Magnets are placed behind the target in sputtering to enhance the efficiency and effectiveness of the deposition process. By creating a magnetic field, electrons are trapped near the target surface, increasing their path length and the likelihood of ionizing collisions with argon gas. This results in a higher plasma density and sputtering rate, allowing for faster and more uniform thin-film deposition at lower pressures. The magnetic field also helps contain the plasma close to the target, reducing electron bombardment on the substrate and preventing thermal damage. Overall, magnets improve sputtering efficiency, deposition rate, and film quality.
Key Points Explained:
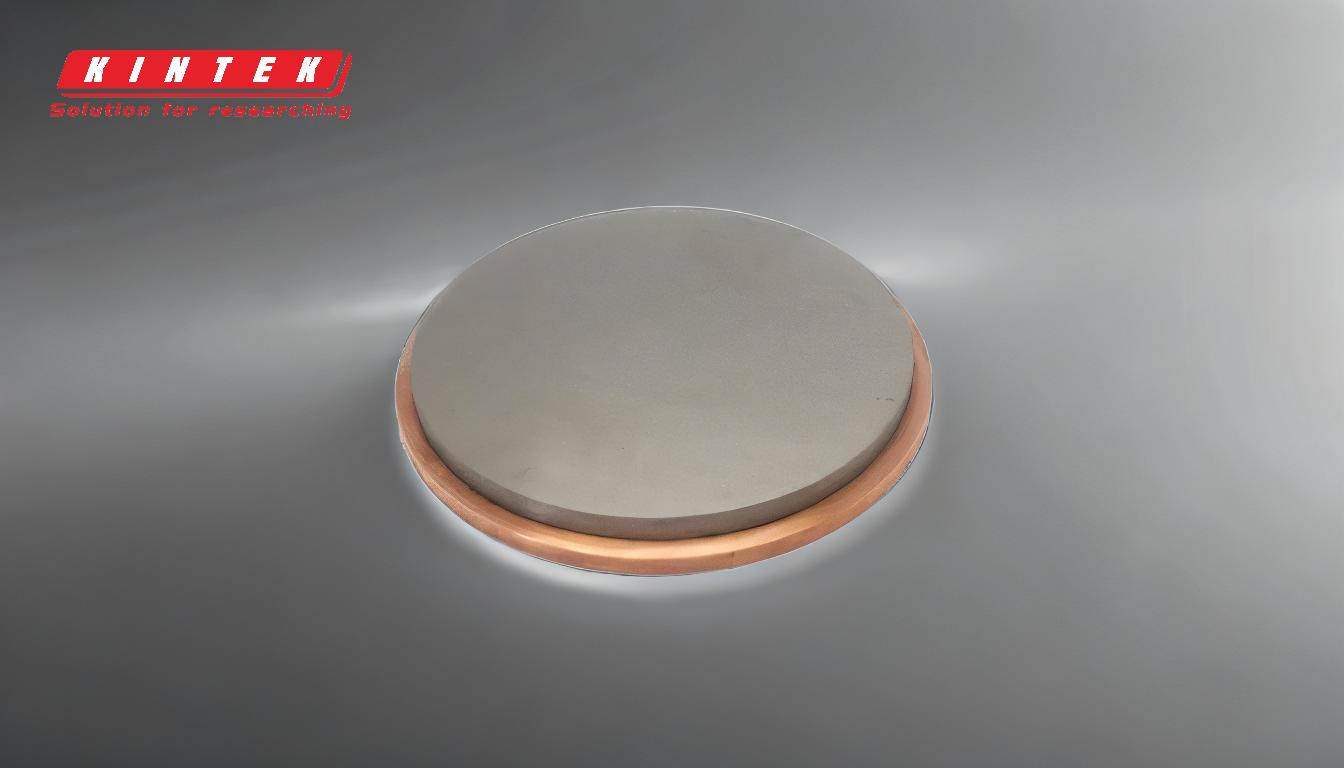
-
Plasma Containment and Ionization Enhancement:
- Magnets create a magnetic field that traps secondary electrons near the target surface.
- Electrons spiral around the magnetic field lines, increasing their path length and the number of ionizing collisions with argon gas.
- This enhances the ionization of the plasma near the target, leading to a higher density of argon ions.
- Higher ion density increases the probability of collisions between argon ions and the target material, boosting the sputtering rate.
-
Increased Sputtering Rate:
- The magnetic field accelerates the ionization of argon gas, increasing the number of argon ions available to bombard the target.
- More argon ions striking the target result in a higher rate of material ejection from the target surface.
- This leads to faster deposition of the thin film onto the substrate.
-
Lower Operating Pressure:
- The enhanced ionization near the target allows the plasma to be sustained at lower pressures.
- Lower pressure reduces the number of gas-phase collisions, allowing sputtered atoms to travel more directly to the substrate.
- This results in a more efficient deposition process with fewer defects in the thin film.
-
Reduction of Electron Bombardment on the Substrate:
- The magnetic field confines the plasma close to the target, reducing the number of electrons that reach the substrate.
- This minimizes thermal damage to the substrate and improves the quality of the deposited film.
-
Uniform Erosion of the Target:
- Magnets help create a stable and uniform erosion pattern on the target surface.
- Uniform erosion ensures consistent deposition rates and film thickness across the substrate.
- This is crucial for achieving high-quality, reproducible thin films.
-
Improved Thin-Film Growth:
- The magnetic field increases the percentage of target material that becomes ionized.
- Ionized atoms are more likely to interact with other particles and settle on the substrate.
- This improves the efficiency of the deposition process, allowing thin films to grow more quickly and uniformly.
-
Energy Efficiency:
- By trapping electrons and enhancing ionization, magnets reduce the energy required to sustain the plasma.
- This makes the sputtering process more energy-efficient, lowering operational costs.
-
Versatility in Applications:
- The use of magnets in sputtering allows for the deposition of a wide range of materials, including metals, semiconductors, and insulators.
- This versatility makes magnetron sputtering a preferred technique in various industries, such as electronics, optics, and coatings.
In summary, magnets placed behind the target in sputtering play a crucial role in enhancing the efficiency, uniformity, and quality of the thin-film deposition process. They achieve this by trapping electrons, increasing plasma density, and improving ionization, all of which contribute to a faster and more controlled deposition of materials onto the substrate.
Summary Table:
Key Benefit | Explanation |
---|---|
Plasma Containment | Magnets trap electrons, increasing ionization and plasma density near the target. |
Increased Sputtering Rate | Higher argon ion density accelerates material ejection for faster deposition. |
Lower Operating Pressure | Enhanced ionization allows efficient deposition at reduced pressures. |
Reduced Substrate Damage | Plasma confinement minimizes electron bombardment, preventing thermal damage. |
Uniform Target Erosion | Ensures consistent deposition rates and film thickness. |
Improved Thin-Film Growth | Ionized atoms settle more efficiently, enhancing film quality. |
Energy Efficiency | Reduces energy required to sustain plasma, lowering operational costs. |
Versatile Applications | Suitable for depositing metals, semiconductors, and insulators. |
Want to optimize your sputtering process? Contact our experts today to learn more!