A reactor and a reaction vessel are terms often used interchangeably, but they have nuanced differences in their design, functionality, and application. A reaction vessel is a general term for any container designed to hold and facilitate chemical reactions, focusing on providing an enclosed space with controlled conditions like temperature, pressure, and mixing. A reactor, on the other hand, is a more specialized type of reaction vessel that often includes advanced features for precise control and optimization of chemical processes. The distinction lies in the complexity, purpose, and engineering design, with reactors being more sophisticated and tailored for specific industrial applications.
Key Points Explained:
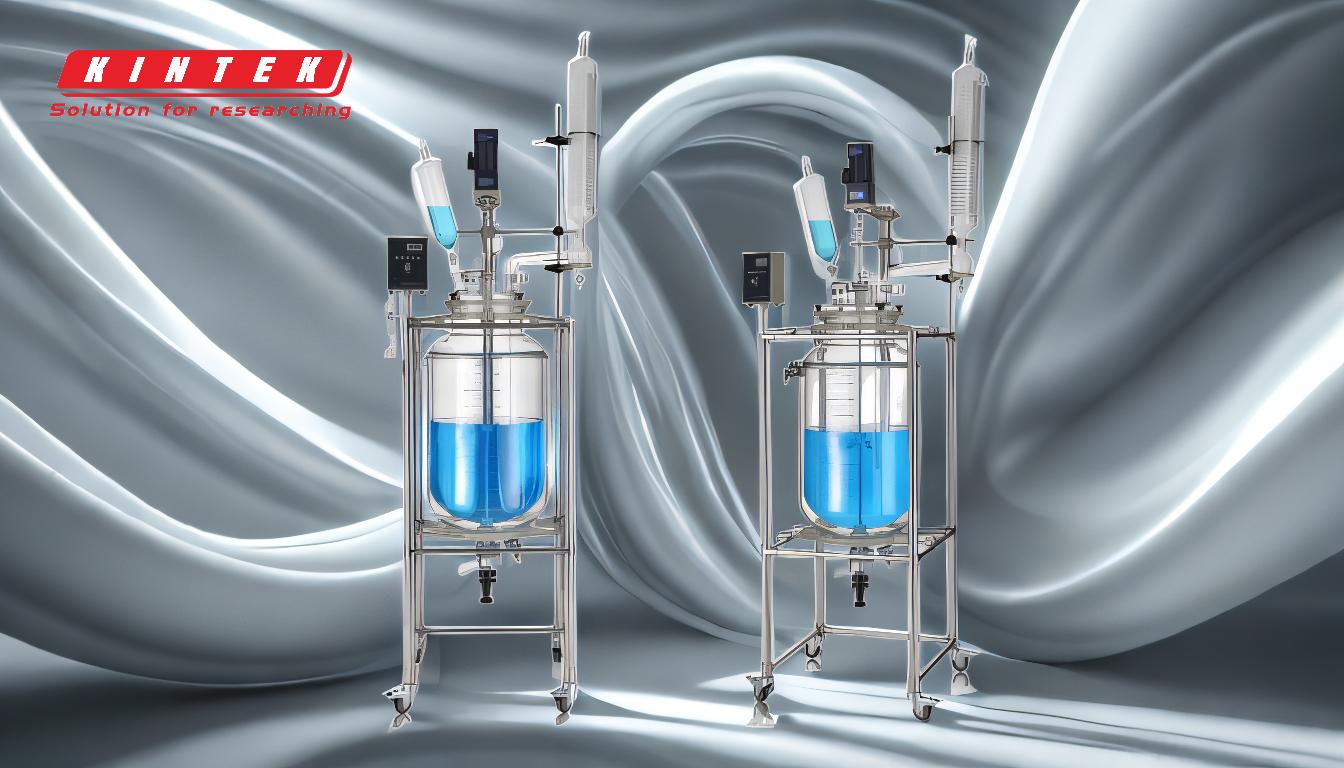
-
Definition and Scope:
- Reaction Vessel: A reaction vessel is a broad term referring to any container designed to facilitate chemical reactions. It provides an enclosed space where reactions can occur under controlled conditions such as temperature, pressure, and mixing. Reaction vessels are commonly used in laboratories and small-scale industrial processes.
- Reactor: A reactor is a specialized type of reaction vessel that is often more complex and designed for specific industrial applications. Reactors are engineered to optimize chemical processes, often incorporating advanced features like precise temperature control, pressure regulation, and automated mixing systems.
-
Design and Complexity:
- Reaction Vessel: The design of a reaction vessel is relatively simple, focusing on basic functionalities like containment, mixing, and temperature control. It is typically used for straightforward chemical reactions where high precision is not critical.
- Reactor: Reactors are designed with greater complexity to handle more demanding chemical processes. They may include features like catalyst beds, heat exchangers, and advanced control systems to optimize reaction conditions and improve efficiency.
-
Applications:
- Reaction Vessel: Reaction vessels are commonly used in laboratories, pilot plants, and small-scale industrial processes. They are suitable for a wide range of chemical reactions, including simple mixing, heating, and cooling processes.
- Reactor: Reactors are typically used in large-scale industrial processes where precise control over reaction conditions is essential. They are often employed in industries like petrochemicals, pharmaceuticals, and food processing, where the optimization of chemical reactions is critical for product quality and yield.
-
Control and Automation:
- Reaction Vessel: Control systems in reaction vessels are generally basic, focusing on manual or semi-automated control of parameters like temperature and pressure. They may not have advanced automation features.
- Reactor: Reactors often feature advanced control and automation systems to precisely regulate reaction conditions. This can include programmable logic controllers (PLCs), sensors, and feedback loops to maintain optimal conditions throughout the reaction process.
-
Material and Construction:
- Reaction Vessel: Reaction vessels are typically made from materials like stainless steel, glass, or other corrosion-resistant alloys, depending on the chemical process. The construction is straightforward, focusing on durability and ease of maintenance.
- Reactor: Reactors are constructed from high-grade materials that can withstand harsh chemical environments and extreme conditions. The construction is more robust, often incorporating specialized coatings or linings to enhance durability and performance.
-
Scale and Capacity:
- Reaction Vessel: Reaction vessels are generally smaller in scale, suitable for laboratory or pilot-scale operations. They are designed to handle smaller volumes of reactants.
- Reactor: Reactors are designed for large-scale industrial operations, capable of handling significant volumes of reactants. They are built to accommodate the high throughput required in commercial production.
In summary, while both reactors and reaction vessels serve the purpose of facilitating chemical reactions, the key differences lie in their design complexity, application scope, and the level of control and automation they offer. Reactors are more specialized and sophisticated, tailored for industrial-scale processes, whereas reaction vessels are more general-purpose and suited for smaller-scale operations.
Summary Table:
Aspect | Reaction Vessel | Reactor |
---|---|---|
Definition | General-purpose container for chemical reactions. | Specialized vessel with advanced features for optimized chemical processes. |
Design Complexity | Simple design for basic functionalities like mixing and temperature control. | Complex design with features like catalyst beds, heat exchangers, and advanced control systems. |
Applications | Used in labs and small-scale industrial processes. | Used in large-scale industrial processes like petrochemicals and pharmaceuticals. |
Control & Automation | Basic control systems, often manual or semi-automated. | Advanced automation with PLCs, sensors, and feedback loops for precise regulation. |
Material & Construction | Made from stainless steel, glass, or corrosion-resistant alloys. | Constructed with high-grade materials to withstand harsh conditions and extreme environments. |
Scale & Capacity | Smaller scale, suitable for labs and pilot plants. | Large-scale, designed for high-throughput industrial production. |
Need help choosing the right equipment for your chemical processes? Contact our experts today for personalized advice!