RF and DC sputtering are two widely used physical vapor deposition (PVD) techniques for thin film coating. DC sputtering uses a direct current (DC) power source and is primarily suited for conductive materials like metals, offering high deposition rates and cost-efficiency for large substrates. In contrast, RF sputtering employs an alternating current (AC) power source, typically at 13.56 MHz, and is capable of depositing both conductive and non-conductive (dielectric) materials. RF sputtering is more expensive and has a lower deposition rate, making it ideal for smaller substrates. The key difference lies in their power sources and the types of materials they can process, with RF sputtering overcoming the limitations of DC sputtering when dealing with insulating materials.
Key Points Explained:
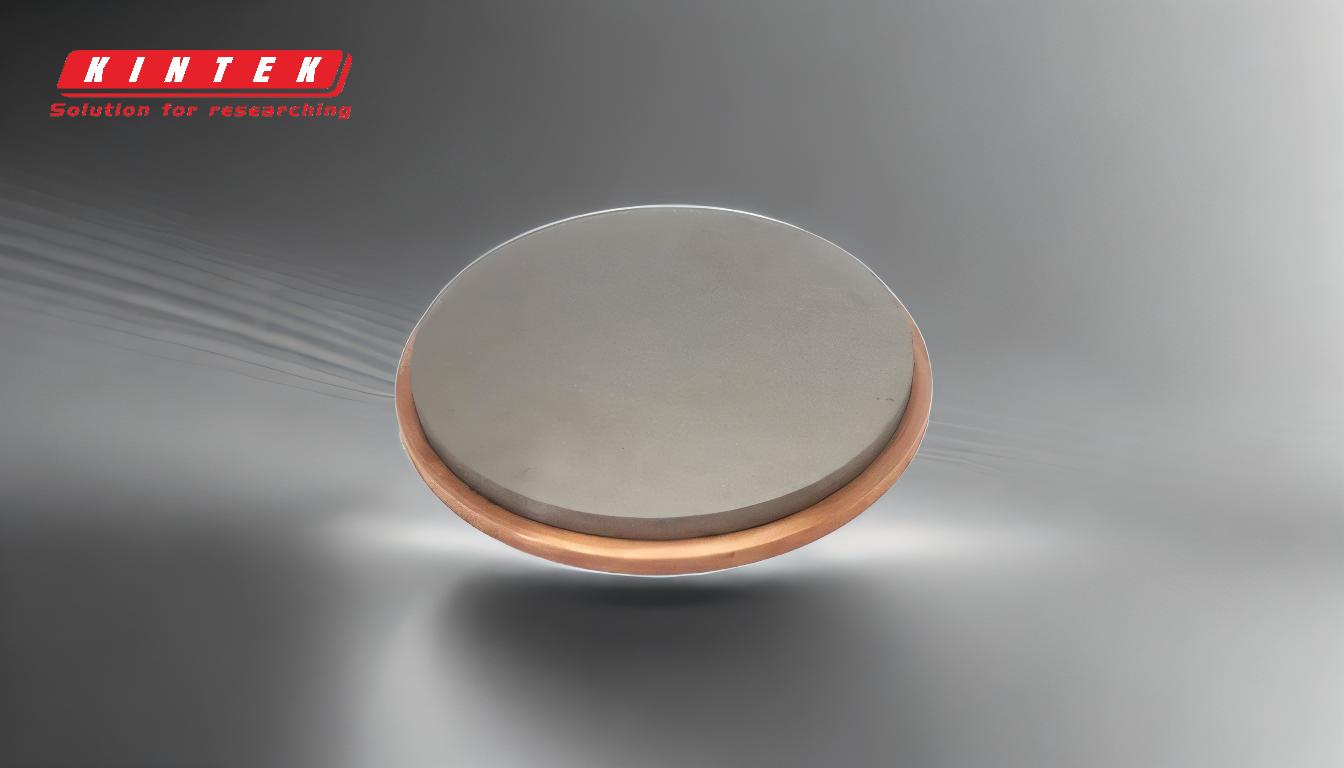
-
Power Source and Mechanism:
- DC Sputtering: Uses a direct current (DC) power source, creating a gaseous discharge where positively charged ions strike the target (cathode) to eject atoms for deposition. The substrate or chamber walls act as the anode. This method is straightforward and effective for conductive materials.
- RF Sputtering: Uses an alternating current (AC) power source, typically at 13.56 MHz, with a cathode (target) and anode connected in series with a blocking capacitor. The alternating voltage prevents charge buildup on insulating targets, enabling the sputtering of non-conductive materials.
-
Material Compatibility:
- DC Sputtering: Best suited for conductive materials like metals. It struggles with dielectric (insulating) materials due to charge accumulation on the target surface, which disrupts the sputtering process.
- RF Sputtering: Can handle both conductive and non-conductive (dielectric) materials. The alternating voltage neutralizes charge buildup on insulating targets, allowing continuous sputtering.
-
Deposition Rate and Cost:
- DC Sputtering: Offers higher deposition rates and is more cost-effective, making it suitable for large-scale production and large substrates.
- RF Sputtering: Has a lower deposition rate and is more expensive due to the complexity of the RF power supply and impedance-matching networks. It is better suited for smaller substrates and specialized applications.
-
System Pressure and Voltage:
- DC Sputtering: Operates at higher pressures and lower voltages compared to RF sputtering.
- RF Sputtering: Requires higher voltages (upwards of 1012 volts) and operates at lower pressures (less than 15 mTorr), making it more complex and energy-intensive.
-
Process Dynamics:
- DC Sputtering: Involves a single-cycle process where ions continuously bombard the target to eject atoms for deposition.
- RF Sputtering: Involves a two-cycle process: during one half-cycle, electrons neutralize positive ions on the target surface, and during the other half-cycle, target atoms are sputtered and deposited on the substrate.
-
Applications:
- DC Sputtering: Ideal for applications requiring high throughput and cost-efficiency, such as coating large metal substrates or producing conductive thin films.
- RF Sputtering: Suitable for specialized applications involving dielectric materials, such as optical coatings, semiconductor devices, and thin-film electronics.
-
Advantages and Limitations:
- DC Sputtering: Advantages include simplicity, high deposition rates, and cost-effectiveness. The main limitation is its inability to handle insulating materials.
- RF Sputtering: Advantages include the ability to sputter insulating materials and better control over film properties. Limitations include higher costs, lower deposition rates, and complexity in operation.
By understanding these key differences, a purchaser can make informed decisions based on the specific requirements of their application, such as material type, substrate size, and production scale.
Summary Table:
Feature | DC Sputtering | RF Sputtering |
---|---|---|
Power Source | Direct Current (DC) | Alternating Current (AC, 13.56 MHz) |
Material Compatibility | Conductive materials (metals) | Conductive & non-conductive materials |
Deposition Rate | High | Lower |
Cost | Cost-effective | More expensive |
Substrate Size | Large substrates | Smaller substrates |
Applications | High-throughput metal coatings | Optical coatings, semiconductors |
Advantages | Simple, fast, cost-efficient | Handles insulating materials |
Limitations | Cannot process insulating materials | Higher cost, complex operation |
Need help choosing the right sputtering technique for your project? Contact our experts today!