Stainless steel reactors are versatile and durable equipment widely used in laboratories and industrial settings. Their temperature range depends on the specific grade of stainless steel used, as different grades have varying thermal properties. Generally, stainless steel reactors can operate effectively within a temperature range of -200°C to 800°C, though this can vary based on the alloy composition and design. Lower-grade stainless steels may have a narrower range, while high-grade alloys can withstand more extreme temperatures. Factors such as corrosion resistance, mechanical strength, and the presence of protective coatings also influence the reactor's performance at different temperatures. Understanding these parameters is crucial for selecting the right reactor for specific applications.
Key Points Explained:
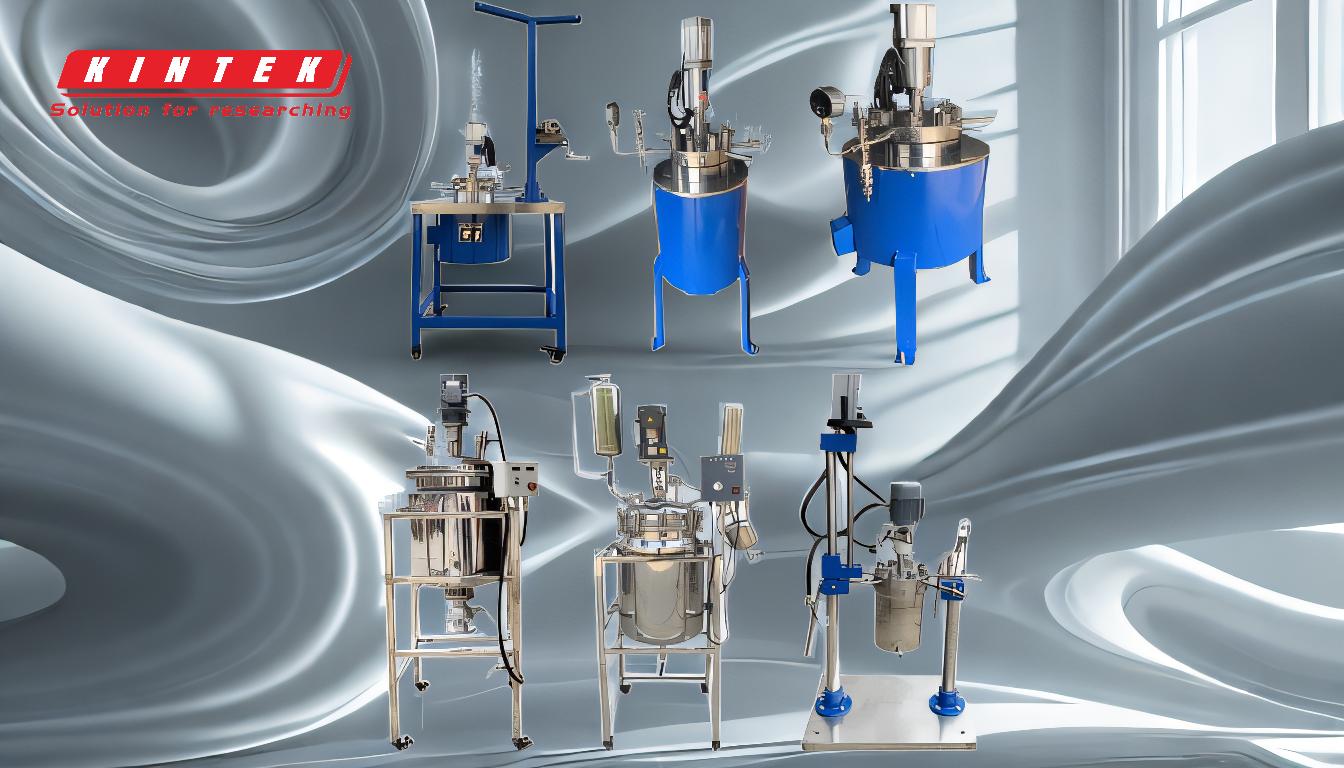
-
Temperature Range of Stainless Steel Reactors
- Stainless steel reactors typically operate within a temperature range of -200°C to 800°C.
- This range is influenced by the specific grade of stainless steel used. For example:
- Austenitic stainless steels (e.g., 304, 316): Commonly used in reactors, these grades can handle temperatures up to 800°C but may lose strength at higher temperatures.
- Ferritic and martensitic stainless steels: These grades have lower temperature limits, typically up to 500°C, due to reduced thermal stability.
- High-temperature alloys (e.g., 310S): These can withstand temperatures up to 1100°C, making them suitable for extreme conditions.
-
Factors Affecting Temperature Tolerance
- Alloy Composition: The presence of elements like chromium, nickel, and molybdenum enhances thermal stability and corrosion resistance.
- Design and Thickness: Thicker reactor walls and reinforced designs can improve heat resistance.
- Protective Coatings: Special coatings or linings can extend the temperature range by providing additional thermal and chemical protection.
-
Applications and Limitations
- Low-Temperature Applications: Stainless steel reactors are suitable for cryogenic processes, such as those in chemical or pharmaceutical industries, due to their ability to withstand temperatures as low as -200°C.
- High-Temperature Applications: They are ideal for processes like polymerization, distillation, and chemical synthesis, where temperatures can reach up to 800°C.
- Limitations: Stainless steel reactors may not be suitable for extremely high-temperature processes (above 800°C) or those involving strong acids or alkalis, as these conditions can accelerate corrosion and reduce lifespan.
-
Maintenance and Durability
- Stainless steel reactors are known for their high mechanical strength and resistance to abrasion, making them durable for long-term use.
- However, they require regular maintenance, especially when exposed to extreme temperatures or corrosive substances, to prevent degradation and ensure optimal performance.
-
Considerations for Purchasers
- Grade Selection: Choose the appropriate stainless steel grade based on the intended temperature range and chemical environment.
- Design Features: Opt for reactors with reinforced designs or protective coatings if operating at extreme temperatures.
- Cost vs. Performance: Balance the initial cost with the reactor's durability and maintenance requirements to ensure long-term value.
By understanding these key points, purchasers can make informed decisions when selecting stainless steel reactors for their specific needs.
Summary Table:
Aspect | Details |
---|---|
Temperature Range | -200°C to 800°C (varies by stainless steel grade) |
Common Grades | Austenitic (304, 316): up to 800°C; Ferritic/Martensitic: up to 500°C |
High-Temperature Alloys | 310S: withstands up to 1100°C |
Key Factors | Alloy composition, design thickness, protective coatings |
Applications | Cryogenic processes (-200°C), polymerization, distillation (up to 800°C) |
Limitations | Not suitable for temperatures above 800°C or strong acids/alkalis |
Maintenance | Regular upkeep required for durability and optimal performance |
Ready to find the perfect stainless steel reactor for your needs? Contact us today for expert guidance!