The sputtering yield is a critical parameter in sputtering processes, representing the average number of atoms ejected from a target material per incident ion. It is influenced by several factors, including the energy and angle of the incident ions, the masses of the ions and target atoms, the surface binding energy of the target material, and, in crystalline materials, the orientation of the crystal axes relative to the surface. These factors collectively determine the efficiency of the sputtering process, impacting deposition rates and the quality of thin films in applications like semiconductor manufacturing and surface coatings.
Key Points Explained:
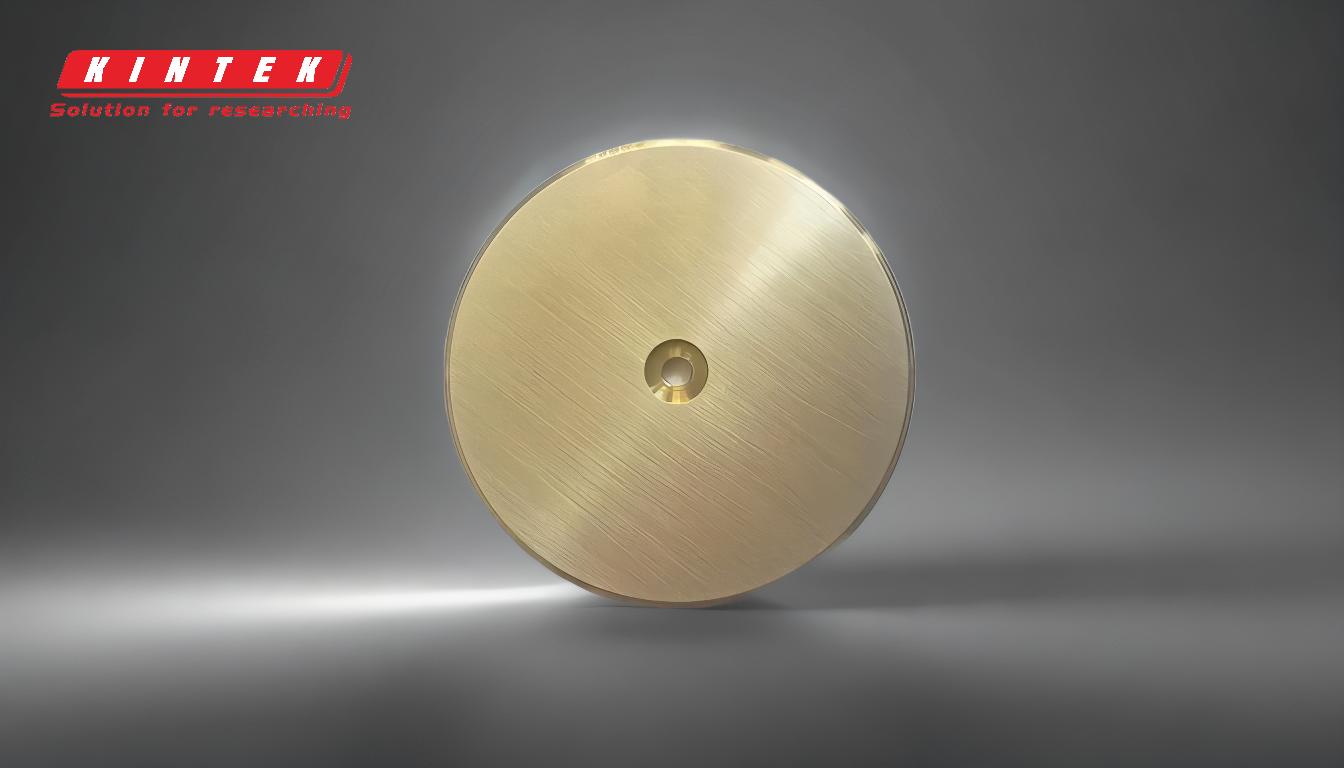
-
Definition of Sputtering Yield:
- The sputtering yield is defined as the average number of atoms ejected from a target material per incident ion. This metric is crucial for understanding the efficiency of the sputtering process, as it directly affects the deposition rate and the quality of the resulting thin films.
-
Factors Influencing Sputtering Yield:
- Energy of Incident Ions: The sputtering yield increases with the energy of the incident ions, typically within the range of 10 to 5000 eV. Higher energy ions can transfer more momentum to the target atoms, leading to more efficient ejection.
- Angle of Ion Impact: The angle at which ions collide with the target surface can significantly affect the sputtering yield. Generally, there is an optimal angle (often around 45 degrees) that maximizes the yield due to enhanced momentum transfer.
- Masses of Ions and Target Atoms: The relative masses of the incident ions and the target atoms play a crucial role. Heavier ions or lighter target atoms can lead to higher sputtering yields due to more effective momentum transfer.
- Surface Binding Energy: The energy required to dislodge an atom from the target surface (surface binding energy) inversely affects the sputtering yield. Materials with lower binding energies tend to have higher sputtering yields.
- Crystalline Structure: For crystalline materials, the orientation of the crystal axes relative to the surface can influence the sputtering yield. Certain orientations may facilitate easier ejection of atoms, leading to higher yields.
-
Applications and Implications:
- Deposition Rate: The sputtering yield directly impacts the deposition rate in sputter deposition processes. Higher yields result in faster deposition, which is beneficial for industrial applications requiring high throughput.
- Film Quality: Understanding and controlling the sputtering yield is essential for achieving desired film properties, such as uniformity, density, and adhesion. Variations in yield can lead to inconsistencies in film thickness and quality.
- Material Selection: Knowledge of sputtering yields for different materials helps in selecting appropriate targets for specific applications. For example, materials with high sputtering yields are preferred for processes requiring rapid deposition.
-
Experimental and Theoretical Considerations:
- Measurement Techniques: Sputtering yields are often determined experimentally using techniques like weight loss measurements or surface analysis methods. Theoretical models, such as those based on the Sigmund theory, also provide valuable insights into the sputtering process.
- Energy Range: The sputtering yield is most relevant in the energy range of 10 to 5000 eV. Below this range, sputtering may not occur efficiently, while above it, other processes like implantation may dominate.
-
Practical Considerations for Equipment and Consumables:
- Ion Source Design: The design of the ion source in sputtering equipment must consider factors like ion energy and angle to optimize the sputtering yield. This includes the configuration of the ion gun and the target holder.
- Target Material Properties: The choice of target material should take into account its sputtering yield, binding energy, and crystalline structure. For example, materials with low binding energies and favorable crystalline orientations are preferred for high-yield applications.
- Process Parameters: Operating parameters such as ion energy, angle of incidence, and plasma gas pressure must be carefully controlled to achieve consistent and optimal sputtering yields. This requires precise tuning of the equipment settings.
By understanding these key points, equipment and consumable purchasers can make informed decisions about the materials and processes best suited for their specific applications, ensuring efficient and high-quality sputtering outcomes.
Summary Table:
Key Factor | Impact on Sputtering Yield |
---|---|
Energy of Incident Ions | Higher energy (10-5000 eV) increases yield due to greater momentum transfer. |
Angle of Ion Impact | Optimal angle (~45°) maximizes yield by enhancing momentum transfer. |
Masses of Ions and Target Atoms | Heavier ions or lighter target atoms increase yield through effective momentum transfer. |
Surface Binding Energy | Lower binding energy leads to higher yield as atoms are more easily dislodged. |
Crystalline Structure | Certain crystal orientations facilitate higher yield by easing atom ejection. |
Optimize your sputtering process with expert insights—contact us today!