Glass-lined reactors are specialized equipment designed for chemical processes where corrosion resistance, purity, and process integrity are critical. They combine the strength of steel with the corrosion resistance and smooth surface of glass, making them ideal for handling corrosive substances, maintaining high purity, and operating under high temperatures and pressures. These reactors are widely used in industries such as fine chemicals, biopharmaceuticals, and new material synthesis, offering advantages like precise temperature control, solvent distillation, and accelerated reaction rates. Their robust design ensures long-term reliability and efficiency in demanding applications.
Key Points Explained:
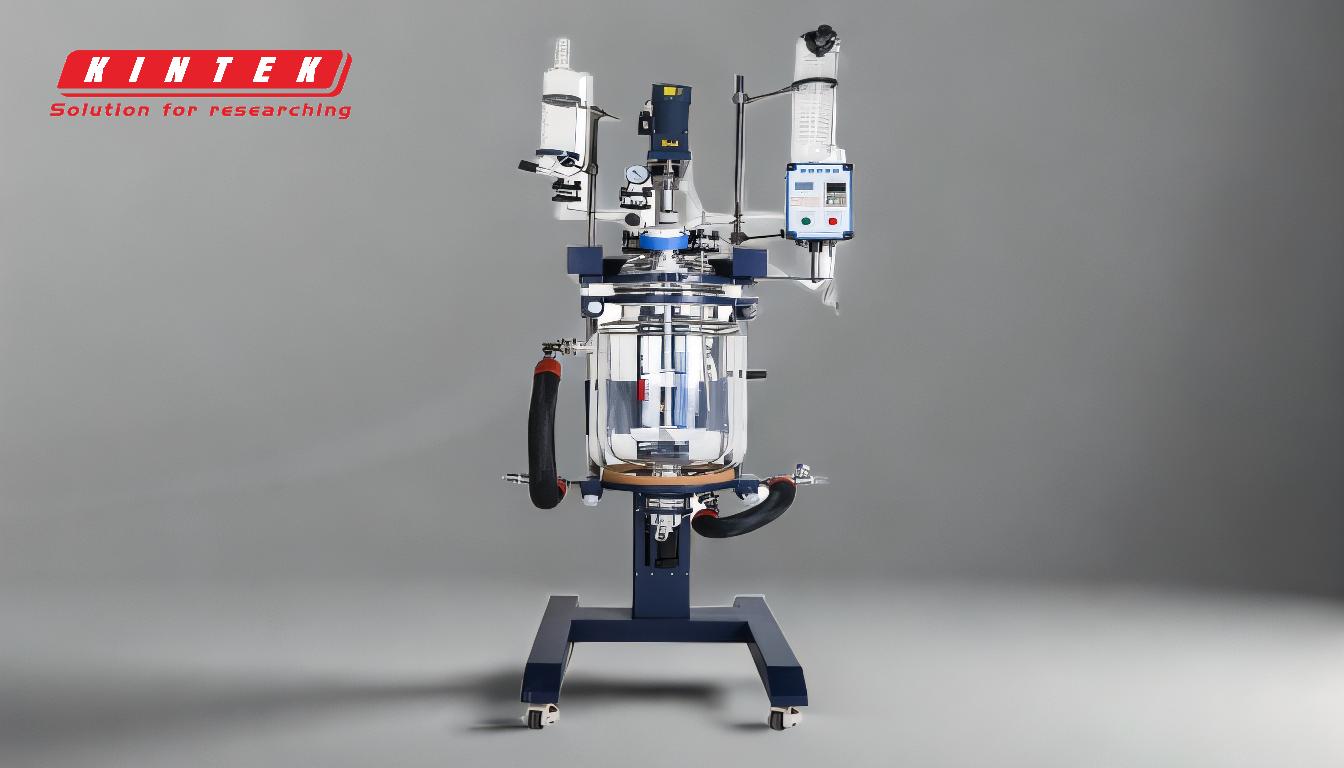
-
Corrosion Resistance and Purity:
- Glass-lined reactors are specifically designed to handle corrosive substances, such as acids and bases, without degradation.
- The glass lining provides a smooth, non-reactive surface that prevents contamination of the chemical process, ensuring high purity.
- This makes them indispensable in industries where chemical integrity and product quality are paramount.
-
Combination of Steel Strength and Glass Properties:
- The external steel construction provides structural strength, enabling the reactor to withstand high operating pressures and mechanical stresses.
- The internal glass lining is fused to the steel, creating a strong bond (approximately 16,000 psi) that ensures durability and resistance to thermal and chemical shocks.
- This combination allows the reactor to operate effectively in demanding environments.
-
Versatility in Applications:
- Glass-lined reactors are used in a wide range of industries, including fine chemicals, biopharmaceuticals, new material synthesis, and scientific research.
- They are available in single-layer, double-layer, and three-layer configurations, catering to different process requirements.
- Their ability to handle both heating and cooling processes makes them versatile for various chemical reactions.
-
Temperature and Pressure Control:
- These reactors can operate at high temperatures and pressures, making them suitable for reactions that require precise thermal control.
- They enable reactions above the boiling point of solvents, which is not feasible with traditional round-bottom flasks.
- This capability accelerates reaction rates and improves process efficiency.
-
Enhanced Reaction Efficiency:
- Glass-lined reactors reduce reaction volumes compared to traditional equipment, leading to faster reaction times and higher throughput.
- They support solvent distillation and refluxing, allowing for efficient separation and purification of reaction products.
- The ability to control temperature and pressure precisely ensures optimal reaction conditions.
-
Long-Term Reliability:
- Recognized as a standard in the chemical process industry, glass-lined reactors are known for their top-quality design and construction.
- Their robust build ensures long and dependable service, even in harsh chemical environments.
- This reliability reduces downtime and maintenance costs, making them a cost-effective solution for industrial applications.
-
Specialized Configurations:
- Single-layer reactors are ideal for basic stirring and temperature control applications.
- Double-layer and three-layer reactors offer additional features, such as enhanced insulation or the ability to handle more complex processes.
- These configurations provide flexibility to meet specific process requirements.
In summary, glass-lined reactors are essential equipment for industries requiring high corrosion resistance, purity, and process control. Their unique combination of steel strength and glass properties, along with their versatility and reliability, makes them a preferred choice for demanding chemical processes.
Summary Table:
Feature | Description |
---|---|
Corrosion Resistance | Handles corrosive substances like acids and bases without degradation. |
High Purity | Smooth, non-reactive glass lining prevents contamination. |
Steel Strength | External steel construction withstands high pressures and mechanical stresses. |
Temperature Control | Operates at high temperatures and pressures for precise thermal control. |
Versatility | Used in fine chemicals, biopharmaceuticals, and new material synthesis. |
Reaction Efficiency | Reduces reaction volumes, accelerates rates, and supports solvent distillation. |
Long-Term Reliability | Robust design ensures dependable service in harsh chemical environments. |
Configurations | Available in single-layer, double-layer, and three-layer designs for flexibility. |
Ready to enhance your chemical processes with glass-lined reactors? Contact us today to learn more!