Sputter deposition is a critical process in semiconductor manufacturing, used to deposit thin films of materials onto substrates. This process involves bombarding a target material with high-energy ions, typically from a plasma of argon, which causes atoms from the target to be ejected and deposited onto a substrate. This method is particularly valued for its ability to produce highly pure and uniform coatings, essential for the high-performance requirements of semiconductor components. Sputter deposition is versatile, capable of depositing a wide range of materials, including metals and ceramics, and has evolved significantly since its discovery in the mid-19th century.
Key Points Explained:
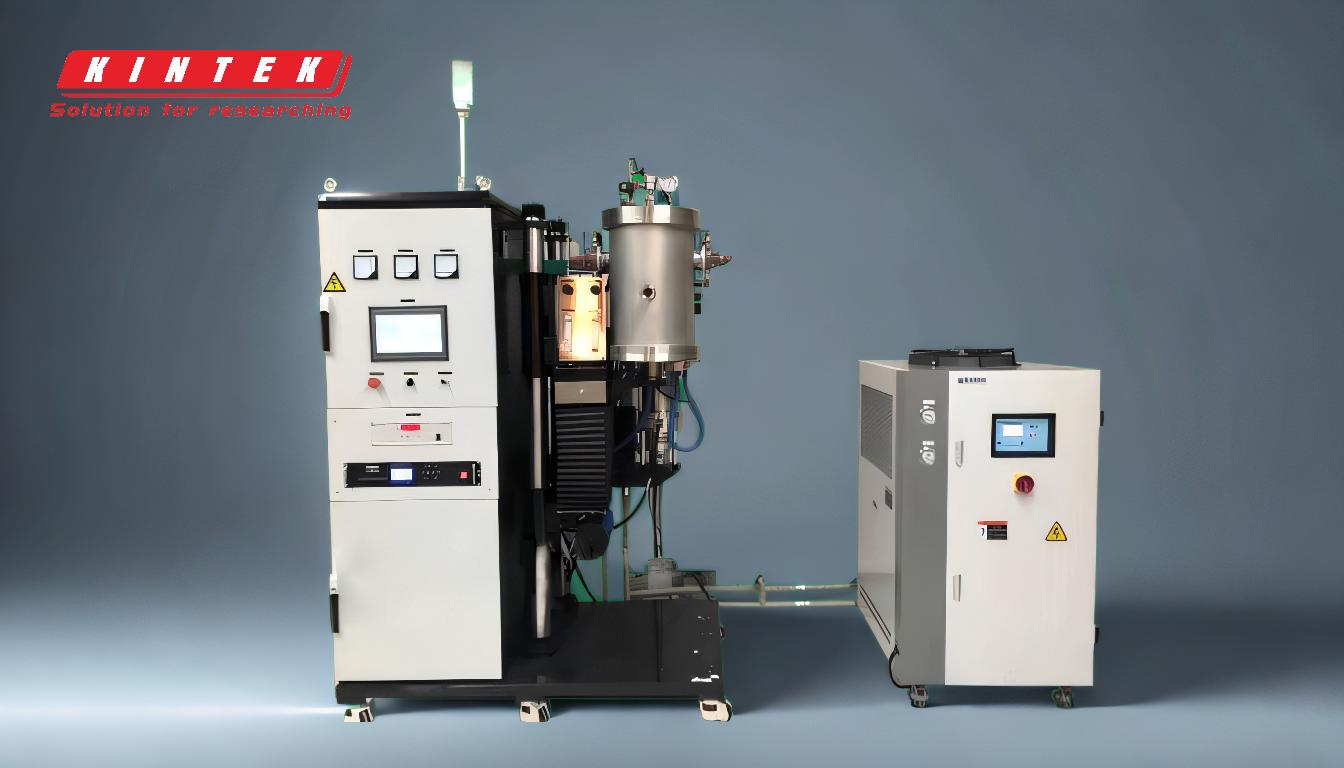
-
Mechanism of Sputter Deposition:
- Sputter deposition works by exposing a target material to a plasma of high-energy ions, usually argon. These ions collide with the target, causing atoms to be ejected from its surface.
- The ejected atoms form a vapor cloud that then condenses onto a substrate, forming a thin film. This process is highly controlled to ensure uniformity and purity of the deposited material.
-
Applications in Semiconductor Manufacturing:
- In semiconductor production, sputter deposition is used to apply thin films of materials like gold, which are essential for their excellent electrical and thermal conductivity.
- The process is crucial for creating the intricate layers of metal and dielectric materials needed in integrated circuits and other semiconductor devices.
-
Historical Development and Technological Advancements:
- Sputter deposition was first observed in the mid-19th century and found commercial applications by the 1930s.
- After a period of decline in the 1950s, the technique regained popularity in the late 1950s and early 1960s due to advancements in vacuum technology and the development of radio frequency (rf) sputtering, which allowed for the deposition of dielectric materials.
-
Importance of Purity in Sputtering Targets:
- The purity of the sputtering target is paramount, especially in semiconductor applications. Even trace impurities can significantly affect the performance of the semiconductor components.
- High-purity targets ensure that the deposited films have the necessary electrical and thermal properties required for high-performance semiconductor devices.
-
Use in Scanning Electron Microscopy (SEM):
- Sputter coating is also used in SEM to improve the imaging of samples. By depositing a thin conductive layer on non-conductive or beam-sensitive samples, it reduces charging effects and enhances the signal-to-noise ratio, leading to clearer and more detailed images.
Sputter deposition remains a cornerstone technique in the fabrication of modern semiconductor devices, offering precision and versatility that are unmatched by other deposition methods. Its continued evolution and adaptation to new materials and technologies underscore its importance in the advancement of semiconductor manufacturing.
Summary Table:
Key Aspect | Details |
---|---|
Mechanism | High-energy argon ions bombard a target, ejecting atoms to form a thin film. |
Applications | Used in semiconductor devices for electrical and thermal conductivity. |
Historical Development | Discovered in the 19th century; advanced with RF sputtering in the 1960s. |
Target Purity | High-purity targets ensure optimal electrical and thermal properties. |
SEM Applications | Enhances imaging by depositing conductive layers on non-conductive samples. |
Discover how sputter deposition can revolutionize your semiconductor processes—contact our experts today!