RF sputtering is a specialized technique used to deposit thin films, particularly for insulating (non-conductive) materials, by utilizing radio frequency (RF) energy in a vacuum environment. It involves alternating electrical potential at a fixed frequency (typically 13.56 MHz) to prevent charge buildup on the target material, which is critical for insulating targets. The process operates in two cycles: the positive cycle, where electrons are attracted to the target, creating a negative bias, and the negative cycle, where ion bombardment continues, enabling the sputtering of target atoms onto the substrate. This method is widely used in industries like semiconductors and computer manufacturing due to its ability to handle non-conductive materials and produce high-quality thin films.
Key Points Explained:
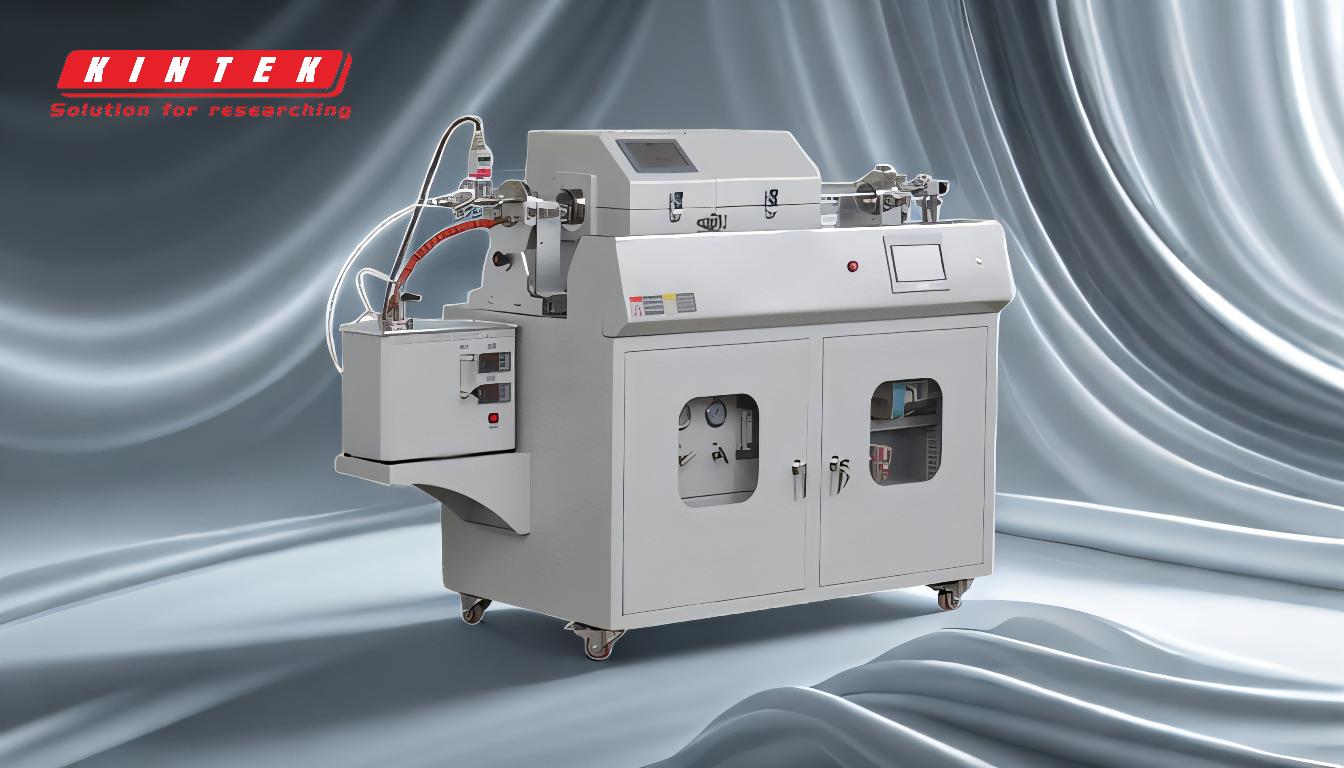
-
Definition and Purpose of RF Sputtering:
- RF sputtering is a thin-film deposition technique that uses radio frequency energy to sputter target materials, especially insulating (non-conductive) ones, onto a substrate.
- It is commonly used in industries such as semiconductors, optics, and computer manufacturing to create precise and high-quality coatings.
-
How RF Sputtering Works:
- The process takes place in a vacuum chamber filled with an inert gas (e.g., argon).
- An RF power source generates an energetic wave at a fixed frequency (typically 13.56 MHz), which ionizes the gas, creating positive ions.
- The target material (cathode) is bombarded by these high-energy ions, causing atoms to be ejected from the target and deposited onto the substrate.
-
The Role of Alternating Electrical Potential:
- RF sputtering alternates the electrical potential between the target and the substrate holder, acting as two electrodes.
- In the positive cycle, the target acts as an anode, attracting electrons and creating a negative bias.
- In the negative cycle, the target acts as a cathode, allowing ion bombardment to continue and ejecting target atoms toward the substrate.
- This alternating potential prevents charge buildup on insulating targets, which is critical for maintaining the sputtering process.
-
Advantages of RF Sputtering:
- Ability to Sputter Insulating Materials: Unlike DC sputtering, RF sputtering can handle non-conductive materials by preventing charge buildup.
- High-Quality Thin Films: The process produces uniform and high-quality coatings, making it ideal for precision applications.
- Reduced Arcing: Alternating the electrical potential minimizes arcing, which can damage the thin film or halt the sputtering process.
-
RF Magnetron Sputtering:
- A variation of RF sputtering that uses magnets to trap electrons near the target material, increasing the ionization of the gas and enhancing the deposition rate.
- This method is particularly useful for achieving faster and more efficient thin-film deposition.
-
Applications of RF Sputtering:
- Semiconductor Industry: Used for depositing insulating layers and conductive films in microelectronics.
- Optics: Applied in the production of anti-reflective coatings and optical filters.
- Computer Manufacturing: Utilized for creating thin films in hard drives and other components.
-
Key Components of RF Sputtering Systems:
- RF Power Supply: Delivers energy at the required frequency (13.56 MHz).
- Matching Network: Ensures efficient power transfer between the power supply and the plasma.
- Vacuum Chamber: Maintains the controlled environment necessary for the sputtering process.
- Target Material: The material to be sputtered, which can be conductive or insulating.
- Substrate Holder: Holds the material to be coated and acts as the second electrode.
-
Challenges and Considerations:
- Complexity: RF sputtering systems are more complex and expensive than DC sputtering systems.
- Heat Generation: The process can generate significant heat, requiring effective cooling mechanisms.
- Target Material Compatibility: While RF sputtering can handle insulating materials, the choice of target material must still be carefully considered to achieve desired film properties.
By understanding these key points, equipment and consumable purchasers can make informed decisions about the suitability of RF sputtering for their specific applications, ensuring optimal performance and cost-effectiveness.
Summary Table:
Aspect | Details |
---|---|
Definition | Thin-film deposition using RF energy for insulating materials. |
Key Advantage | Handles non-conductive materials, prevents charge buildup. |
Process | Alternating electrical potential at 13.56 MHz in a vacuum environment. |
Applications | Semiconductors, optics, computer manufacturing. |
Key Components | RF power supply, matching network, vacuum chamber, target material. |
Challenges | Complexity, heat generation, target material compatibility. |
Discover how RF sputtering can enhance your manufacturing process—contact our experts today!