Sputtering ions are ions used in the sputtering process, a thin film deposition technique where high-energy ions bombard a target material, causing atoms or molecules to be ejected and deposited onto a substrate. This process occurs in a vacuum chamber, typically using inert gases like argon. The ions are generated by ionizing the sputtering gas, and they are accelerated toward the target material due to an applied voltage. The collision of these ions with the target causes the ejection of target particles, which then form a thin film on the substrate. Sputtering is widely used in industries for creating durable coatings, analyzing surface compositions, and developing advanced materials.
Key Points Explained:
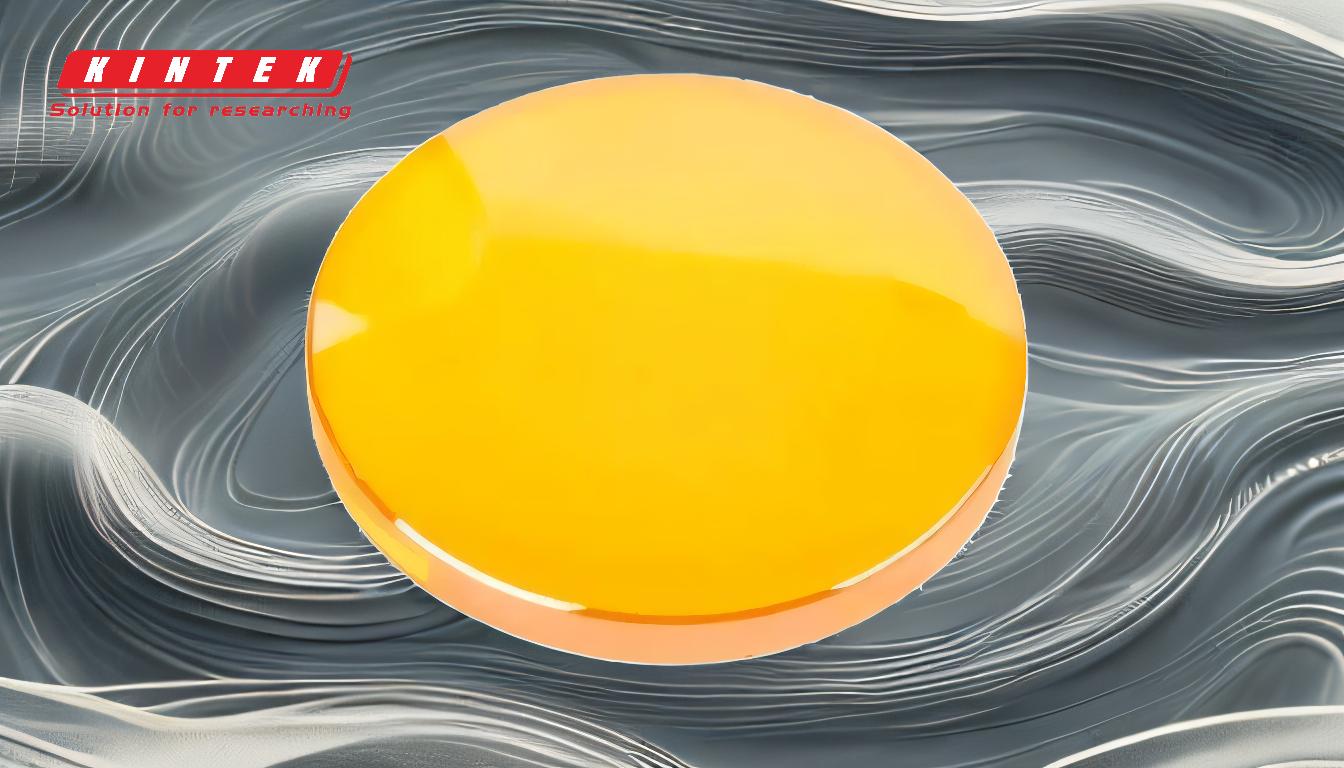
-
Definition of Sputtering Ions:
- Sputtering ions are charged particles (usually ions of inert gases like argon or xenon) that are accelerated toward a target material in a vacuum chamber. These ions are generated by ionizing a sputtering gas, and their energy is used to dislodge atoms or molecules from the target material.
-
Mechanism of Sputtering:
- The sputtering process involves:
- Placing the target material and substrate in a vacuum chamber.
- Applying a voltage to create a plasma by ionizing the sputtering gas.
- Accelerating the ions toward the target material, causing the target atoms to be ejected.
- Depositing the ejected material onto the substrate as a thin film.
- The sputtering process involves:
-
Role of Inert Gases:
- Inert gases like argon or xenon are commonly used as sputtering gases because they are chemically non-reactive. This ensures that the sputtering process does not introduce unwanted chemical reactions, maintaining the purity of the deposited film.
-
Energy Transfer and Ejection:
- When the sputtering ions collide with the target material, they transfer their kinetic energy to the target atoms. If the energy transferred is sufficient, the target atoms are ejected from the surface in the form of neutral particles. These particles then travel through the vacuum and deposit onto the substrate.
-
Applications of Sputtering Ions:
- Thin Film Deposition: Sputtering ions are used to create thin films for applications in electronics, optics, and coatings.
- Surface Cleaning: The process can be used to clean surfaces by removing contaminants.
- Surface Analysis: Sputtering is employed in techniques like Secondary Ion Mass Spectrometry (SIMS) to analyze the chemical composition of surfaces.
- Alloy Formation: Sputtering allows for the deposition of alloys in a single run, making it useful for creating complex material structures.
-
Vacuum Environment:
- Sputtering requires a vacuum environment to prevent contamination and ensure that the ejected particles travel unimpeded to the substrate. The vacuum also helps in maintaining the stability of the plasma and the efficiency of the ion bombardment.
-
Types of Sputtering:
- Magnetron Sputtering: Uses magnetic fields to confine electrons near the target, increasing the ionization of the sputtering gas and enhancing the sputtering rate.
- Ion Beam Sputtering (IBS): A more precise method where an ion beam is directed at the target, allowing for better control over the deposition process.
-
Advantages of Sputtering:
- High Purity: The vacuum environment and use of inert gases ensure high-purity films.
- Versatility: Can deposit a wide range of materials, including metals, alloys, and dielectrics.
- Uniformity: Produces uniform thin films with precise thickness control.
-
Challenges:
- Cost: The equipment and vacuum systems required for sputtering can be expensive.
- Complexity: The process requires careful control of parameters like pressure, voltage, and gas flow.
- Deposition Rate: Sputtering can have slower deposition rates compared to other thin film deposition techniques.
In summary, sputtering ions play a critical role in the sputtering process, enabling the creation of high-quality thin films and coatings used in various industries. The process relies on the controlled bombardment of a target material by high-energy ions, resulting in the ejection and deposition of target atoms onto a substrate. This technique is valued for its precision, versatility, and ability to produce uniform, high-purity films.
Summary Table:
Aspect | Details |
---|---|
Definition | Charged particles (e.g., argon or xenon ions) used to eject target atoms. |
Mechanism | Ion bombardment in a vacuum chamber deposits ejected atoms onto a substrate. |
Role of Inert Gases | Non-reactive gases like argon ensure high-purity film deposition. |
Applications | Thin films, surface cleaning, alloy formation, and surface analysis. |
Advantages | High purity, versatility, and uniform film thickness. |
Challenges | High cost, process complexity, and slower deposition rates. |
Discover how sputtering ions can revolutionize your material processes—contact our experts today!