Sputtering targets are specialized materials used in the sputtering process, a technique employed to deposit thin films onto substrates. These targets are essential in industries such as semiconductors, renewable energy, and construction, where they help create coatings for electronic devices, solar cells, and low-radiation glass. Common materials used in sputtering targets include tantalum, niobium, titanium, tungsten, molybdenum, hafnium, and silicon, each serving specific applications. After use, sputtering targets often contain residual valuable metals, making them worth recycling to reclaim maximum value. This process requires specialized knowledge and technology to ensure efficient recovery and reuse.
Key Points Explained:
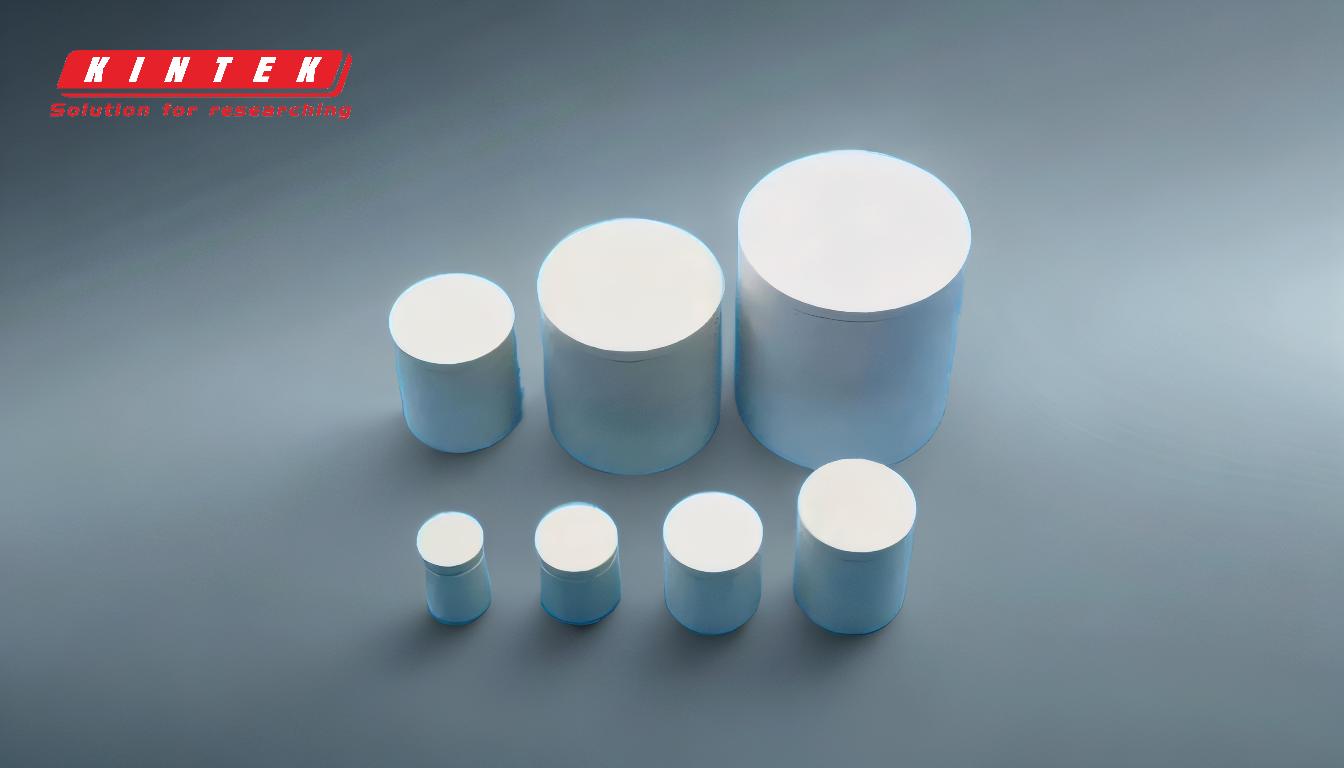
-
Definition and Purpose of Sputtering Targets:
- Sputtering targets are thin discs or sheets made of specific materials used in the sputter deposition process.
- They are designed to be bombarded with ions in a vacuum chamber, causing atoms to be ejected from the target's surface and deposited onto a substrate.
- This process creates thin films ranging from nanometers to micrometers in thickness, which are critical in various industries.
-
Applications of Sputtering Targets:
- Semiconductors: Used to deposit thin films for integrated circuits and other electronic components.
- Low-E Glass: Applied in the production of low-radiation coated glass for energy-efficient building construction.
- Thin-Film Solar Cells: Essential for creating coatings that enhance the efficiency of solar panels.
- Optoelectronics: Used in devices like LEDs and displays.
- Decorative Coatings: Provide aesthetic finishes for consumer products.
-
Common Materials Used in Sputtering Targets:
- Tantalum: Primarily used in semiconductor production due to its excellent conductivity and stability.
- Niobium: Utilized in electronics for its superconducting properties.
- Titanium: Chosen for wear-resistant and aesthetic applications.
- Tungsten: Used in decorative coatings and high-temperature applications.
- Molybdenum: Applied in solar panel coatings for its durability.
- Hafnium: Acts as an insulator in semiconductor devices.
- Silicon: Essential in solar cell production and microelectronics.
-
The Sputtering Process:
- The target material is placed in a vacuum chamber and bombarded with ions.
- The energy from the ions causes atoms to be ejected from the target's surface.
- These atoms form a spray that deposits onto a substrate, creating a thin film.
- The process is highly controlled to ensure uniformity and precision in the deposited layers.
-
Recycling and Reclamation of Used Sputtering Targets:
- Used sputtering targets often contain residual valuable metals, making them economically viable for recycling.
- Specialized knowledge and technology are required to process these targets efficiently.
- Recycling helps recover precious materials, reducing waste and promoting sustainability in industries reliant on sputtering targets.
-
Importance in Modern Technology:
- Sputtering targets play a critical role in advancing technologies such as semiconductors, renewable energy, and energy-efficient construction.
- The ability to deposit precise thin films enables the development of smaller, faster, and more efficient electronic devices.
- Their use in solar cells and low-E glass contributes to reducing energy consumption and promoting environmental sustainability.
By understanding the role and applications of sputtering targets, purchasers can make informed decisions about material selection, ensuring optimal performance and cost-effectiveness in their specific applications.
Summary Table:
Key Aspect | Details |
---|---|
Definition | Thin discs/sheets used in sputter deposition to create thin films. |
Applications | Semiconductors, low-E glass, solar cells, optoelectronics, decorative coatings. |
Common Materials | Tantalum, niobium, titanium, tungsten, molybdenum, hafnium, silicon. |
Sputtering Process | Bombardment of ions in a vacuum chamber to deposit thin films on substrates. |
Recycling | Reclaim valuable metals from used targets for sustainability. |
Importance | Critical for advancing semiconductors, renewable energy, and construction. |
Optimize your thin film deposition process with the right sputtering targets—contact our experts today!