The residence time in a batch reactor significantly impacts the reaction by determining how long reactants remain in the reactor, which directly influences the extent of the reaction, product yield, and selectivity. Longer residence times generally allow for more complete reactions, higher conversion rates, and improved product quality, but they also increase energy consumption and operational costs. Conversely, shorter residence times may lead to incomplete reactions and lower yields but reduce energy usage and costs. Optimizing residence time is crucial for balancing reaction efficiency, product quality, and economic considerations.
Key Points Explained:
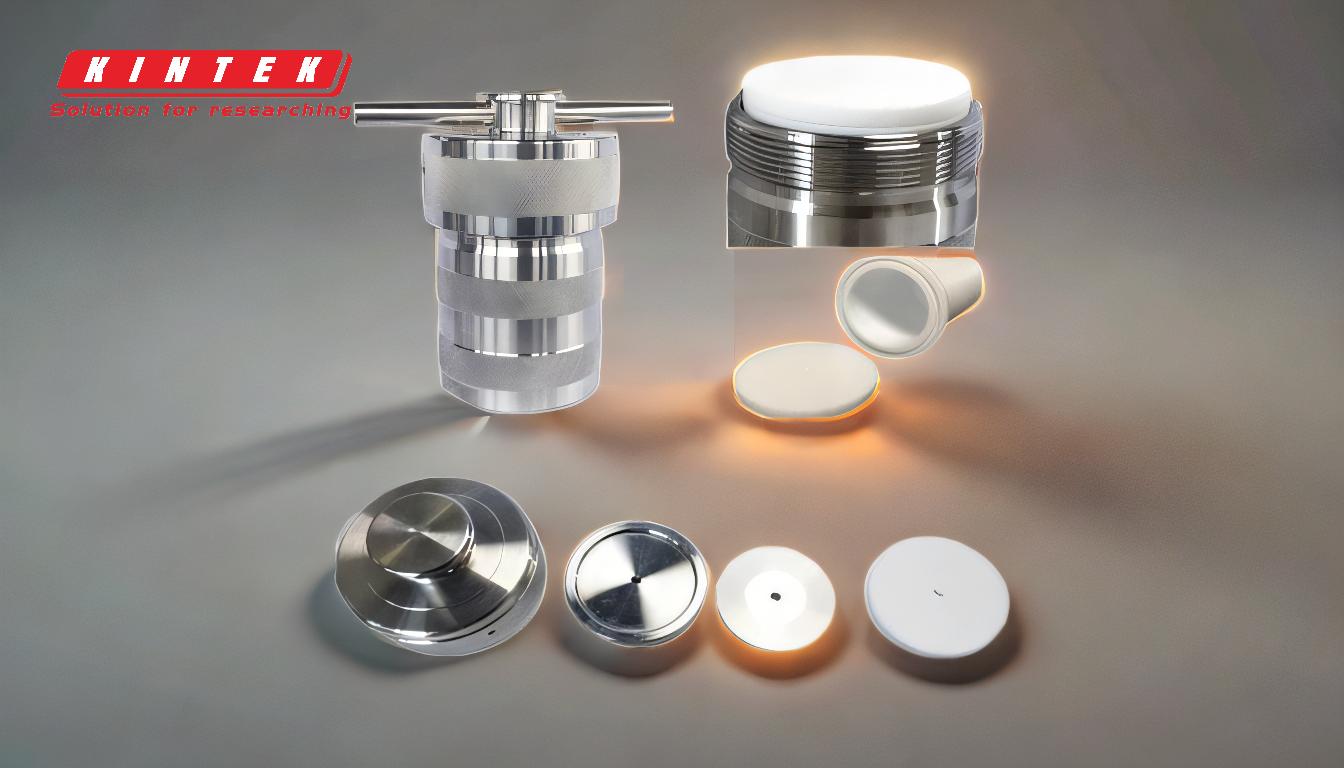
-
Definition of Residence Time in a Batch Reactor:
- Residence time refers to the duration that reactants spend in the reactor before being removed. In a batch reactor, this is equivalent to the total reaction time, as the reactants are added at the start and removed after the reaction is complete.
- Unlike continuous reactors, where residence time is determined by flow rate, in batch reactors, it is controlled by the reaction kinetics and operational parameters.
-
Impact on Reaction Extent and Conversion:
- Longer residence times allow more time for reactants to interact, leading to higher conversion rates and more complete reactions.
- For reactions with slow kinetics, extended residence times are necessary to achieve desired conversion levels.
- Example: In polymerization reactions, longer residence times ensure higher molecular weights and better polymer properties.
-
Effect on Product Yield and Selectivity:
- Residence time influences the selectivity of the reaction, especially in systems with multiple competing reactions.
- Optimal residence times can maximize the yield of the desired product while minimizing by-products.
- Example: In pharmaceutical synthesis, precise control of residence time is critical to ensure high-purity active pharmaceutical ingredients (APIs).
-
Energy Consumption and Operational Costs:
- Longer residence times require more energy to maintain reaction conditions (e.g., temperature, pressure), increasing operational costs.
- Shorter residence times reduce energy usage but may compromise reaction efficiency and product quality.
- Example: In exothermic reactions, prolonged residence times may necessitate additional cooling, raising energy expenses.
-
Reaction Kinetics and Residence Time Optimization:
- The relationship between residence time and reaction kinetics is crucial for optimizing reactor performance.
- Understanding the rate laws and activation energy of the reaction helps determine the ideal residence time.
- Example: For first-order reactions, doubling the residence time typically doubles the conversion, but this relationship may not hold for higher-order reactions.
-
Trade-offs in Residence Time Selection:
- Balancing reaction efficiency, product quality, and economic considerations is essential.
- Too short a residence time may result in incomplete reactions, while too long a residence time may lead to over-reaction or degradation of products.
- Example: In food processing, overcooking due to excessive residence time can degrade nutritional value and flavor.
-
Practical Considerations for Batch Reactors:
- Batch reactors are inherently flexible, allowing for adjustments in residence time based on experimental or operational feedback.
- Monitoring and control systems are critical for maintaining consistent residence times and ensuring reproducible results.
- Example: In chemical manufacturing, real-time monitoring of reaction progress helps optimize residence time for each batch.
-
Comparison with Continuous Reactors:
- In continuous reactors, residence time is influenced by flow rates and reactor volume, while in batch reactors, it is fixed by the reaction duration.
- Batch reactors are better suited for reactions requiring precise control over residence time, especially for small-scale or specialized processes.
- Example: Continuous reactors are preferred for large-scale production, whereas batch reactors are ideal for R&D and pilot-scale studies.
By carefully analyzing these factors, engineers and chemists can determine the optimal residence time for a batch reactor, ensuring efficient, cost-effective, and high-quality production.
Summary Table:
Aspect | Impact of Longer Residence Time | Impact of Shorter Residence Time |
---|---|---|
Reaction Extent | Higher conversion rates, more complete reactions | Incomplete reactions, lower conversion rates |
Product Yield | Improved yield and selectivity | Reduced yield, potential by-product formation |
Energy Consumption | Increased energy use and operational costs | Lower energy use and reduced costs |
Product Quality | Enhanced quality and desired properties | Potential degradation or over-reaction |
Economic Considerations | Higher costs due to energy and time | Lower costs but may compromise efficiency |
Need help optimizing your batch reactor's residence time? Contact our experts today for tailored solutions!