Sputtering is a physical vapor deposition (PVD) process used to deposit thin films of materials onto substrates. It involves bombarding a target material with high-energy ions, typically from an inert gas like argon, causing atoms or molecules to be ejected from the target surface. These ejected particles then deposit onto a substrate, forming a thin film. The range of sputtering, or the distance over which sputtered particles travel, depends on factors such as the energy of the incident ions, the mass of the target atoms, the angle of incidence, and the vacuum conditions in the chamber. The sputtering yield, which quantifies the efficiency of the process, is influenced by these parameters and varies across different materials and conditions.
Key Points Explained:
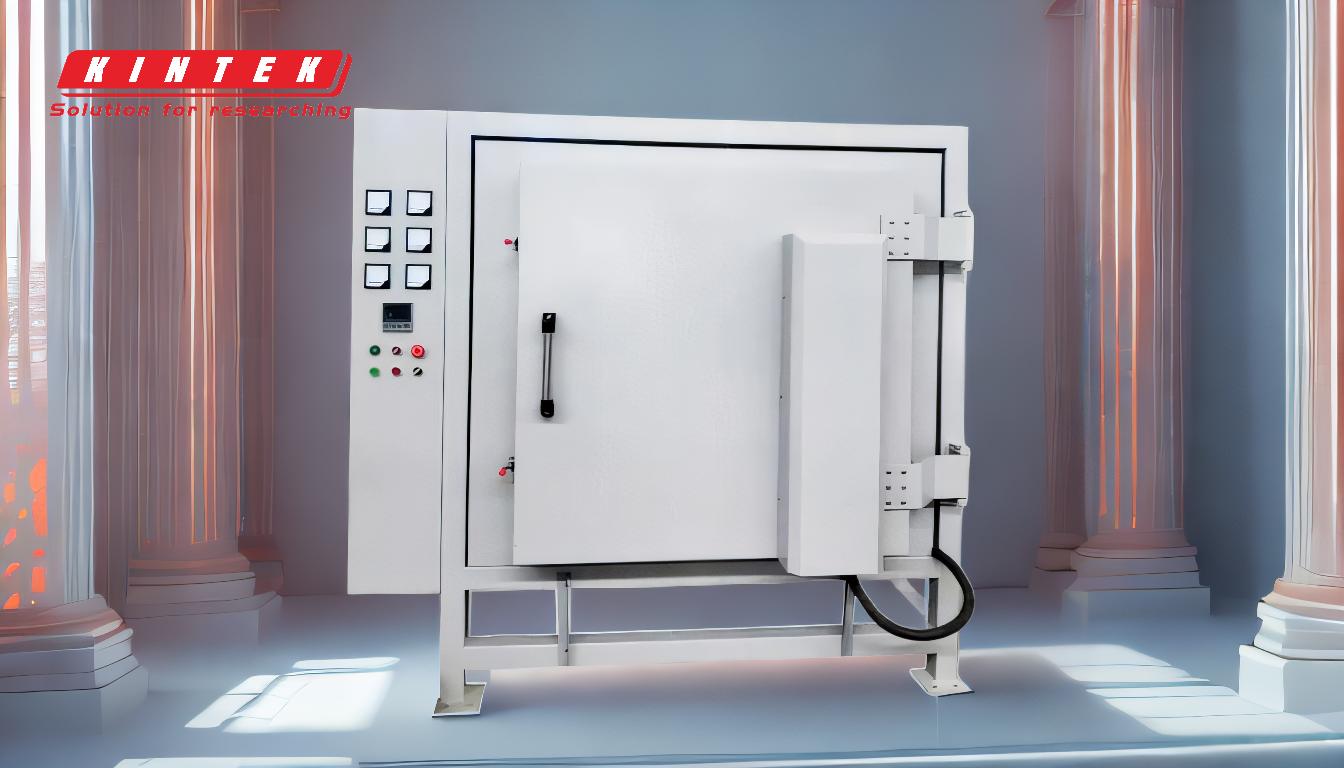
-
Definition of Sputtering Range:
- The range of sputtering refers to the distance that sputtered particles travel from the target material to the substrate. This distance is influenced by the energy of the incident ions, the properties of the target material, and the vacuum environment.
-
Factors Influencing Sputtering Range:
- Incident Ion Energy: Higher energy ions can eject target atoms with greater kinetic energy, increasing the distance they travel before depositing on the substrate.
- Mass of Ions and Target Atoms: Heavier ions and target atoms result in higher momentum transfer, which can increase the sputtering yield and the range of sputtered particles.
- Angle of Incidence: The angle at which ions strike the target affects the trajectory and energy distribution of the ejected particles, influencing their travel distance.
- Vacuum Conditions: Sputtering requires a high vacuum to minimize collisions between sputtered particles and residual gas molecules, ensuring a longer mean free path and greater deposition range.
-
Sputtering Yield:
- The sputtering yield (S) is the number of target atoms ejected per incident ion. It is a key metric that determines the efficiency of the sputtering process. The yield depends on the factors mentioned above and varies for different materials and sputtering conditions.
-
Equation for Sputtering Rate:
- The sputtering rate, which quantifies the amount of material removed from the target per unit time, is given by the equation:
[
\text{Sputtering rate} = \frac{MSj}{pN_A e}
]
where:
- ( M ) = molar weight of the target material,
- ( S ) = sputtering yield,
- ( j ) = ion current density,
- ( p ) = material density,
- ( N_A ) = Avogadro's number,
- ( e ) = electron charge.
- This equation highlights the relationship between the sputtering rate and the physical properties of the target material and the sputtering conditions.
- The sputtering rate, which quantifies the amount of material removed from the target per unit time, is given by the equation:
[
\text{Sputtering rate} = \frac{MSj}{pN_A e}
]
where:
-
Role of Vacuum in Sputtering:
- Sputtering is performed under high vacuum to ensure that the sputtered particles travel unimpeded to the substrate. A lower vacuum would increase the likelihood of collisions with residual gas molecules, reducing the effective range of sputtering and the quality of the deposited film.
-
Influence of Chamber Pressure and Power Source:
- Chamber Pressure: Optimal chamber pressure improves the coverage and uniformity of the deposited film by controlling the mean free path of the sputtered particles.
- Power Source: The type of power source (DC or RF) affects the deposition rate, material compatibility, and cost. RF sputtering is often used for insulating materials, while DC sputtering is suitable for conductive targets.
-
Kinetic Energy and Surface Mobility:
- The kinetic energy of the sputtered particles determines their direction and deposition on the substrate. Higher energy particles can lead to better adhesion and film quality. Additionally, the excess energy of metal ions can increase surface mobility during deposition, enhancing the uniformity and density of the film.
In summary, the range of sputtering is determined by a combination of physical and environmental factors, including ion energy, target material properties, vacuum conditions, and process parameters. Understanding these factors is essential for optimizing the sputtering process and achieving high-quality thin film deposition.
Summary Table:
Key Factor | Impact on Sputtering Range |
---|---|
Incident Ion Energy | Higher energy increases particle travel distance. |
Mass of Ions/Target Atoms | Heavier ions/atoms enhance momentum transfer, increasing range. |
Angle of Incidence | Affects particle trajectory and energy distribution, influencing range. |
Vacuum Conditions | High vacuum ensures longer mean free path, reducing collisions and increasing range. |
Sputtering Yield (S) | Determines efficiency; higher yield improves deposition range. |
Chamber Pressure | Optimal pressure improves film uniformity and coverage. |
Power Source | DC or RF affects deposition rate, material compatibility, and cost. |
Ready to optimize your sputtering process? Contact our experts today for tailored solutions!