Metal sputtering is a versatile and widely used thin-film deposition technique that involves the ejection of atoms from a solid metal target material due to bombardment by high-energy ions, typically argon ions. These ejected atoms then deposit onto a substrate, forming a thin, uniform coating. This process is conducted in a vacuum chamber to ensure control over the environment and to facilitate the efficient transfer of material. Metal sputtering is utilized across various industries, including microelectronics, solar cells, optoelectronics, and aerospace, for applications such as creating chemically resistant coatings, producing gas-impermeable films, and manufacturing dielectric stacks. The process is highly controllable, enabling the production of precise and high-quality thin films with minimal thermal damage.
Key Points Explained:
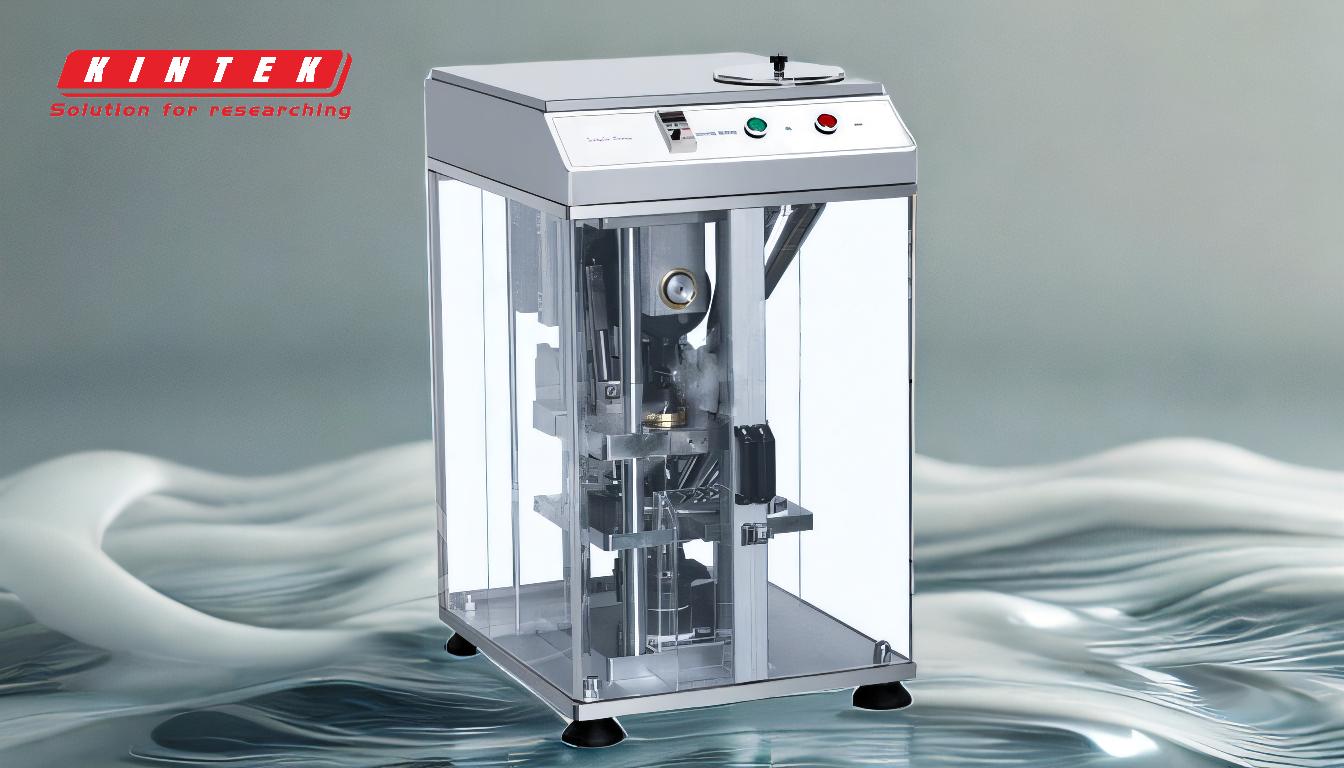
-
Definition of Metal Sputtering:
- Metal sputtering is a physical vapor deposition (PVD) process where atoms are ejected from a solid metal target material due to bombardment by high-energy ions, typically argon ions. These ejected atoms then deposit onto a substrate, forming a thin, uniform coating.
-
Process Mechanism:
- The process begins by creating a vacuum environment in a chamber to remove air and other gases.
- A small amount of argon gas is introduced into the chamber.
- A target material (usually a metal) is placed on one side of the chamber, and a substrate is placed on the opposite side.
- A voltage (DC, radio frequency, or median frequency) is applied, ionizing the argon gas and creating a plasma.
- The argon ions are accelerated towards the negatively charged target material, causing atoms to be ejected from the target due to momentum transfer.
- These ejected atoms travel through the vacuum chamber and deposit onto the substrate, forming a thin film.
-
Applications of Metal Sputtering:
- Semiconductor Industry: Used for creating chemically resistant thin film coatings on semiconductor devices.
- Aerospace and Defense: Applied in the deposition of gadolinium films for neutron radiography.
- Corrosion Protection: Used to create gas-impermeable films that protect corrosion-prone materials.
- Medical Devices: Produces dielectric stacks to electrically isolate surgical tools.
- Microelectronics and Optoelectronics: Used in the production of thin-film solar cells, transparent conductive coatings, and decorative finishes.
-
Advantages of Metal Sputtering:
- Uniform Coatings: The omni-directional deposition of sputtered atoms ensures even coating on complex geometries.
- Minimal Thermal Damage: The process generates less heat compared to other deposition methods, reducing the risk of thermal damage to the substrate.
- Enhanced Secondary Electron Emission: Improves the performance of materials in applications like Scanning Electron Microscopy (SEM).
- Versatility: Can be used with a wide range of materials, including metals, alloys, and compounds.
-
Equipment and Consumables:
- Vacuum Chamber: Essential for maintaining the controlled environment required for the sputtering process.
- Target Material: The metal or alloy that is bombarded to produce the thin film.
- Substrate: The material onto which the thin film is deposited.
- Argon Gas: Used as the sputtering gas due to its inert properties and ability to efficiently ionize.
- Power Supply: Provides the necessary voltage (DC, RF, or MF) to ionize the argon gas and accelerate ions towards the target.
-
Challenges and Considerations:
- Heat Management: The process generates significant heat, requiring specialized chilling systems to prevent damage to the target and substrate.
- Target Erosion: Continuous bombardment can lead to target erosion, necessitating regular replacement or maintenance.
- Process Control: Precise control over parameters such as pressure, voltage, and gas flow is essential to achieve consistent and high-quality coatings.
Metal sputtering is a critical technology in modern manufacturing and research, enabling the development of advanced materials and devices with enhanced performance and durability. Its ability to produce high-quality, uniform thin films makes it indispensable in industries ranging from electronics to aerospace.
Summary Table:
Aspect | Details |
---|---|
Definition | Physical vapor deposition (PVD) process using high-energy ions to eject atoms from a metal target. |
Process Mechanism | Argon gas ionization, plasma creation, and atom deposition onto a substrate. |
Applications | Semiconductor coatings, aerospace films, corrosion protection, medical devices, and solar cells. |
Advantages | Uniform coatings, minimal thermal damage, versatility, and enhanced electron emission. |
Equipment | Vacuum chamber, target material, substrate, argon gas, and power supply. |
Challenges | Heat management, target erosion, and precise process control. |
Discover how metal sputtering can elevate your projects—contact our experts today for tailored solutions!