Evaporation under vacuum pressure is essential for several reasons, primarily to lower the boiling point of liquids, protect heat-sensitive materials, and ensure process efficiency and purity. By reducing the pressure, the energy required for molecules to transition from the liquid to the gas phase decreases, enabling evaporation at lower temperatures. This is particularly beneficial for heat-sensitive substances, as it prevents thermal degradation. Additionally, vacuum conditions minimize contamination by reducing interactions with background gases, ensuring that only the desired vapors reach the target. Vacuum systems also allow for precise control over the evaporation process, making them indispensable in applications like rotary evaporation and vacuum distillation.
Key Points Explained:
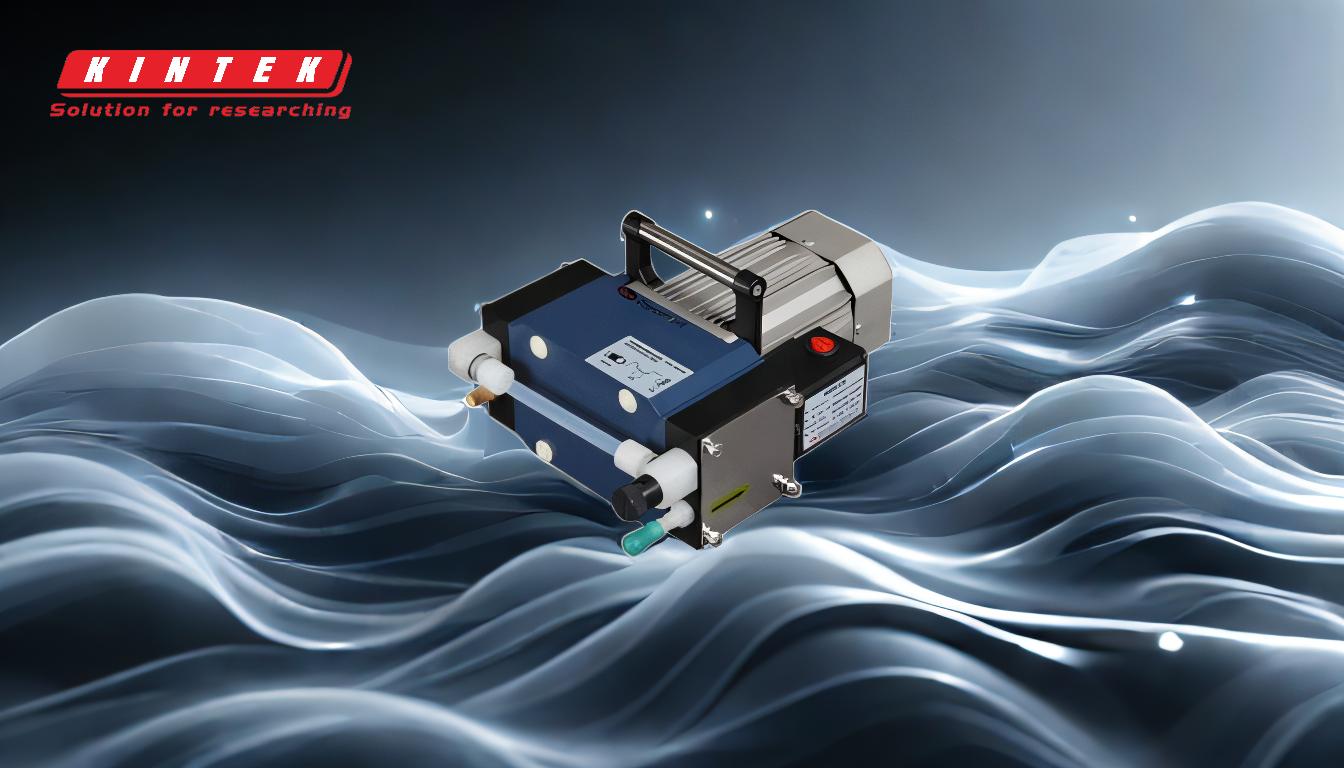
-
Lowering the Boiling Point:
- Explanation: Under vacuum conditions, the pressure is reduced, which decreases the energy required for molecules to transition from the liquid to the gas phase. This allows liquids to evaporate at much lower temperatures than they would at atmospheric pressure.
- Application: This is particularly useful for heat-sensitive materials, as it prevents thermal degradation or "cooking" of the contents. For example, in rotary evaporation, vacuum pressure enables the gentle separation of solvents without damaging the sample.
-
Protecting Heat-Sensitive Materials:
- Explanation: Many substances, such as certain chemicals or biological samples, are sensitive to high temperatures. By lowering the boiling point through vacuum pressure, these materials can be processed without exposure to damaging heat.
- Application: In industries like pharmaceuticals or food processing, vacuum evaporation ensures that delicate compounds, such as aromas or active pharmaceutical ingredients, remain intact during the separation process.
-
Ensuring Process Efficiency:
- Explanation: Vacuum systems allow for faster and more efficient evaporation by reducing the time and energy required to achieve the desired separation. This is because the lower pressure accelerates the transition of molecules into the gas phase.
- Application: In processes like vacuum distillation, solvents with high boiling points (e.g., DMSO) can be evaporated at modest temperatures, significantly reducing processing time.
-
Minimizing Contamination:
- Explanation: In a vacuum environment, the presence of background gases is minimized, reducing the likelihood of contamination. This ensures that only the desired vapors reach the deposition target or collection vessel.
- Application: In thin-film deposition or chemical synthesis, maintaining a high-purity environment is critical to achieving consistent and high-quality results.
-
Precise Control Over the Process:
- Explanation: Vacuum pressure is a key variable that can be rapidly adjusted to achieve the desired boiling point. Unlike temperature, which changes more slowly, vacuum pressure can be fine-tuned to optimize the evaporation process.
- Application: In rotary evaporators, the vacuum pump is a critical component that allows operators to precisely control the evaporation rate and ensure efficient separation of mixtures with different boiling points.
-
Facilitating Separation and Recovery:
- Explanation: Vacuum pressure helps draw vapors from the evaporating flask into the condenser, where they are cooled and condensed back into liquids. This facilitates the separation and recovery of distillates.
- Application: In processes like solvent recovery or essential oil extraction, vacuum evaporation ensures that valuable components are efficiently collected without loss or degradation.
-
Enabling Gentle Separation:
- Explanation: The combination of vacuum pressure and rotation in devices like rotary evaporators creates a gentle separation process. This is ideal for mixtures with varying boiling points, as it prevents overheating and ensures uniform evaporation.
- Application: In laboratories, this technique is widely used for concentrating solutions, purifying compounds, or isolating specific components from complex mixtures.
By leveraging vacuum pressure, evaporation processes become more efficient, precise, and adaptable to a wide range of applications, from industrial manufacturing to laboratory research. The ability to control pressure ensures that materials are processed safely and effectively, making vacuum systems an indispensable tool in modern science and industry.
Summary Table:
Key Benefit | Explanation | Application |
---|---|---|
Lowering the Boiling Point | Reduces energy required for evaporation, enabling lower temperature evaporation. | Protects heat-sensitive materials in rotary evaporation and vacuum distillation. |
Protecting Heat-Sensitive Materials | Prevents thermal degradation by lowering boiling points. | Essential in pharmaceuticals and food processing for delicate compounds. |
Ensuring Process Efficiency | Accelerates evaporation, reducing time and energy. | Ideal for vacuum distillation of high-boiling solvents like DMSO. |
Minimizing Contamination | Reduces background gases, ensuring high-purity environments. | Critical for thin-film deposition and chemical synthesis. |
Precise Control Over the Process | Allows rapid adjustment of vacuum pressure for optimal evaporation. | Used in rotary evaporators for efficient separation of mixtures. |
Facilitating Separation and Recovery | Draws vapors into condensers for efficient recovery. | Essential for solvent recovery and essential oil extraction. |
Enabling Gentle Separation | Combines vacuum pressure and rotation for uniform evaporation. | Widely used in labs for concentrating solutions and purifying compounds. |
Ready to optimize your evaporation process? Contact us today to learn more about vacuum systems!