Sputtering is a widely used thin-film deposition technique where the thickness of the deposited film typically ranges from angstroms to microns. The maximum thickness achievable depends on several factors, including the sputtering time, power applied to the target, material properties, and process conditions. While sputtering is versatile and capable of producing uniform coatings, it faces challenges such as film contamination, temperature constraints, and limitations in controlling thickness precisely. These factors collectively influence the practical upper limit of film thickness in sputtering applications.
Key Points Explained:
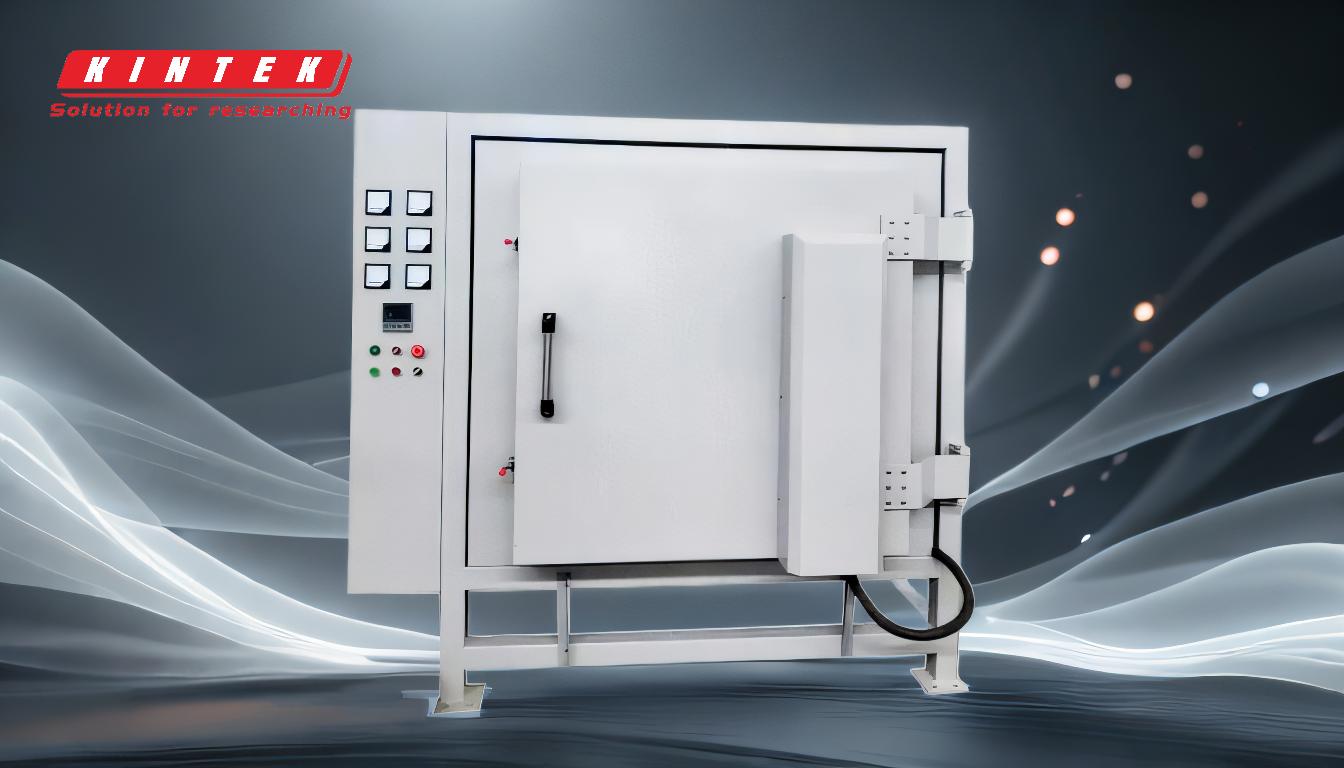
-
Typical Thickness Range in Sputtering:
- Sputtering produces coatings with thicknesses ranging from angstroms to microns.
- This range is suitable for applications requiring thin films, such as semiconductors, optical coatings, and protective layers.
-
Factors Influencing Maximum Thickness:
- Sputtering Time: Longer deposition times generally result in thicker films, but this is limited by practical considerations such as production efficiency.
- Power Applied to the Target: Higher power levels increase the sputtering rate, enabling thicker deposits, but excessive power can lead to overheating and contamination.
- Material Properties: The melting temperature and sputtering yield of the target material affect how easily it can be deposited and how thick the film can grow.
- Energy of Coating Particles: Particles with higher energy (ranging from tens to thousands of electron volts) can contribute to thicker and denser films.
-
Challenges in Achieving Maximum Thickness:
- Film Contamination: Impurities from the target or environment can diffuse into the film, limiting its quality and thickness.
- Temperature Constraints: High temperatures during deposition can cause undesirable stresses during cooling, affecting film integrity.
- Uniformity and Purity: Achieving uniform thickness and high purity becomes increasingly difficult as the film grows thicker.
-
Practical Limitations:
- Cooling Systems: The need for cooling systems to manage heat generation reduces production rates and increases energy costs.
- Material Selection: Materials with very high melting points or low sputtering yields are challenging to deposit in thick layers.
- Sidewall Coverage: In applications requiring liftoff processes, sputtering's tendency to deposit on sidewalls can complicate achieving precise thickness control.
-
Applications and Desired Thickness:
- Conformal Coatings: Sputtering is ideal for applications requiring uniform coatings over complex geometries, where thickness control is critical.
- Layered Structures: Multiple materials can be deposited in layers, with each layer's thickness carefully controlled to meet specific functional requirements.
-
Conclusion on Maximum Thickness:
- While sputtering can theoretically deposit films up to several microns thick, practical limitations such as contamination, temperature management, and uniformity challenges often restrict the achievable thickness.
- The maximum thickness is highly dependent on the specific application, material, and process parameters, making it essential to optimize these factors for each use case.
In summary, the maximum thickness in sputtering is influenced by a combination of process parameters, material properties, and practical constraints. While the technique is versatile and capable of producing films ranging from angstroms to microns, achieving thicker films requires careful optimization and consideration of the associated challenges.
Summary Table:
Aspect | Details |
---|---|
Typical Thickness Range | Angstroms to microns |
Key Factors | Sputtering time, power, material properties, and energy of coating particles |
Challenges | Film contamination, temperature constraints, uniformity, and purity |
Practical Limitations | Cooling systems, material selection, and sidewall coverage |
Applications | Semiconductors, optical coatings, conformal coatings, and layered structures |
Optimize your sputtering process for maximum thickness—contact our experts today!