Sputtering in material science is a physical process used for depositing thin films of materials onto substrates. It involves bombarding a target material with high-energy ions, typically from an inert gas like argon, in a vacuum chamber. This bombardment causes atoms or molecules from the target to be ejected and subsequently deposited onto a substrate, forming a thin film. Sputtering is widely used in industries such as semiconductor manufacturing, optics, and packaging due to its precision and ability to produce high-quality, uniform coatings. The process is highly controllable, making it suitable for applications requiring ultra-high purity and precise thickness control.
Key Points Explained:
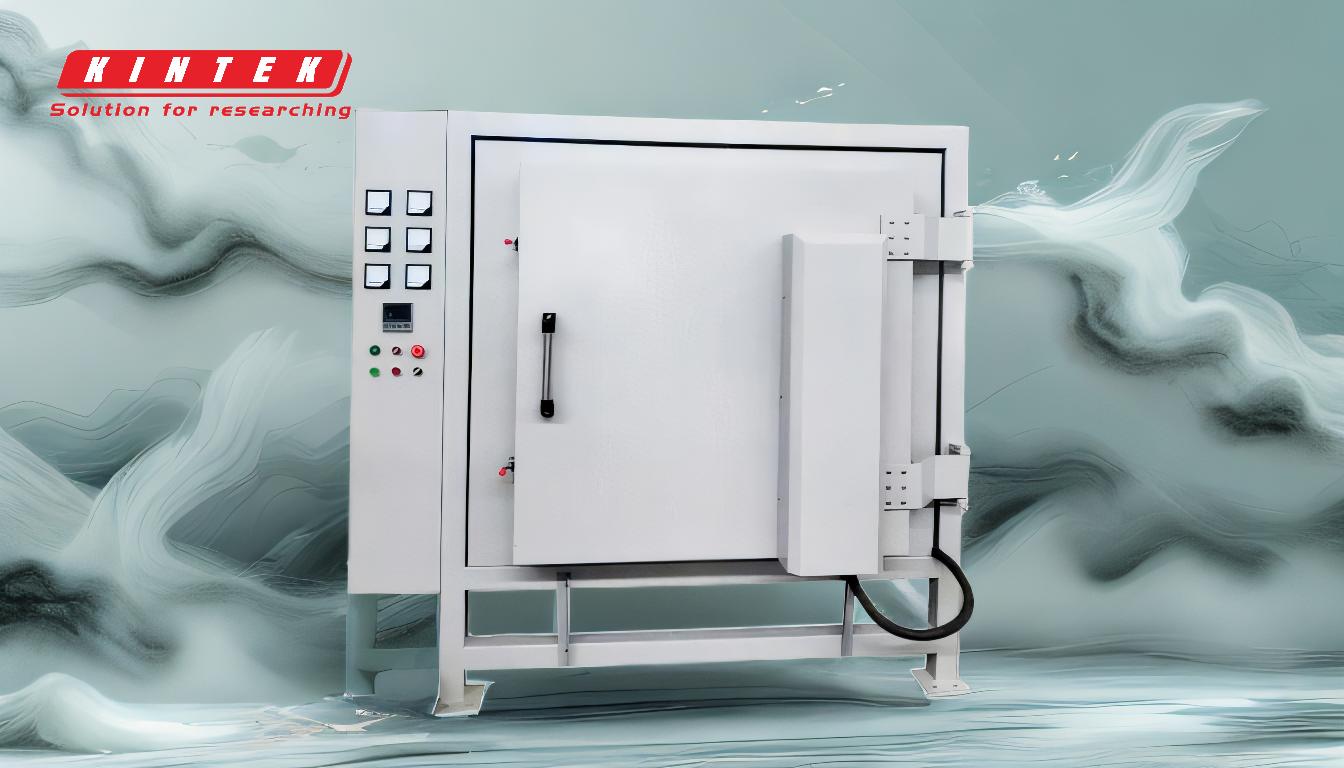
-
Definition of Sputtering:
- Sputtering is a physical vapor deposition (PVD) technique where atoms are ejected from a solid target material due to bombardment by energetic ions.
- The ejected atoms then travel through a vacuum and deposit onto a substrate, forming a thin film.
-
Mechanism of Sputtering:
- A target material and a substrate are placed in a vacuum chamber.
- A voltage is applied, making the target the cathode and the substrate the anode.
- A plasma is created by ionizing a sputtering gas (usually argon or xenon).
- The target material is bombarded by ions from the plasma, causing atoms to be ejected from the target surface.
- These ejected atoms travel through the vacuum and deposit onto the substrate, forming a thin film.
-
Key Components of the Sputtering Process:
- Vacuum Chamber: Essential for maintaining a controlled environment free from contaminants.
- Target Material: The source material that is bombarded to produce the thin film.
- Substrate: The surface onto which the thin film is deposited.
- Sputtering Gas: Typically an inert gas like argon, which is ionized to create the plasma.
- Power Supply: Provides the voltage necessary to create the plasma and accelerate ions toward the target.
-
Applications of Sputtering:
- Semiconductor Manufacturing: Used to deposit thin films of metals and dielectrics in the production of integrated circuits.
- Optics: Produces reflective coatings for mirrors and anti-reflective coatings for lenses.
- Packaging: Creates barrier layers in packaging materials, such as those used in potato chip bags.
- Decorative Coatings: Used to apply thin films for aesthetic purposes on various products.
-
Advantages of Sputtering:
- High Precision: Allows for the deposition of films with precise thickness and composition.
- Uniformity: Produces highly uniform coatings over large areas.
- Material Versatility: Can be used with a wide range of materials, including metals, alloys, and ceramics.
- High Purity: The vacuum environment minimizes contamination, resulting in high-purity films.
-
Historical Context:
- Sputtering has been studied since the early 1800s, making it a mature and well-understood process.
- Its initial applications were primarily in research, but it has since become a cornerstone of modern manufacturing processes.
-
Process Variations:
- Magnetron Sputtering: Uses magnetic fields to enhance the efficiency of the sputtering process by confining electrons near the target, increasing the ionization of the sputtering gas.
- Reactive Sputtering: Involves the use of reactive gases (e.g., oxygen or nitrogen) to form compound films (e.g., oxides or nitrides) during the deposition process.
- Ion Beam Sputtering: Uses a focused ion beam to sputter the target material, offering even greater control over the deposition process.
-
Challenges and Considerations:
- Cost: The equipment and vacuum requirements can be expensive.
- Complexity: The process requires careful control of parameters such as pressure, gas flow, and power.
- Material Limitations: Some materials may be difficult to sputter due to their physical properties.
In summary, sputtering is a versatile and precise method for depositing thin films, with applications spanning multiple industries. Its ability to produce high-quality, uniform coatings makes it an essential technique in modern material science and manufacturing.
Summary Table:
Key Aspect | Details |
---|---|
Definition | Physical vapor deposition (PVD) technique for ejecting atoms from a target. |
Mechanism | Bombardment of target material with ions in a vacuum chamber. |
Key Components | Vacuum chamber, target material, substrate, sputtering gas, power supply. |
Applications | Semiconductors, optics, packaging, decorative coatings. |
Advantages | High precision, uniformity, material versatility, high purity. |
Process Variations | Magnetron, reactive, and ion beam sputtering. |
Challenges | Cost, complexity, and material limitations. |
Discover how sputtering can elevate your manufacturing process—contact us today for expert guidance!