Stainless steel reactors are widely used in various industries due to their durability, strength, and resistance to corrosion. The composition of a stainless steel reactor primarily involves stainless steel alloys, which are chosen based on their mechanical and chemical properties. These alloys typically contain iron, chromium, nickel, and other elements like molybdenum, manganese, and carbon. The specific composition depends on the intended application, particularly the need for resistance to corrosion, high pressure, and temperature. Stainless steel reactors are preferred for high-pressure applications, often up to 200 bar, and are suitable for processes requiring robust and long-lasting equipment.
Key Points Explained:
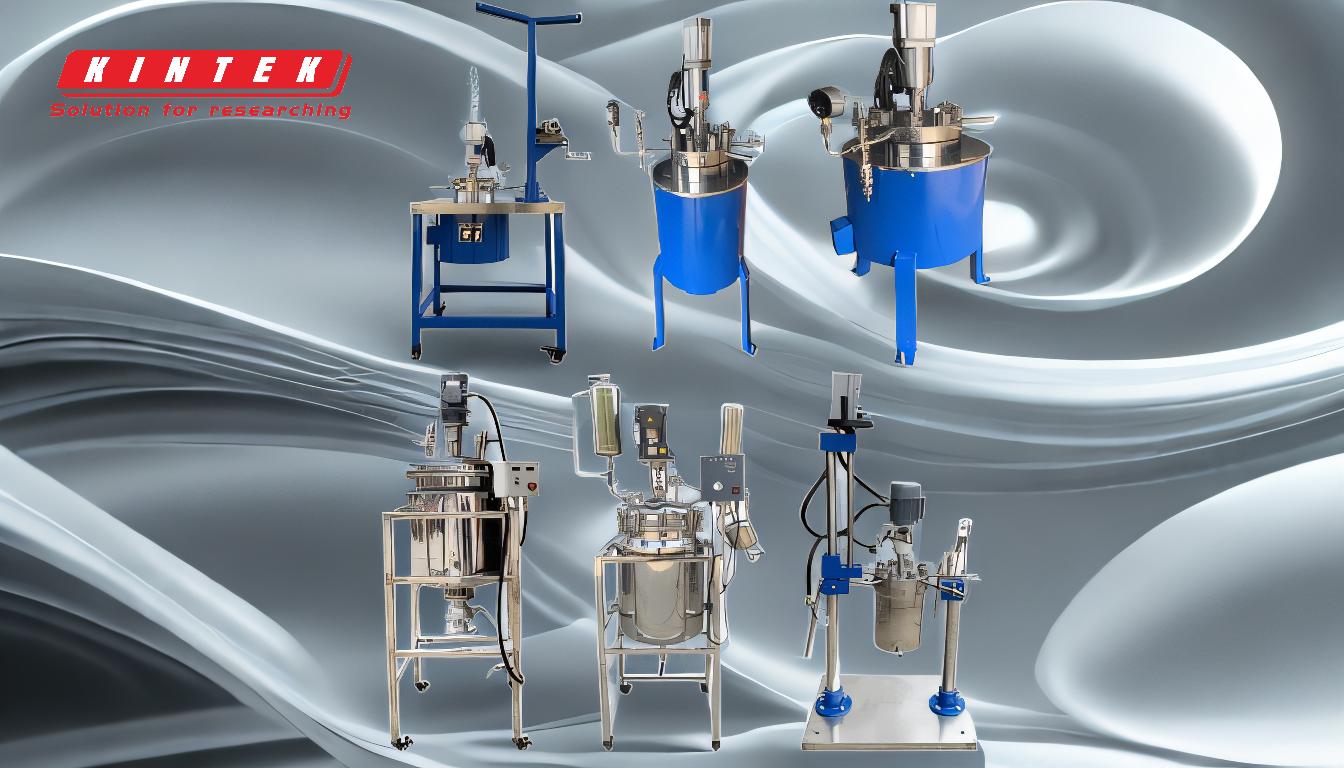
-
Primary Composition of Stainless Steel Alloys:
- Stainless steel reactors are primarily made of stainless steel alloys, which are iron-based metals containing chromium and nickel as the main alloying elements.
- Chromium (typically 10.5% or more) provides corrosion resistance by forming a passive layer of chromium oxide on the surface.
- Nickel enhances ductility, toughness, and resistance to oxidation and corrosion, especially in acidic environments.
- Additional elements like molybdenum, manganese, and carbon may be included to improve specific properties such as strength, weldability, and resistance to pitting corrosion.
-
Types of Stainless Steel Used:
- Austenitic Stainless Steel (e.g., 304, 316): The most common type used in reactors due to its excellent corrosion resistance, formability, and weldability. Grade 316, which contains molybdenum, is particularly resistant to chlorides and acidic environments.
- Duplex Stainless Steel: Combines austenitic and ferritic structures, offering higher strength and better resistance to stress corrosion cracking.
- Ferritic Stainless Steel: Less commonly used in reactors but may be chosen for specific applications requiring resistance to certain types of corrosion.
-
Properties of Stainless Steel Reactors:
- High Strength and Durability: Stainless steel reactors can withstand high pressures (up to 200 bar) and mechanical stresses, making them suitable for demanding industrial processes.
- Corrosion Resistance: The chromium content ensures resistance to rust and corrosion, even in harsh chemical environments.
- Thermal Stability: Stainless steel maintains its structural integrity at high temperatures, making it suitable for processes involving heat.
- Hygienic Properties: Stainless steel is easy to clean and sterilize, making it ideal for pharmaceutical and food industries.
-
Applications of Stainless Steel Reactors:
- Stainless steel reactors are used in industries such as chemical processing, pharmaceuticals, food and beverage, and petrochemicals.
- They are ideal for processes involving corrosive chemicals, high pressures, and elevated temperatures.
- The ability to withstand aggressive environments makes them suitable for batch and continuous processes.
-
Comparison with Other Materials:
- Glass Reactors: Preferred for low-pressure applications (around 5 bar) where visual observation of the reaction is necessary. However, glass is less durable and cannot handle high pressures or mechanical stresses.
- Exotic Alloys (e.g., Hastelloy, Inconel): Used for extremely high-pressure applications (thousands of bars) due to their superior strength and resistance to oxidation and corrosion. However, these materials are more expensive than stainless steel.
-
Considerations for Purchasing:
- When selecting a stainless steel reactor, consider the specific chemical environment, pressure requirements, and temperature range.
- Ensure the reactor is constructed from the appropriate grade of stainless steel (e.g., 316 for acidic or chloride-rich environments).
- Evaluate the reactor's design, including seals, fittings, and accessories, to ensure compatibility with the intended process.
In summary, the composition of a stainless steel reactor is primarily based on stainless steel alloys, with specific grades chosen to meet the demands of the application. These reactors offer a balance of strength, durability, and corrosion resistance, making them a versatile choice for a wide range of industrial processes.
Summary Table:
Aspect | Details |
---|---|
Primary Composition | Iron, chromium, nickel, molybdenum, manganese, carbon |
Key Properties | High strength, corrosion resistance, thermal stability, hygienic properties |
Common Grades | 304, 316 (austenitic), duplex, ferritic |
Applications | Chemical, pharmaceutical, food & beverage, petrochemical industries |
Pressure Capacity | Up to 200 bar |
Comparison | More durable than glass, cost-effective vs. exotic alloys |
Discover the perfect stainless steel reactor for your needs—contact our experts today!