Sputtering is a physical vapor deposition (PVD) technique used to deposit thin films of material onto a substrate. The process involves bombarding a target material with high-energy ions, typically from an inert gas like argon, which dislodges atoms from the target. These atoms then travel through a vacuum chamber and deposit onto a substrate, forming a thin, uniform film. Sputtering is widely used in industries such as semiconductors, optics, and coatings due to its ability to produce high-quality, consistent films with precise control over thickness and composition.
Key Points Explained:
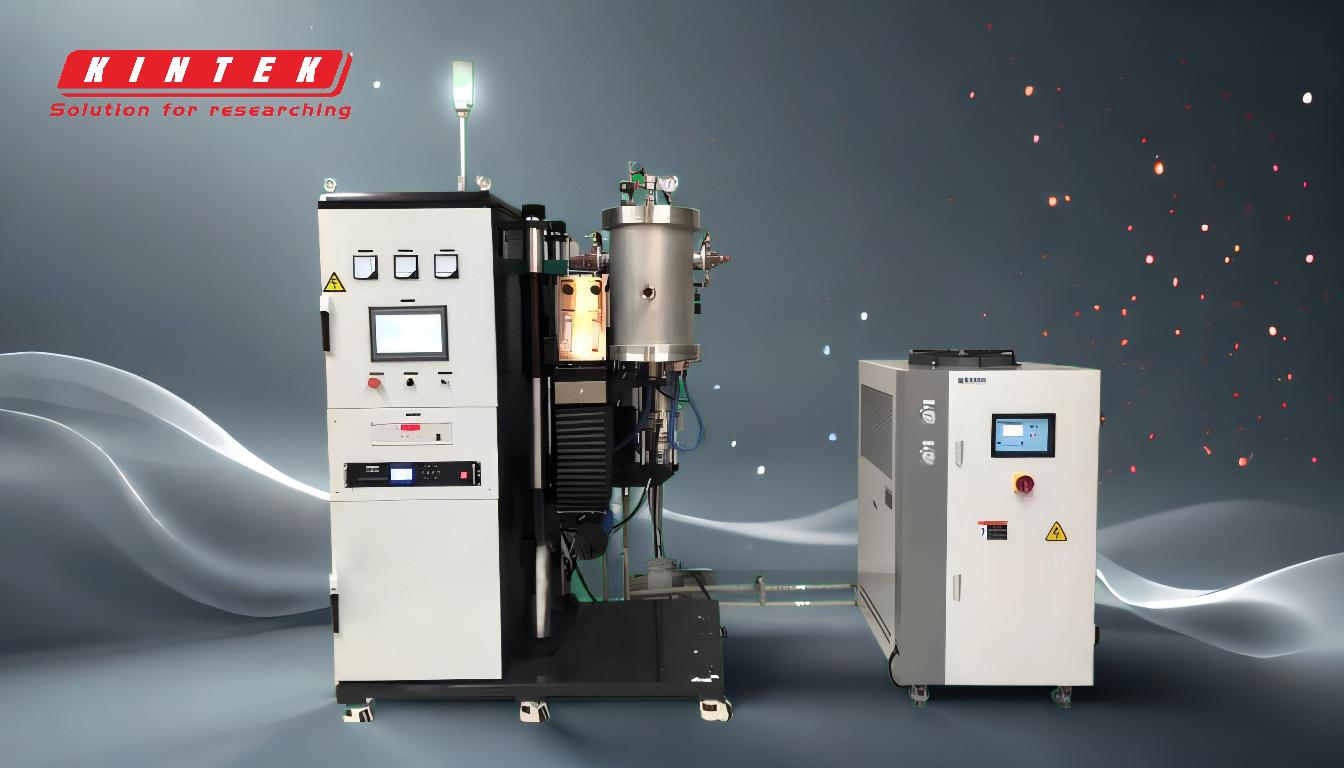
-
Mechanism of Sputtering:
- Sputtering occurs when high-energy ions, usually from an inert gas like argon, collide with a target material. The energy transfer from the ions to the target causes atoms or molecules to be ejected from the target's surface.
- These ejected particles, now in a neutral state, travel through the vacuum chamber and deposit onto a substrate, forming a thin film.
-
Uniform Deposition:
- The low-pressure environment in the sputtering chamber ensures that the ejected particles travel in a straight line, leading to highly uniform deposition.
- This uniformity is critical for applications requiring consistent film thickness, such as in semiconductor manufacturing or optical coatings.
-
Applications of Sputtering:
- Semiconductors: Sputtering is used to deposit thin films of conductive, insulating, or semiconducting materials onto silicon wafers, essential for creating integrated circuits.
- Optics: Thin films deposited via sputtering are used to create anti-reflective coatings, mirrors, and other optical components.
- Coatings: Sputtering is employed to apply protective or functional coatings, such as wear-resistant layers on tools or decorative finishes on consumer products.
-
Advantages of Sputtering:
- Precision: Sputtering allows for precise control over film thickness and composition, making it suitable for applications requiring high accuracy.
- Versatility: A wide range of materials, including metals, alloys, and ceramics, can be deposited using sputtering.
- Quality: The films produced are typically dense, adherent, and free from defects, ensuring high performance in their intended applications.
-
Types of Sputtering:
- DC Sputtering: Uses a direct current power source to generate the plasma, suitable for conductive materials.
- RF Sputtering: Utilizes radio frequency power, enabling the deposition of insulating materials.
- Magnetron Sputtering: Incorporates magnetic fields to enhance the efficiency of the sputtering process, commonly used for high-quality film deposition.
By understanding the purpose and process of sputtering, purchasers of equipment and consumables can make informed decisions about the best techniques and materials for their specific applications.
Summary Table:
Aspect | Details |
---|---|
Mechanism | High-energy ions dislodge target atoms, depositing them onto a substrate. |
Uniform Deposition | Ensures consistent film thickness for critical applications. |
Applications | Semiconductors, optics, and protective coatings. |
Advantages | Precision, versatility, and high-quality films. |
Types | DC, RF, and Magnetron sputtering for different materials and applications. |
Ready to enhance your thin film deposition process? Contact us today for expert guidance!