Hydrogen annealing is a specialized heat treatment process conducted in a hydrogen-rich atmosphere at elevated temperatures, typically between 200°C and 300°C. This process is primarily used to remove hydrogen embrittlement, relieve internal stresses, and clean oxidized surfaces. It is commonly applied after fabrication processes like welding, coating, or galvanizing. The hydrogen atmosphere prevents oxidation and promotes surface cleaning, but precautions are necessary to avoid decarburization of steel. While 100% hydrogen is effective, nitrogen-hydrogen blends offer a cost-effective alternative. The process involves maintaining the material in a hydrogen annealing oven for several hours to ensure thorough treatment.
Key Points Explained:
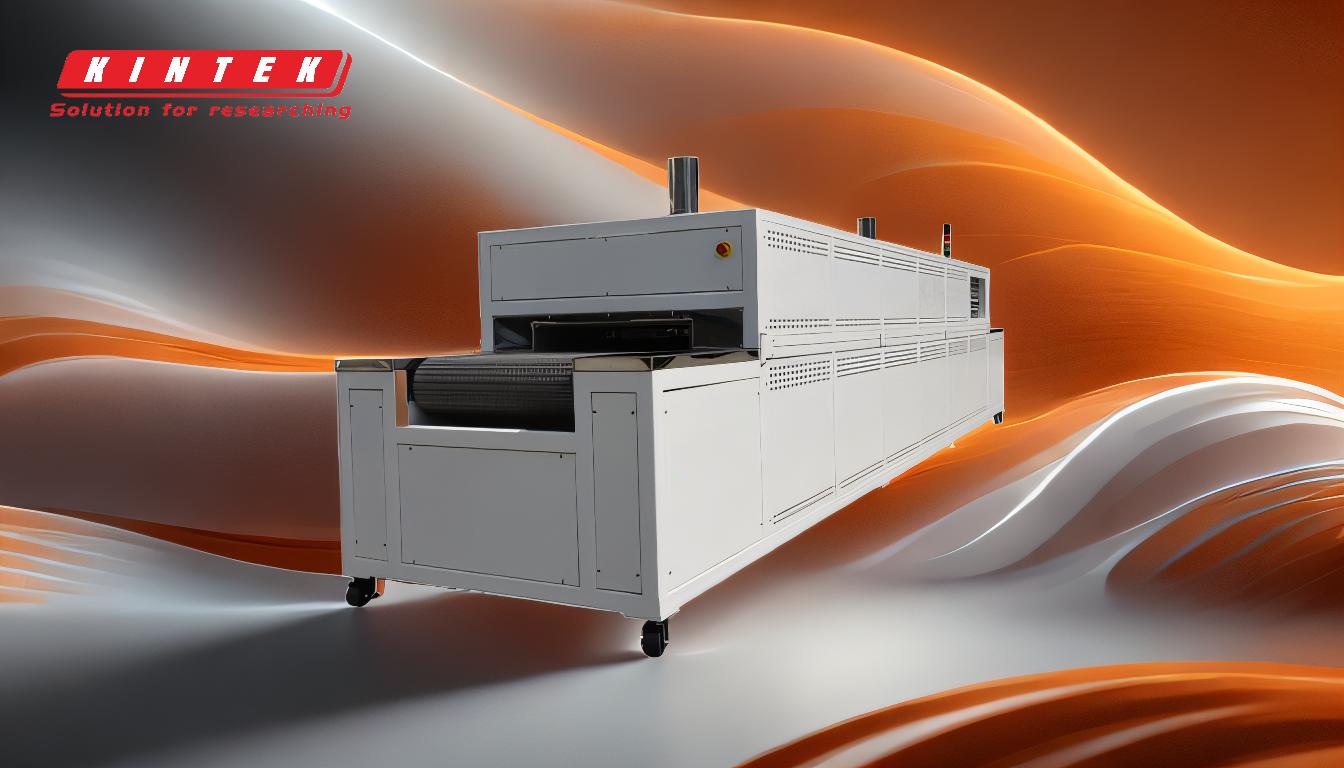
-
Temperature Range:
- Hydrogen annealing is performed at temperatures between 200°C and 300°C. This range is optimal for removing hydrogen atoms that cause embrittlement and for relieving internal stresses.
-
Hydrogen Atmosphere:
- The process is carried out in a 100% hydrogen atmosphere. Hydrogen is a highly reducing gas, which helps in:
- Preventing oxidation.
- Reducing surface oxides, leading to a cleaner and brighter surface, often referred to as 'bright annealing.'
- The process is carried out in a 100% hydrogen atmosphere. Hydrogen is a highly reducing gas, which helps in:
-
Duration:
- The material is kept in the hydrogen annealing oven for several hours. This extended duration ensures the complete removal of hydrogen atoms and the effective relief of internal stresses.
-
Applications:
- Hydrogen annealing is predominantly used immediately after:
- Welding: To relieve stresses and remove hydrogen introduced during the welding process.
- Coating processes: To ensure the integrity of the coating.
- Galvanizing: To prevent hydrogen embrittlement in galvanized parts.
- Hydrogen annealing is predominantly used immediately after:
-
Benefits:
- Removal of Hydrogen Embrittlement: The process effectively removes hydrogen atoms that can cause embrittlement, enhancing the material's durability.
- Stress Relief: It relieves internal stresses induced during fabrication processes like casting, welding, and coating.
- Surface Cleaning: The reducing nature of hydrogen cleans oxidized surfaces, improving the material's appearance and performance.
-
Precautions:
- Decarburization: Hydrogen can decarburize steel parts, leading to a loss of carbon content and weakening the material. Precautions must be taken to mitigate this risk.
- Cost: A 100% hydrogen atmosphere is the most expensive option. To reduce costs, nitrogen-hydrogen blends can be used as an alternative, offering a balance between effectiveness and expense.
-
Equipment:
- Hydrogen Annealing Oven: Specialized ovens designed to maintain a controlled hydrogen atmosphere at the required temperatures are used. These ovens must be capable of handling the high temperatures and ensuring a consistent hydrogen environment.
-
Process Variations:
- Bright Annealing: This is a specific type of hydrogen annealing where the primary goal is to achieve a bright, clean surface by reducing surface oxides.
- Nitrogen-Hydrogen Blends: For cost-sensitive applications, nitrogen-hydrogen blends can be used instead of pure hydrogen. These blends still provide the benefits of hydrogen annealing but at a lower cost.
In summary, hydrogen annealing is a critical heat treatment process that enhances the mechanical properties and surface quality of materials. By understanding the temperature requirements, the role of the hydrogen atmosphere, and the necessary precautions, manufacturers can effectively utilize this process to improve the performance and longevity of their products.
Summary Table:
Aspect | Details |
---|---|
Temperature Range | 200°C to 300°C |
Hydrogen Atmosphere | 100% hydrogen or nitrogen-hydrogen blends |
Duration | Several hours |
Applications | Post-welding, coating, galvanizing |
Benefits | Removes embrittlement, relieves stress, cleans surfaces |
Precautions | Avoid decarburization; consider cost-effective nitrogen-hydrogen blends |
Equipment | Specialized hydrogen annealing ovens |
Process Variations | Bright annealing, nitrogen-hydrogen blends |
Ready to improve your material performance? Contact us today to learn more about hydrogen annealing solutions!