In the pharmaceutical industry, reactors are essential equipment used for chemical reactions, drug synthesis, and biopharmaceutical production. They provide controlled environments to optimize reaction conditions, enhance yields, and ensure product purity. Reactors come in various types, including high-pressure reactors for accelerating complex molecule production, glass reactors for biopharmaceuticals like monoclonal antibodies and enzymes, and specialized reactors for APIs. These reactors enable precise kinetic control, reduce development time, and support processes like cell culture, fermentation, and downstream processing. Their versatility and adaptability make them indispensable in drug development and manufacturing.
Key Points Explained:
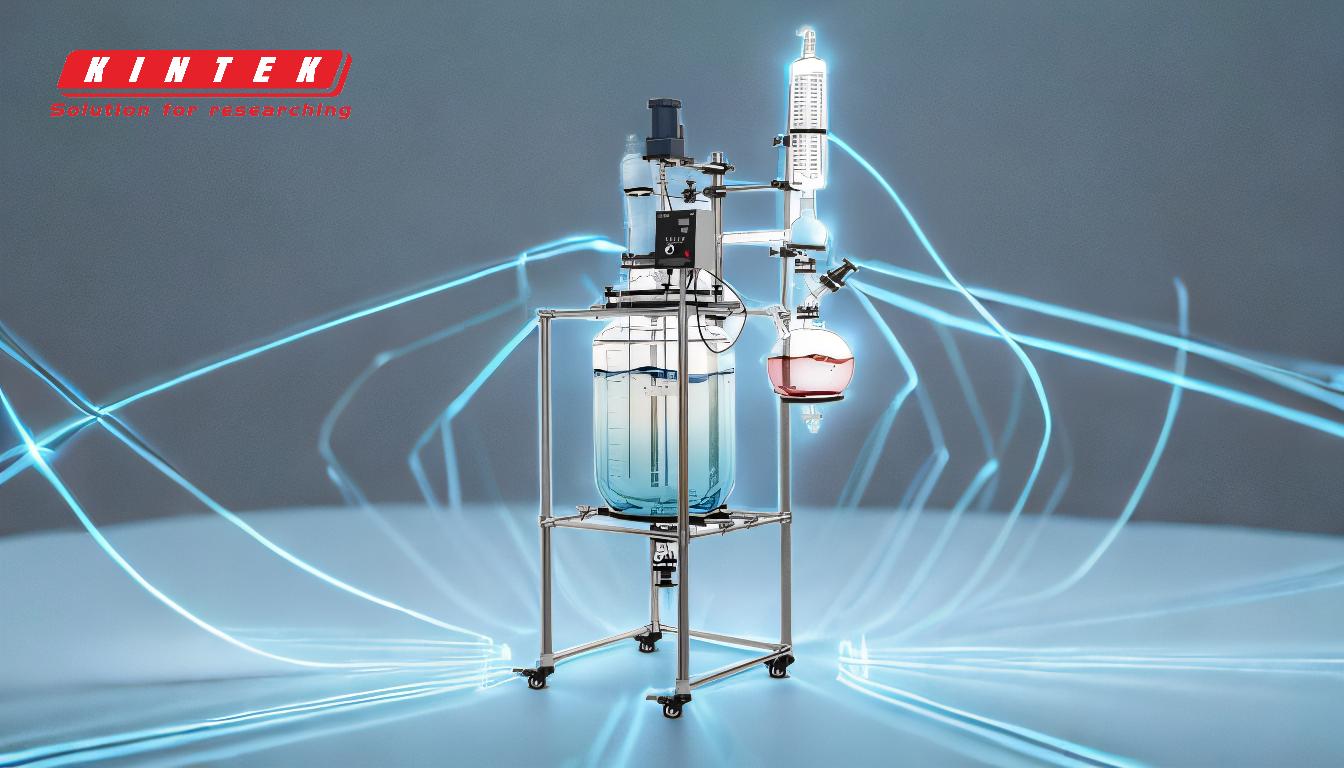
-
Definition and Purpose of Reactors in Pharmaceuticals
- Reactors are specialized vessels designed to facilitate chemical reactions under controlled conditions.
- They are critical for drug synthesis, biopharmaceutical production, and optimizing reaction parameters such as temperature, pressure, and mixing.
- Reactors ensure high yields, product purity, and consistency, which are vital for pharmaceutical manufacturing.
-
Types of Reactors Used in the Pharmaceutical Industry
-
High-Pressure Reactors:
- Used for accelerating the production of complex molecules.
- Enable precise kinetic control, reducing the time required for drug development.
- Ideal for multi-step reactions and high-pressure synthesis.
-
Glass Reactors:
- Commonly used for biopharmaceutical production, including monoclonal antibodies, recombinant proteins, and therapeutic enzymes.
- Provide a clear, controlled environment for cell culture, fermentation, and downstream processing.
- Suitable for drug synthesis, particularly in the production of active pharmaceutical ingredients (APIs).
-
Other Reactor Types:
- Plug Flow Reactor, Continuous Stirred-tank Reactor, Loop Reactor, Batch Reactor, Catalytic Reactor, and Semi-batch Reactor.
- Each type is tailored for specific applications, such as continuous processing or batch production.
-
High-Pressure Reactors:
-
Applications of Reactors in Pharmaceuticals
-
Drug Synthesis:
- Reactors are used to produce APIs and other pharmaceutical compounds.
- They optimize reaction conditions to achieve high yields and purity.
-
Biopharmaceutical Production:
- Glass reactors are essential for producing biopharmaceuticals like proteins, enzymes, and vaccines.
- They support cell culture and fermentation processes, ensuring a controlled environment for growth and production.
-
Process Development:
- Reactors enable researchers to study and scale up reactions from lab to industrial scale.
- They reduce development time by accelerating multi-step reactions and providing precise control over reaction parameters.
-
Drug Synthesis:
-
Benefits of Using Reactors in Pharmaceuticals
-
Precision and Control:
- Reactors allow for precise control over temperature, pressure, and mixing, ensuring optimal reaction conditions.
-
Efficiency:
- High-pressure reactors and continuous flow reactors reduce production time and improve efficiency.
-
Scalability:
- Reactors facilitate the transition from lab-scale experiments to large-scale manufacturing.
-
Versatility:
- Custom configurations and specialized reactors are available for specific applications, such as biofuels research or biopharmaceutical production.
-
Precision and Control:
-
Considerations for Selecting Reactors
-
Material Compatibility:
- Glass reactors are preferred for biopharmaceuticals due to their inert nature and transparency.
- High-pressure reactors are often made of durable materials like stainless steel.
-
Process Requirements:
- The choice of reactor depends on the specific process, such as batch or continuous production.
-
Scalability:
- Reactors must be scalable to accommodate production needs from lab to industrial scale.
-
Customization:
- Custom configurations may be required for specialized applications, such as biofuels or unique drug synthesis processes.
-
Material Compatibility:
-
Future Trends in Pharmaceutical Reactors
-
Automation and Digitalization:
- Increasing use of automated systems and digital controls for enhanced precision and efficiency.
-
Sustainability:
- Development of reactors that minimize waste and energy consumption.
-
Advanced Materials:
- Use of advanced materials to improve durability, compatibility, and performance.
-
Integration with AI and Machine Learning:
- Leveraging AI to optimize reaction conditions and predict outcomes, further reducing development time.
-
Automation and Digitalization:
By understanding the role, types, and applications of reactors in the pharmaceutical industry, stakeholders can make informed decisions to enhance drug development and manufacturing processes.
Summary Table:
Aspect | Details |
---|---|
Types of Reactors | High-Pressure, Glass, Plug Flow, Continuous Stirred-tank, Loop, Batch, Catalytic, Semi-batch |
Key Applications | Drug Synthesis, Biopharmaceutical Production, Process Development |
Benefits | Precision Control, Efficiency, Scalability, Versatility |
Selection Factors | Material Compatibility, Process Requirements, Scalability, Customization |
Future Trends | Automation, Sustainability, Advanced Materials, AI Integration |
Ready to enhance your pharmaceutical processes? Contact our experts today to find the perfect reactor for your needs!