Evaporators are crucial equipment in the chemical industry, used for concentrating solutions, recovering solvents, and separating components. The type of evaporator selected depends on factors such as the nature of the chemical solution, thermal sensitivity, energy efficiency, and scale of operation. Common types include falling film evaporators, forced circulation evaporators, and rising film evaporators, each with specific advantages tailored to different chemical processes. This answer explores the types of evaporators used in the chemical industry, their applications, and the factors influencing their selection.
Key Points Explained:
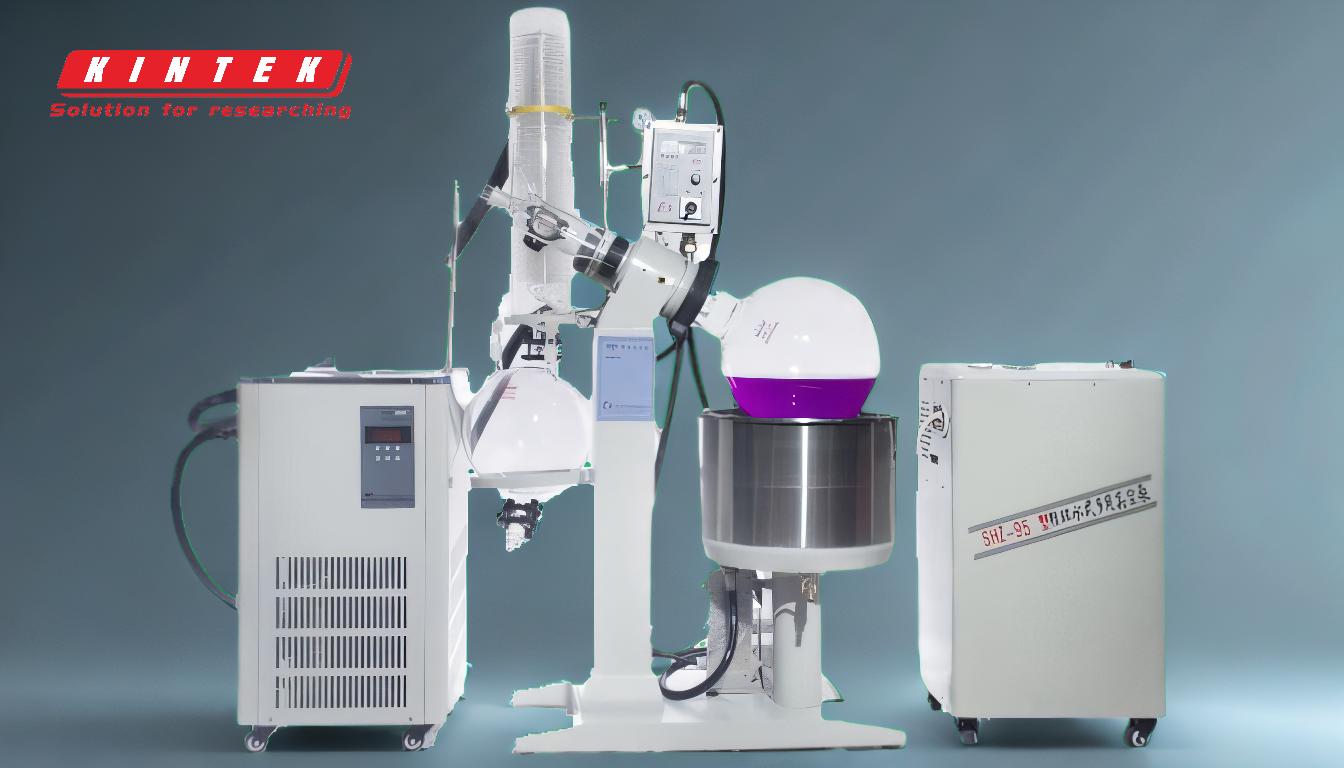
-
Types of Evaporators Used in the Chemical Industry
-
Falling Film Evaporators:
- These are widely used for heat-sensitive materials due to their low residence time and efficient heat transfer.
- Ideal for concentrating solutions with high viscosity or those prone to fouling.
- Applications include the production of polymers, organic chemicals, and specialty chemicals.
-
Forced Circulation Evaporators:
- Suitable for handling solutions with high solids content or those that are prone to scaling.
- Operate at higher pressures and temperatures, making them ideal for inorganic chemical processes.
- Commonly used in the production of salts, acids, and bases.
-
Rising Film Evaporators:
- Effective for processing solutions with low to moderate viscosity.
- Used in applications requiring high evaporation rates, such as solvent recovery and concentration of chemical intermediates.
-
Falling Film Evaporators:
-
Factors Influencing Evaporator Selection
-
Thermal Sensitivity:
- Falling film evaporators are preferred for heat-sensitive materials due to their short contact time and minimal thermal degradation.
-
Viscosity and Solids Content:
- Forced circulation evaporators are better suited for high-viscosity solutions or those with suspended solids.
-
Energy Efficiency:
- Multi-effect evaporators, which reuse vapor from one stage to heat the next, are chosen for energy-intensive processes.
-
Scale of Operation:
- Large-scale chemical plants often use forced circulation or multi-effect evaporators for their high throughput and efficiency.
-
Thermal Sensitivity:
-
Applications in the Chemical Industry
-
Solvent Recovery:
- Evaporators are used to recover solvents from chemical reactions, reducing waste and costs.
-
Concentration of Solutions:
- Used to increase the concentration of chemical solutions for further processing or storage.
-
Waste Treatment:
- Evaporators help in treating chemical waste by concentrating and separating hazardous components.
-
Solvent Recovery:
-
Advantages of Specific Evaporator Types
-
Falling Film Evaporators:
- High heat transfer efficiency and low energy consumption.
- Minimal fouling and easy maintenance.
-
Forced Circulation Evaporators:
- Ability to handle abrasive and scaling materials.
- High evaporation rates and robust design.
-
Rising Film Evaporators:
- Suitable for continuous operation and high-capacity processes.
- Effective for low-viscosity solutions.
-
Falling Film Evaporators:
-
Considerations for Equipment Purchasers
- Material Compatibility: Ensure the evaporator materials are resistant to the chemicals being processed.
- Operational Costs: Evaluate energy consumption, maintenance requirements, and downtime.
- Scalability: Choose equipment that can accommodate future production increases.
- Regulatory Compliance: Ensure the evaporator meets industry standards for safety and environmental regulations.
In summary, the choice of evaporator in the chemical industry depends on the specific requirements of the process, including the nature of the solution, thermal sensitivity, and operational scale. Falling film, forced circulation, and rising film evaporators are the most commonly used types, each offering distinct advantages for different applications. Equipment purchasers should carefully evaluate these factors to select the most suitable evaporator for their needs.
Summary Table:
Evaporator Type | Key Features | Applications |
---|---|---|
Falling Film | Low residence time, efficient heat transfer, minimal fouling | Heat-sensitive materials, high-viscosity solutions, polymers, specialty chemicals |
Forced Circulation | Handles high solids content, operates at high pressures and temperatures | Inorganic chemicals, salts, acids, bases |
Rising Film | High evaporation rates, suitable for low to moderate viscosity solutions | Solvent recovery, concentration of chemical intermediates |
Need help selecting the right evaporator for your chemical processes? Contact our experts today for tailored solutions!