The sputtering process, while widely used for thin-film deposition, has several limitations that can affect its efficiency, cost, and the quality of the deposited films. These limitations include potential film contamination from impurities, high capital and operational costs, low deposition rates for certain materials, difficulties in controlling film thickness, and challenges in integrating with other processes like lift-off. Additionally, the process may require complex equipment and cooling systems, which can further increase energy costs and reduce production rates. Understanding these limitations is crucial for selecting the appropriate deposition method for specific applications.
Key Points Explained:
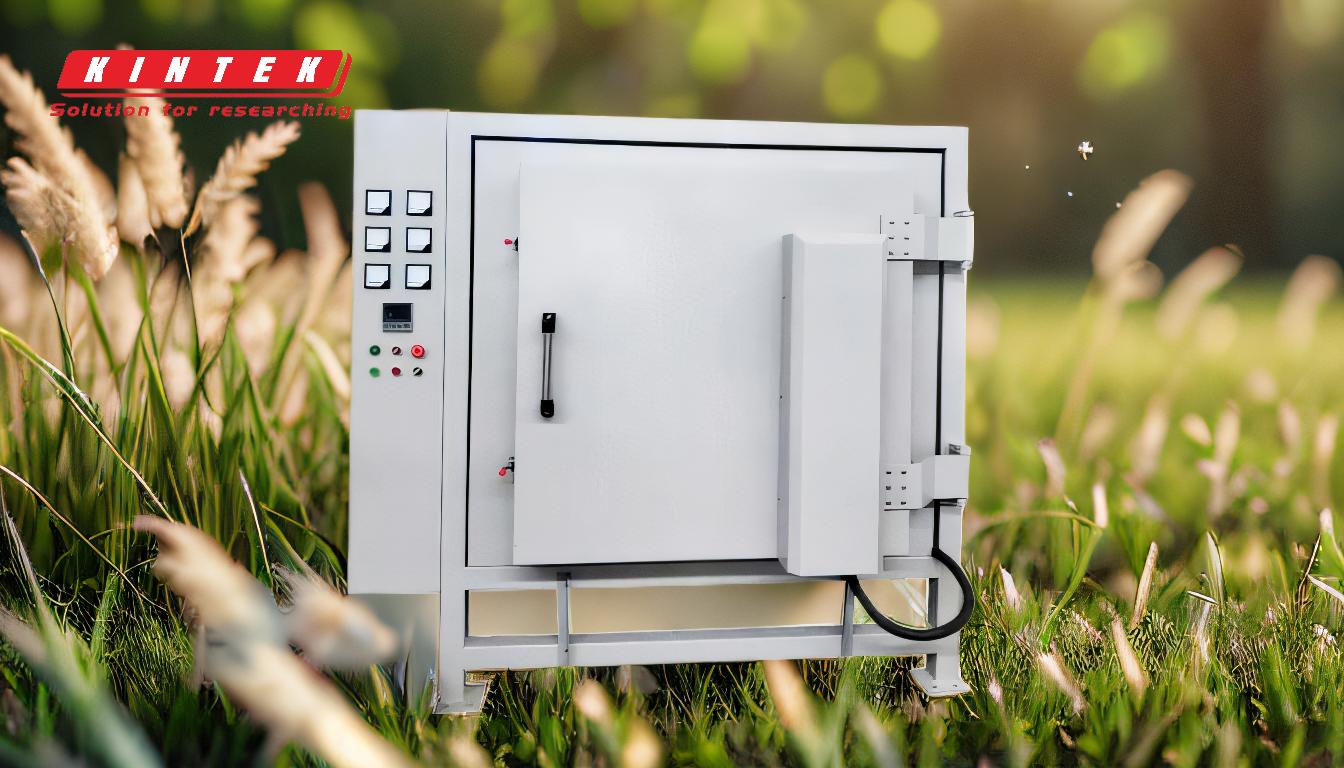
-
Film Contamination:
- Cause: Impurities from the source materials can diffuse into the film during the sputtering process, leading to contamination.
- Impact: This contamination can degrade the quality of the deposited film, affecting its electrical, optical, or mechanical properties.
- Example: Inert sputtering gases can become embedded in the growing film as impurities, further exacerbating contamination issues.
-
High Capital and Operational Costs:
- Equipment Complexity: Sputtering requires sophisticated equipment, including high-pressure devices and cooling systems, which are expensive to purchase and maintain.
- Energy Costs: The need for cooling systems not only increases energy consumption but also reduces the overall production rate, making the process less cost-effective.
-
Low Deposition Rates:
- Material Dependency: Certain materials, such as SiO2, have relatively low deposition rates in sputtering, which can slow down production.
- Production Impact: Low deposition rates can be a significant limitation in high-volume manufacturing environments where throughput is critical.
-
Difficulty in Controlling Film Thickness:
- Precision Issues: Sputtering processes often struggle with the precise control of film thickness, which is crucial for applications requiring uniform thin films.
- Layer-by-Layer Growth: Active control for layer-by-layer growth is more challenging compared to other deposition methods, such as pulsed laser deposition.
-
Challenges with Material Selection:
- Melting Temperature Limitations: The selection of coating materials is limited by their melting temperatures, as materials with very high melting points may not be suitable for sputtering.
- Degradation of Organic Solids: Some materials, particularly organic solids, are prone to degradation under ionic bombardment, limiting their use in sputtering processes.
-
Integration with Lift-Off Processes:
- Shadowing Issues: The diffuse transport characteristic of sputtering makes full shadowing impossible, complicating the integration with lift-off processes used for structuring films.
- Contamination Risks: This can lead to contamination problems, particularly when trying to create precise patterns or structures on the substrate.
-
Substrate Temperature Rise:
- Thermal Effects: The sputtering process can cause a significant rise in substrate temperature, which may affect the properties of the substrate or the deposited film.
- Impurity Gas Susceptibility: High substrate temperatures can also make the process more susceptible to contamination from impurity gases.
-
Vacuum Requirements:
- Lesser Vacuum Range: Sputtering operates under a lesser vacuum range compared to evaporation, which increases the likelihood of introducing impurities into the substrate.
- Comparison with Evaporation: This makes sputtering less suitable for applications where ultra-high purity is required.
Understanding these limitations is essential for optimizing the sputtering process and selecting the most appropriate deposition technique for specific applications. While sputtering offers many advantages, such as the ability to deposit a wide range of materials and produce high-quality films, these limitations must be carefully considered to ensure the desired outcomes are achieved.
Summary Table:
Limitation | Cause/Impact |
---|---|
Film Contamination | Impurities from source materials degrade film quality. |
High Capital and Operational Costs | Complex equipment and cooling systems increase costs and reduce efficiency. |
Low Deposition Rates | Certain materials like SiO2 have slow deposition rates, impacting production. |
Difficulty in Controlling Film Thickness | Challenges in achieving precise, uniform thin films. |
Challenges with Material Selection | Limited by melting temperatures and degradation of organic solids. |
Integration with Lift-Off Processes | Shadowing issues and contamination risks complicate structuring. |
Substrate Temperature Rise | Thermal effects and impurity gas susceptibility affect film properties. |
Vacuum Requirements | Lesser vacuum range increases impurity risks compared to evaporation. |
Need help selecting the right deposition method for your application? Contact our experts today!