Thickness uniformity in sputtering refers to the consistency of the thin film's thickness across the substrate during the deposition process. It is a critical parameter in thin film manufacturing, as it directly impacts the performance and reliability of the final product. Achieving high thickness uniformity requires precise control over various factors, such as target-substrate distance, ion energy, target erosion area, temperature, and gas pressure. These factors influence the deposition rate and the distribution of the coating particles, which in turn affect the uniformity of the film. Understanding and optimizing these parameters is essential for producing high-quality thin films with consistent properties.
Key Points Explained:
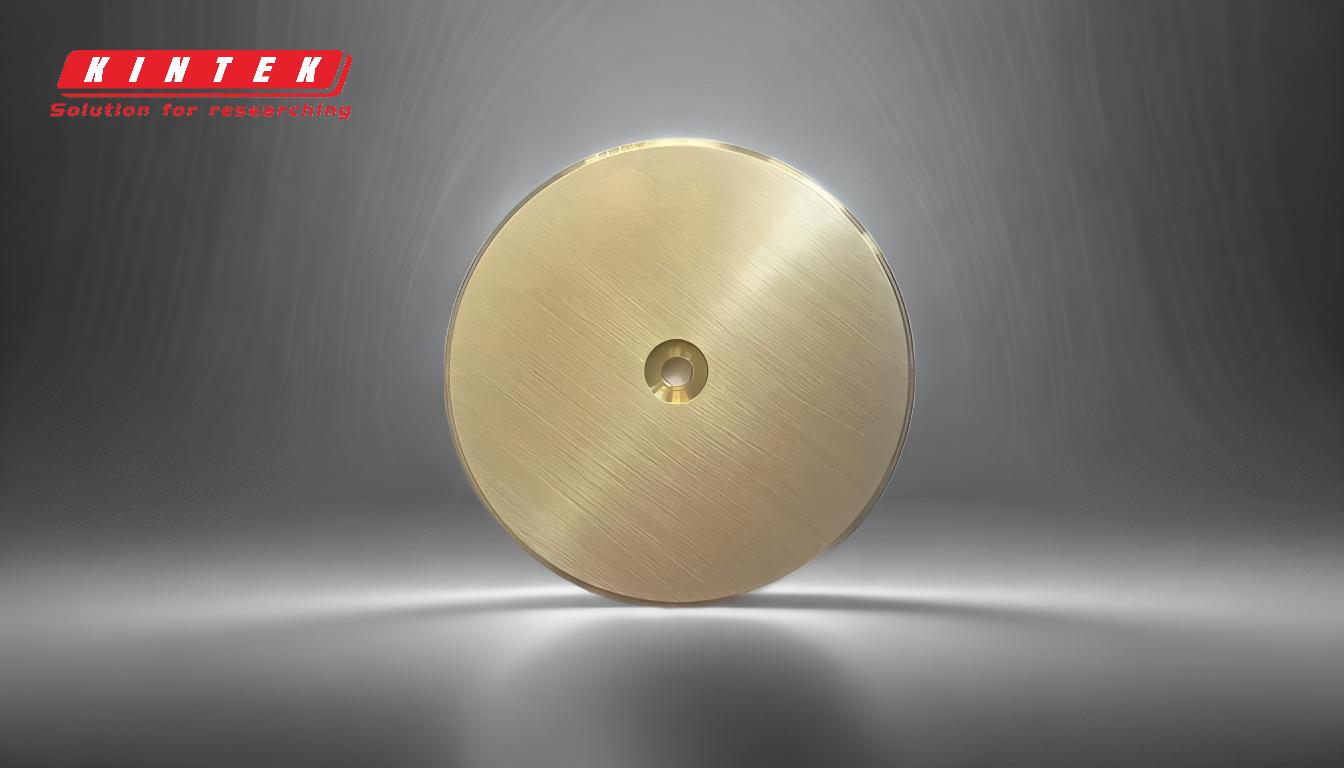
-
Definition of Thickness Uniformity:
- Thickness uniformity refers to the consistency of the thin film's thickness across the substrate. It is a measure of how evenly the material is deposited during the sputtering process.
- Uniformity is crucial for ensuring that the film performs consistently across its entire surface, which is particularly important in applications like semiconductors, optical coatings, and solar cells.
-
Factors Affecting Thickness Uniformity:
- Target-Substrate Distance: The distance between the target (the material being sputtered) and the substrate (the surface being coated) plays a significant role in determining thickness uniformity. A shorter distance generally leads to higher deposition rates but may reduce uniformity due to uneven particle distribution. Conversely, a longer distance can improve uniformity but may decrease the deposition rate.
- Ion Energy: The energy of the ions used in the sputtering process affects the deposition rate and the quality of the film. Higher ion energy can lead to more efficient sputtering but may also cause uneven deposition if not properly controlled.
- Target Erosion Area: The size and shape of the target erosion area influence the distribution of sputtered particles. A larger erosion area can lead to more uniform deposition, while a smaller area may result in uneven thickness.
- Temperature: The temperature of the substrate and the sputtering environment can affect the mobility of the deposited atoms, influencing the film's uniformity. Higher temperatures can improve uniformity by allowing atoms to spread more evenly across the substrate.
- Gas Pressure: The pressure of the sputtering gas (usually argon) affects the mean free path of the sputtered particles. Optimal gas pressure ensures that particles travel uniformly to the substrate, improving thickness uniformity.
-
Deposition Rate and Uniformity:
- The deposition rate, or how quickly the material is deposited onto the substrate, is inversely related to thickness uniformity. Higher deposition rates often lead to less uniform films because the particles do not have enough time to spread evenly across the substrate.
- Balancing the deposition rate with the need for uniformity is a key challenge in sputtering. This can be achieved by adjusting parameters such as power, temperature, and target-substrate distance.
-
Geometric Parameters:
- Source to Substrate Distance: The distance between the sputtering source and the substrate is critical. If the distance is too short, the film may be thicker near the center and thinner at the edges. If the distance is too long, the film may be too thin overall.
- Cathode Angle: The angle at which the sputtering cathode is positioned relative to the substrate can affect the distribution of the sputtered particles. Proper alignment is necessary to ensure uniform deposition.
- Centerline Intersection: The point where the centerline of the target intersects with the substrate should be carefully controlled to ensure even deposition across the entire substrate.
-
Importance of Uniformity in Applications:
- In many applications, such as semiconductor manufacturing, optical coatings, and solar cells, even a small variation in film thickness can significantly impact performance. For example, in optical coatings, non-uniform thickness can lead to variations in the refractive index, affecting the optical properties of the coating.
- Understanding the specific requirements of the application is essential to avoid over or under-specifying uniformity. In some cases, a high degree of uniformity may be necessary, while in others, a lower level may be acceptable.
-
Optimization of Sputtering Parameters:
- Achieving optimal thickness uniformity requires careful optimization of all relevant sputtering parameters. This often involves a combination of experimental testing and computational modeling to determine the best settings for a given application.
- Regular monitoring and adjustment of the sputtering process are necessary to maintain consistent uniformity over time.
-
Measurement and Control:
- Thickness uniformity is typically measured using techniques such as ellipsometry, profilometry, or interferometry. These methods provide precise measurements of film thickness across the substrate, allowing for adjustments to be made as needed.
- Real-time monitoring and control systems can be used to automatically adjust sputtering parameters during the deposition process, ensuring consistent uniformity.
In conclusion, thickness uniformity in sputtering is a complex but critical aspect of thin film deposition. It is influenced by a variety of factors, including target-substrate distance, ion energy, target erosion area, temperature, and gas pressure. Achieving high uniformity requires careful optimization of these parameters, as well as regular monitoring and adjustment of the sputtering process. Understanding the specific requirements of the application is essential to ensure that the film performs as intended.
Summary Table:
Factor | Impact on Uniformity |
---|---|
Target-Substrate Distance | Shorter distance increases deposition rate but may reduce uniformity. |
Ion Energy | Higher energy improves efficiency but may cause uneven deposition. |
Target Erosion Area | Larger erosion areas lead to more uniform deposition. |
Temperature | Higher temperatures improve atom mobility, enhancing uniformity. |
Gas Pressure | Optimal pressure ensures uniform particle travel to the substrate. |
Deposition Rate | Higher rates reduce uniformity; balancing rate and uniformity is crucial. |
Geometric Parameters | Proper alignment of source, cathode angle, and centerline intersection ensures uniformity. |
Need help optimizing your sputtering process for better thickness uniformity? Contact our experts today!