Sputtering is a physical vapor deposition (PVD) process used to deposit thin films of material onto a substrate. It involves bombarding a target material with high-energy ions, typically from an inert gas like argon, in a vacuum environment. The ions transfer kinetic energy to the target atoms, causing them to be ejected from the surface. These ejected atoms then travel through the vacuum chamber and deposit onto a substrate, forming a thin film with precise properties such as reflectivity, electrical resistivity, or ionic resistivity. The process is highly controllable, allowing for the creation of films with specific morphology, grain orientation, and density.
Key Points Explained:
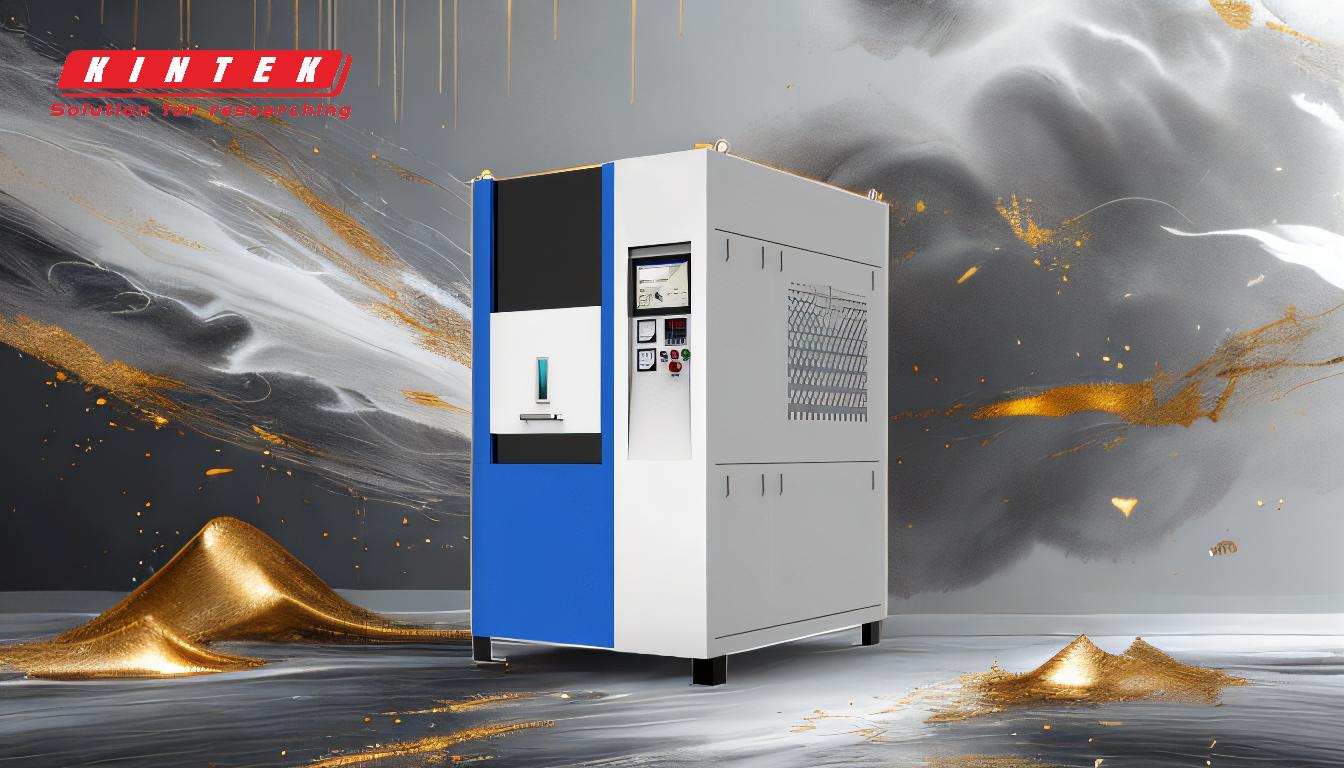
-
Ion Bombardment and Energy Transfer:
- In sputtering, a plasma is created by ionizing an inert gas (e.g., argon) in a vacuum chamber.
- The ions are accelerated by an electric field toward the target material, which acts as the cathode.
- When these high-energy ions collide with the target, they transfer their kinetic energy to the target atoms.
- This energy transfer causes a cascade of collisions within the target material, leading to the ejection of atoms or molecules from the surface.
-
Ejection of Target Atoms:
- The kinetic energy from the incident ions must exceed the binding energy of the target atoms to eject them.
- Ejected atoms are typically in a neutral state, though some may become ionized during the process.
- The ejected atoms form a vapor stream that travels through the vacuum chamber.
-
Deposition onto Substrate:
- The ejected atoms traverse the chamber and adhere to the substrate, which is usually positioned opposite the target.
- The substrate acts as the anode in the electric field, attracting any ionized particles.
- The deposited atoms nucleate and grow into a thin film with specific properties, such as reflectivity, electrical conductivity, or resistance.
-
Role of Plasma and Electric Field:
- A plasma is essential for generating the ions needed for sputtering. It is created by applying a voltage between the target (cathode) and substrate (anode).
- The electric field accelerates the ions toward the target, ensuring they have sufficient energy to eject target atoms.
-
Control Over Film Properties:
- Sputtering allows precise control over film characteristics, including morphology, grain size, and density.
- This precision makes sputtering ideal for applications requiring high-quality thin films, such as in semiconductor manufacturing, optical coatings, and protective layers.
-
Vacuum Environment:
- The process occurs in a vacuum to minimize contamination and ensure the ejected atoms travel unimpeded to the substrate.
- The vacuum also helps maintain the stability of the plasma and prevents unwanted chemical reactions.
-
Applications of Sputtering:
- Sputtering is widely used in industries requiring high precision, such as electronics (e.g., semiconductor devices), optics (e.g., anti-reflective coatings), and materials science (e.g., wear-resistant coatings).
- It is also used in research and development to create thin films with tailored properties for specific applications.
By understanding these key points, one can appreciate the physics of sputtering as a highly controlled and versatile process for depositing thin films with exceptional precision and uniformity.
Summary Table:
Key Aspect | Description |
---|---|
Process | Physical vapor deposition (PVD) using high-energy ions to eject target atoms. |
Key Components | Plasma, electric field, vacuum chamber, target material, and substrate. |
Control Over Film Properties | Precise control of morphology, grain size, density, and electrical properties. |
Applications | Semiconductors, optical coatings, wear-resistant layers, and R&D. |
Environment | Vacuum to minimize contamination and ensure stable plasma. |
Discover how sputtering can enhance your precision applications—contact our experts today!