Hot isostatic pressing (HIP) is a versatile manufacturing process that applies high temperature and uniform gas pressure to eliminate porosity, increase density, and improve the mechanical properties of materials. It is widely used across industries such as aerospace, automotive, medical, oil and gas, and power generation. HIP enhances material integrity by removing internal defects, making it essential for applications requiring high fatigue resistance, durability, and performance in extreme environments. Key applications include densification of castings, consolidation of powder metallurgy, additive manufacturing, diffusion bonding, and the production of high-performance components for industries like aerospace, defense, and medical devices.
Key Points Explained:
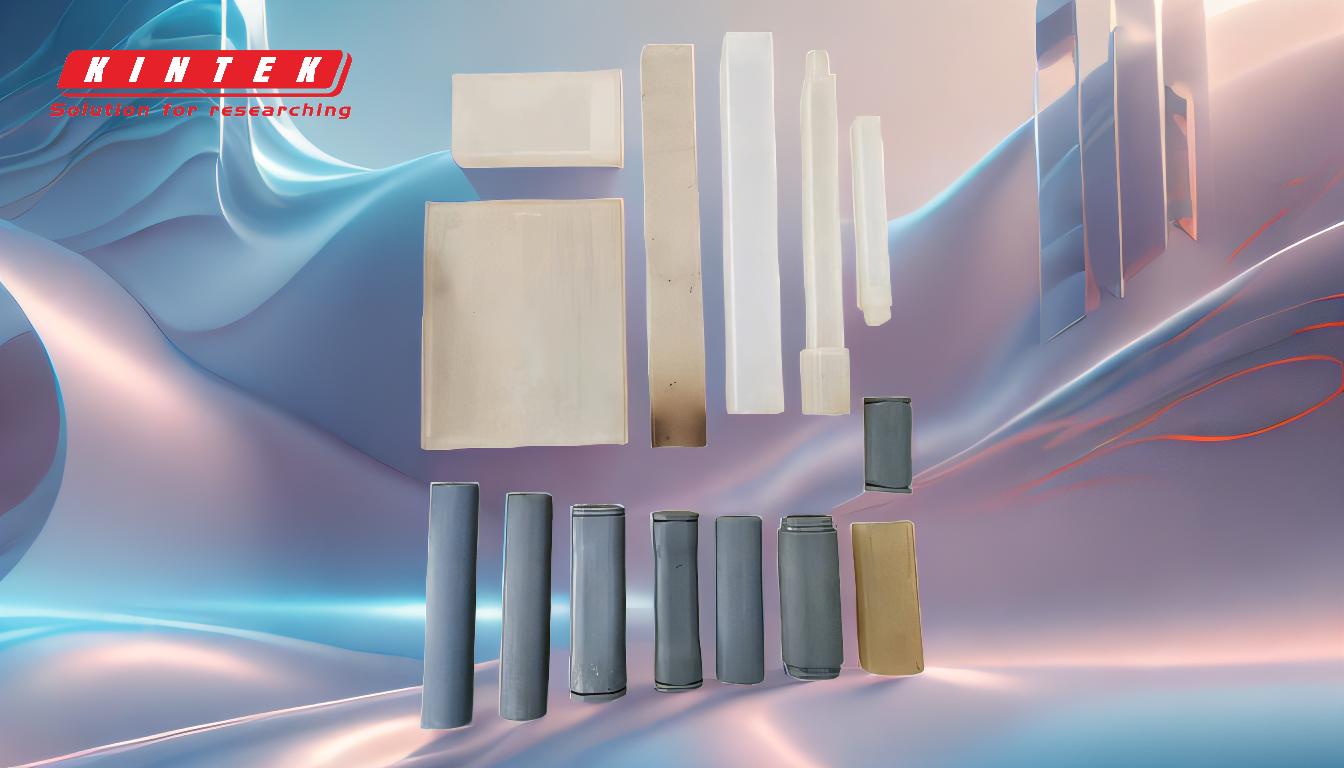
-
Elimination of Porosity and Defects:
- HIP uses elevated temperature and isostatic gas pressure to remove internal voids, cracks, and defects in materials.
- This process results in denser, more durable parts, which are critical for applications requiring high fatigue resistance and structural integrity.
- Example: Aerospace castings and industrial gas turbine components benefit from HIP to ensure reliability under extreme stress.
-
Densification of Castings:
- HIP is extensively used to densify castings in industries like aerospace, power generation, and heavy equipment.
- By eliminating porosity, HIP improves the mechanical properties of cast parts, making them suitable for high-performance applications.
- Example: Turbine blades and engine components in aerospace and power generation industries.
-
Powder Metallurgy and Metal Injection Molding (MIM):
- HIP consolidates metal powders into solid objects, enhancing their density and mechanical properties.
- This is particularly useful in producing complex, near-net-shape components with minimal material waste.
- Example: Automotive and medical components, such as gears and orthopedic implants.
-
Additive Manufacturing and 3D Printing:
- HIP is increasingly used in additive manufacturing to improve the performance of 3D-printed metal parts.
- It ensures that parts produced through additive manufacturing meet the stringent material requirements of industries like aerospace and medical.
- Example: Rocket engine components and racing car parts.
-
Diffusion Bonding:
- HIP enables the bonding of dissimilar metals, creating cost-effective and high-performance components.
- This technique is valuable in industries requiring complex assemblies with superior material properties.
- Example: Aerospace and defense applications, where lightweight and durable materials are essential.
-
High-Performance Applications in Extreme Environments:
- HIP is used in industries where materials must withstand extreme conditions, such as power units and submarine oil pipelines.
- It ensures that materials meet the high performance and reliability standards required in these environments.
- Example: Components for nuclear reactors and offshore oil drilling equipment.
-
Medical and Biomedical Applications:
- HIP is critical in the production of biomedical devices and orthopedic implants, where material integrity and biocompatibility are paramount.
- It ensures that medical devices are free from defects and have the necessary mechanical properties for long-term use.
- Example: Hip and knee implants, dental prosthetics.
-
Versatility Across Materials:
- HIP is not limited to metals; it is also used for ceramics, polymers, and composite materials.
- This versatility makes it a valuable tool in a wide range of manufacturing processes.
- Example: High-end graphite production and ceramic components for industrial machinery.
-
Economic and Environmental Benefits:
- By improving material properties and reducing defects, HIP extends the lifespan of components, reducing the need for replacements and repairs.
- It also minimizes material waste, contributing to more sustainable manufacturing practices.
- Example: Cost savings in aerospace and automotive industries through the use of durable, high-performance components.
In summary, hot isostatic pressing is a critical technology for enhancing material properties and ensuring the reliability of components in high-performance industries. Its applications span from aerospace and automotive to medical and oil and gas, making it an indispensable tool in modern manufacturing.
Summary Table:
Key Benefit | Application |
---|---|
Elimination of Porosity & Defects | Aerospace castings, turbine blades, industrial gas turbine components |
Densification of Castings | Turbine blades, engine components in aerospace and power generation |
Powder Metallurgy & MIM | Automotive gears, orthopedic implants, dental prosthetics |
Additive Manufacturing | Rocket engine components, racing car parts |
Diffusion Bonding | Aerospace and defense lightweight components |
Extreme Environment Applications | Nuclear reactor components, offshore oil drilling equipment |
Medical & Biomedical | Hip and knee implants, dental prosthetics |
Versatility Across Materials | Ceramics, polymers, composites, high-end graphite production |
Economic & Environmental Benefits | Cost savings, reduced material waste, sustainable manufacturing practices |
Ready to enhance your materials with hot isostatic pressing? Contact our experts today to learn more!