The sputtering process is a precise and controlled method used to deposit thin films of material onto a substrate. It involves creating a vacuum environment, introducing an inert gas (typically argon), and generating a plasma by ionizing the gas. The plasma's ions are accelerated towards a target material, causing atoms to be ejected from the target's surface. These ejected atoms then travel through the vacuum chamber and deposit onto a substrate, forming a thin film with specific properties. The process is highly accurate and is widely used in industries requiring precision coatings, such as semiconductors, optics, and electronics.
Key Points Explained:
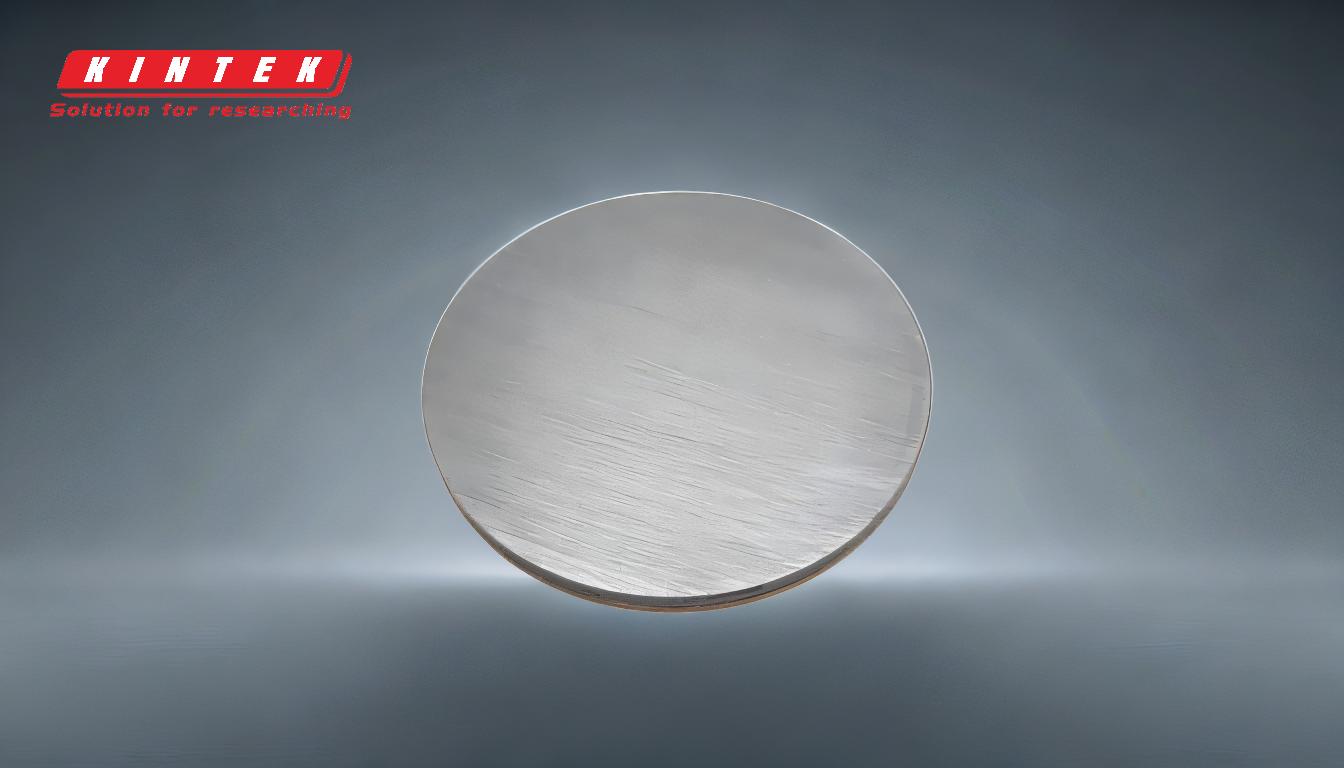
-
Vacuum Chamber Setup:
- The process begins by placing the target material (source) and the substrate (destination) inside a vacuum chamber.
- The internal pressure is reduced to around 1 Pa (0.0000145 psi) to remove moisture and impurities, ensuring a clean environment for the deposition process.
-
Introduction of Inert Gas:
- An inert gas, typically argon, is introduced into the chamber to create a low-pressure atmosphere.
- The choice of argon is due to its inert nature, which prevents unwanted chemical reactions during the sputtering process.
-
Plasma Generation:
- A high voltage (3-5 kV) is applied to ionize the argon atoms, creating a plasma composed of positively charged argon ions (Ar+).
- A magnetic field is often used to confine and control the plasma, enhancing the efficiency of the sputtering process.
-
Ion Bombardment:
- The positively charged argon ions are accelerated towards the negatively charged target (cathode) due to the applied electric field.
- Upon collision, the ions transfer their kinetic energy to the target material, causing atoms to be ejected from the target's surface.
-
Atom Ejection and Transport:
- The ejected atoms from the target material enter the gaseous state within the vacuum chamber.
- These atoms travel through the chamber, either by line of sight or by being ionized and accelerated towards the substrate.
-
Film Deposition:
- The ejected atoms condense onto the substrate, forming a thin film.
- The properties of the film, such as reflectivity, electrical resistivity, and density, can be precisely controlled by adjusting parameters like pressure, temperature, and the magnetic field.
-
Temperature Control:
- The chamber may be heated to temperatures ranging from 150 – 750°C (302 – 1382°F) depending on the specific requirements of the coating being applied.
- Temperature control is crucial for achieving the desired film morphology, grain orientation, and density.
-
Process Optimization:
- The entire process is highly optimized to ensure uniformity and precision in the deposited film.
- Parameters such as gas pressure, voltage, and magnetic field strength are carefully controlled to achieve the desired film properties.
By following these steps, the sputtering process enables the production of high-quality thin films with precise control over their properties, making it an essential technique in various high-tech industries.
Summary Table:
Step | Description |
---|---|
Vacuum Chamber Setup | Create a vacuum environment (~1 Pa) to remove impurities for clean deposition. |
Inert Gas Introduction | Introduce argon gas to prevent unwanted chemical reactions. |
Plasma Generation | Ionize argon gas with high voltage (3-5 kV) to create a plasma. |
Ion Bombardment | Accelerate argon ions to eject target material atoms. |
Atom Ejection & Transport | Ejected atoms travel through the chamber to the substrate. |
Film Deposition | Atoms condense on the substrate, forming a thin film with controlled properties. |
Temperature Control | Heat chamber (150–750°C) to optimize film properties. |
Process Optimization | Adjust parameters for uniform, high-quality thin films. |
Discover how the sputtering process can enhance your precision coating needs—contact us today for expert guidance!