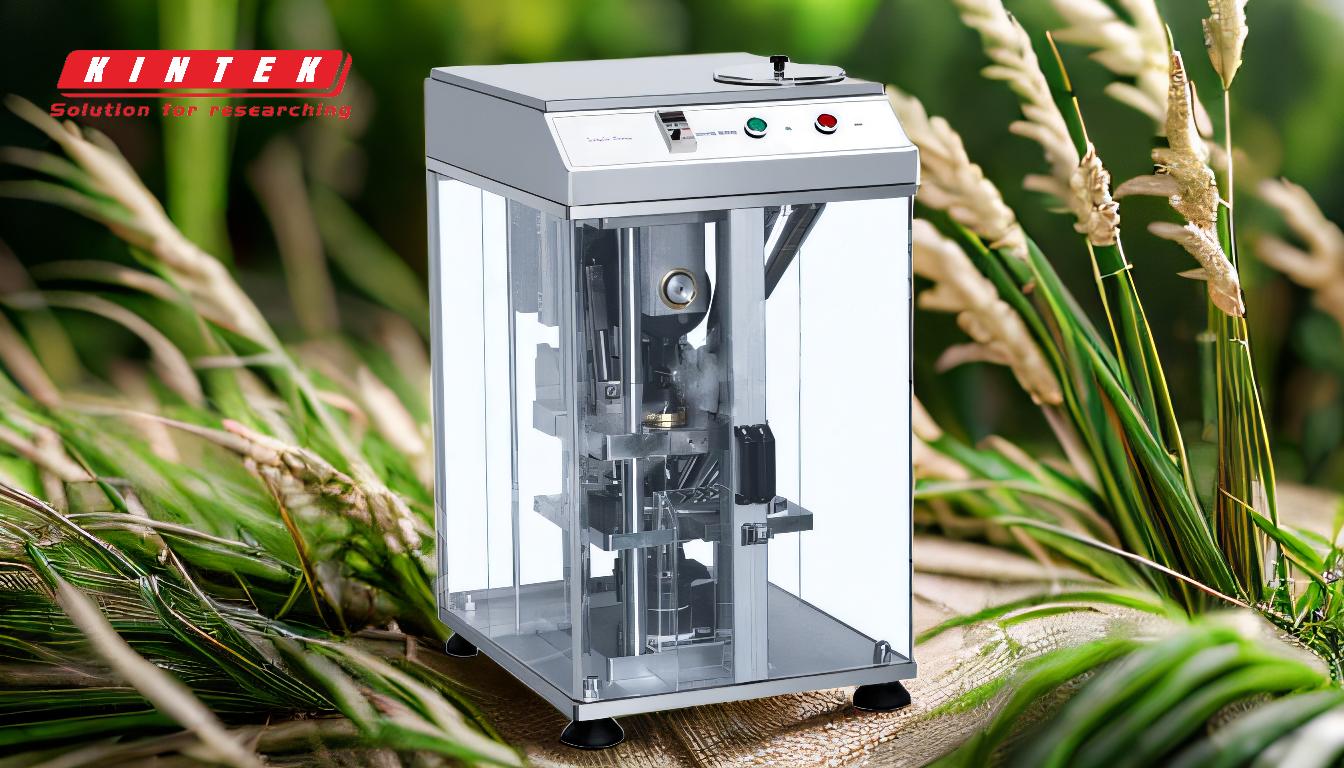
-
Definition and Process of Reactive Sputtering:
- Reactive sputtering is a thin-film deposition process that involves a chemical reaction between sputtered metal atoms from a target material and a reactive gas (e.g., oxygen or nitrogen) introduced into the vacuum chamber.
- The process combines conventional sputtering with chemical vapor deposition (CVD), allowing for the formation of compound thin films directly on the substrate.
-
Key Components and Setup:
- Vacuum Chamber: The process takes place in a vacuum environment to minimize contamination and control the reactive gas pressure.
- Reactive Gases: Gases like oxygen (O₂) or nitrogen (N₂) are introduced to react with the sputtered metal atoms.
- Target Material: A metallic target (e.g., aluminum or titanium) is bombarded by high-energy ions, releasing metal atoms that travel to the substrate.
- Substrate: The surface where the thin film is deposited, often requiring precise control over temperature and surface conditions.
-
Chemical Reactions in Reactive Sputtering:
- The reactive gas chemically reacts with the sputtered metal atoms on the substrate surface, forming compound films such as oxides or nitrides.
- Example: Aluminum (Al) reacts with oxygen (O₂) to form aluminum oxide (Al₂O₃):
[ 4 \text{Al} + 3 \text{O}_2 \rightarrow 2 \text{Al}_2\text{O}_3 ] - This reaction allows for the creation of hard, durable coatings with specific properties.
-
Advantages of Reactive Sputtering:
- Precise Stoichiometry: The process enables precise control over the chemical composition of the deposited film.
- Versatility: It can be used to deposit a wide range of compound films, including oxides, nitrides, and carbides.
- High Deposition Rates: Reactive sputtering often achieves higher deposition rates compared to other methods like RF magnetron sputtering.
- Enhanced Film Properties: The resulting films often exhibit improved hardness, wear resistance, and optical properties.
-
Applications of Reactive Sputtering:
- Optical Coatings: Used to create anti-reflective or reflective layers for lenses, mirrors, and other optical devices.
- Semiconductors: Deposits insulating or conductive layers in semiconductor devices.
- Wear-Resistant Coatings: Produces hard, durable coatings for tools and industrial components.
- Decorative Coatings: Used in applications like watch faces or architectural glass.
-
Comparison with Conventional Sputtering:
- Unlike conventional sputtering, which deposits pure metal films, reactive sputtering creates compound films through chemical reactions.
- The introduction of reactive gases allows for the formation of films with tailored properties, such as increased hardness or specific optical characteristics.
-
Challenges and Considerations:
- Gas Flow Control: Precise control of reactive gas flow is critical to achieving the desired film properties.
- Target Poisoning: Excessive reactive gas can lead to the formation of a compound layer on the target surface, reducing sputtering efficiency.
- Process Optimization: Balancing the reactive gas concentration, sputtering power, and pressure is essential for optimal film quality.
By leveraging the chemical reactivity of gases and the physical sputtering process, reactive sputtering offers a powerful tool for creating high-performance thin films with tailored properties for a wide range of applications.
Summary Table:
Aspect | Details |
---|---|
Definition | Combines sputtering with chemical reactions to create compound thin films. |
Key Components | Vacuum chamber, reactive gases (O₂, N₂), target material, substrate. |
Advantages | Precise stoichiometry, versatility, high deposition rates, enhanced properties. |
Applications | Optical coatings, semiconductors, wear-resistant layers, decorative coatings. |
Challenges | Gas flow control, target poisoning, process optimization. |
Discover how reactive sputtering can enhance your thin-film applications—contact our experts today!