Stainless steel reactors are widely used in various industrial and laboratory applications due to their unique properties. They are particularly valued for their high mechanical strength, stability, and resistance to abrasion and wear. These reactors are suitable for high-pressure and high-temperature conditions, making them ideal for demanding applications. Additionally, stainless steel reactors are easy to inspect and repair, which enhances their longevity and reliability. However, they are more expensive than glass reactors and do not provide visibility into the reaction process, which can be a limitation depending on the specific requirements of the application.
Key Points Explained:
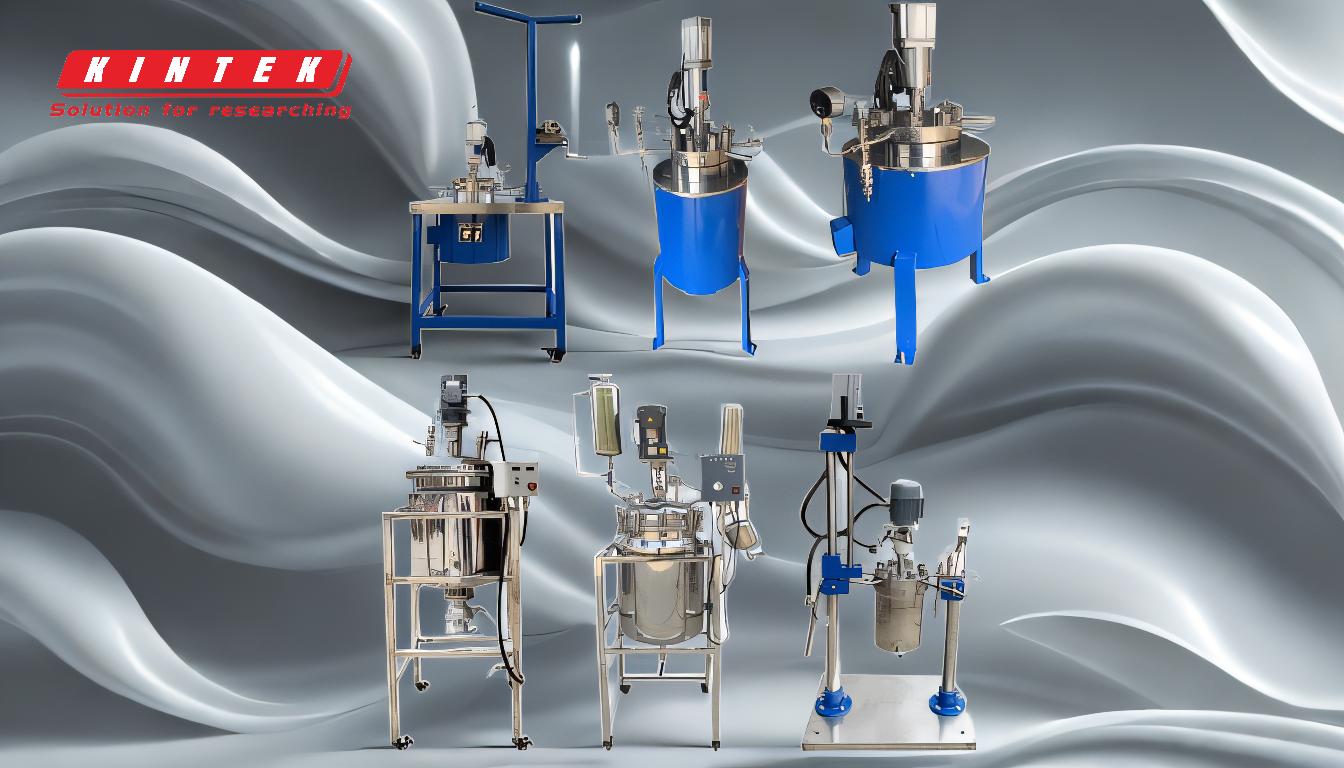
-
High Mechanical Strength and Stability:
- Stainless steel reactors are known for their robustness and ability to withstand significant mechanical stress. This makes them suitable for applications where the reactor must endure high pressures and temperatures without deforming or failing.
- The stability of stainless steel ensures that the reactor maintains its structural integrity over time, even under harsh conditions, which is crucial for long-term reliability.
-
Resistance to Abrasion and Wear:
- Stainless steel's inherent resistance to abrasion and wear makes it an excellent choice for reactions involving abrasive materials or those that require frequent stirring or mixing.
- This resistance reduces the need for frequent maintenance or replacement of reactor components, thereby lowering operational costs over time.
-
Suitability for High-Pressure and High-Temperature Conditions:
- Stainless steel reactors are designed to handle high-pressure and high-temperature environments, making them ideal for processes that require above-reflux conditions or pressurized reactions.
- This capability is particularly important in industries such as chemical manufacturing, where reactions often occur under extreme conditions.
-
Chemical Resistance:
- Stainless steel, especially when alloyed with materials like Hastelloy, offers improved resistance to a wide range of chemicals. This makes it suitable for reactions involving corrosive substances.
- The chemical resistance of stainless steel reactors ensures that they can be used in a variety of chemical processes without the risk of material degradation.
-
Ease of Inspection and Repair:
- Stainless steel reactors are relatively easy to inspect and repair, which is a significant advantage in maintaining operational efficiency.
- The ability to quickly identify and address any issues reduces downtime and ensures that the reactor can be kept in optimal working condition with minimal disruption to the process.
-
Cost and Visibility Considerations:
- While stainless steel reactors are more expensive than glass reactors, their durability and suitability for demanding conditions often justify the higher initial investment.
- A notable limitation of stainless steel reactors is the lack of visibility into the reaction process, which can be a disadvantage in applications where monitoring the reaction visually is important.
In summary, stainless steel reactors are chosen for their strength, durability, and suitability for demanding conditions. However, the choice between stainless steel and other materials like glass depends on the specific requirements of the reaction, including the need for visibility, pressure and temperature conditions, and budget constraints.
Summary Table:
Feature | Description |
---|---|
High Mechanical Strength | Withstands high pressures and temperatures without deformation. |
Resistance to Abrasion and Wear | Ideal for abrasive materials and frequent stirring, reducing maintenance costs. |
High-Pressure & High-Temperature | Suitable for extreme conditions in industries like chemical manufacturing. |
Chemical Resistance | Resists corrosion, especially when alloyed with materials like Hastelloy. |
Ease of Inspection and Repair | Minimal downtime and easy maintenance enhance operational efficiency. |
Cost and Visibility | Higher initial cost but durable; lacks visibility into reaction processes. |
Ready to choose the right reactor for your needs? Contact us today for expert guidance!