Types of Laboratory Mixing Equipment
Magnetic Stirrer
A magnetic stirrer is an essential piece of equipment in the laboratory, primarily used for the efficient mixing of liquids. It operates by harnessing the power of magnetic fields to rotate a stirrer, often referred to as a magnetic flea, within a container. This rotation ensures uniform distribution of solutes within the solvent, facilitating accurate and consistent results in various laboratory processes.
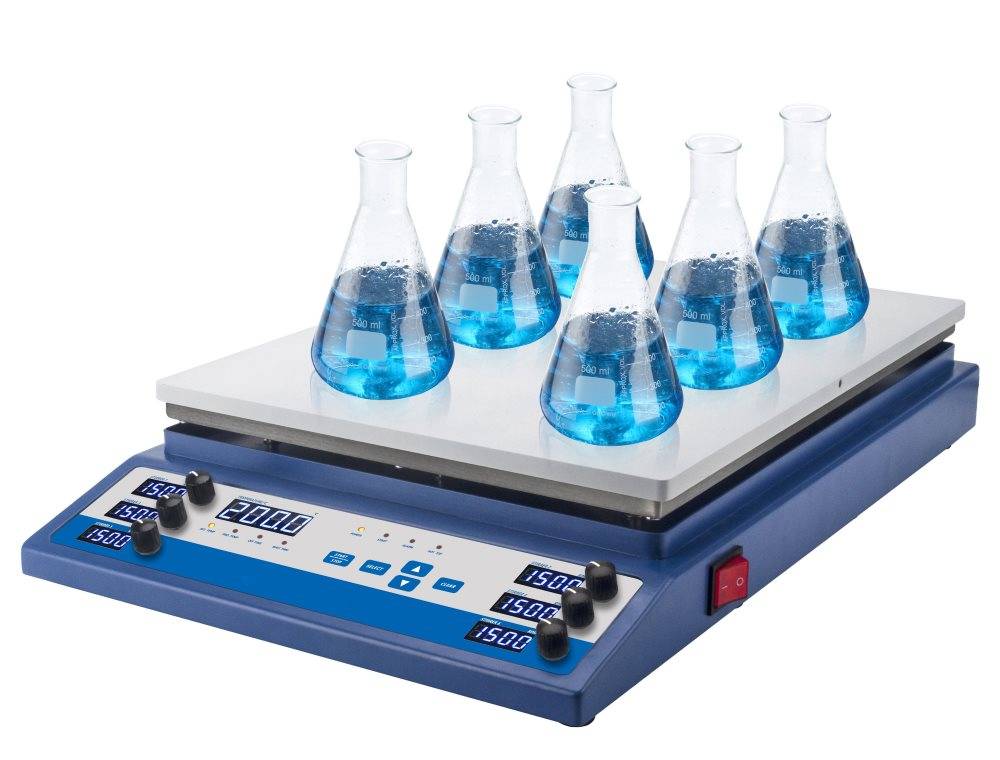
The magnetic stirrer is particularly advantageous due to its simplicity and effectiveness. Unlike other mixing devices that may require direct mechanical contact with the liquid, the magnetic stirrer achieves mixing through indirect magnetic interaction. This design not only reduces the risk of contamination but also allows for easy operation and maintenance.
Moreover, the versatility of magnetic stirrers extends to their compatibility with a wide range of container sizes and shapes. Whether it's a small beaker or a larger flask, the adjustable magnetic field ensures that the stirrer aligns and rotates appropriately, maintaining optimal mixing conditions. This adaptability makes magnetic stirrers a popular choice in both academic and industrial laboratories.
In addition to their basic mixing function, modern magnetic stirrers often come equipped with additional features such as adjustable speed control and digital displays. These enhancements allow for precise control over the mixing process, catering to the specific needs of different experiments and applications.
Electric Stirrer
The electric stirrer stands out as a versatile and technologically advanced piece of equipment, particularly suited for a wide array of industries including heavy industry, light industry, and pharmaceuticals. Unlike traditional stirrers, the electric variant is equipped with a digital display that not only enhances user control but also provides precise monitoring of the mixing process.
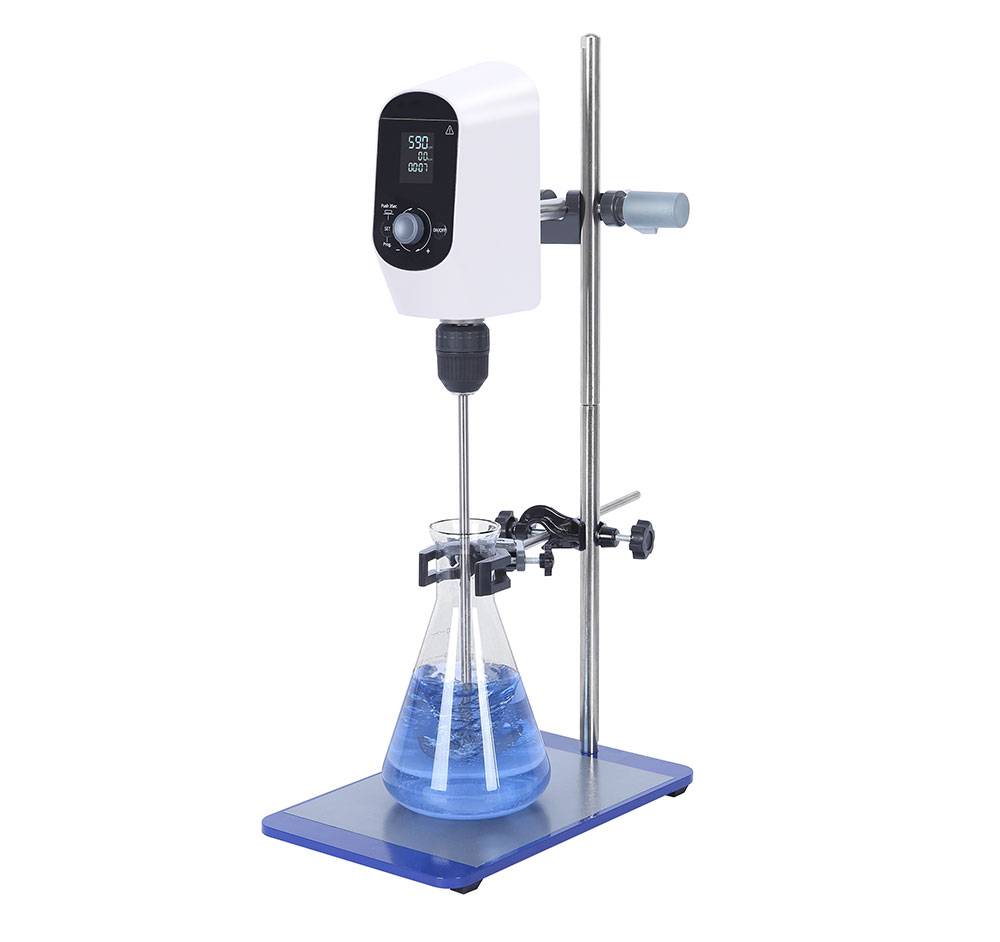
In heavy industry applications, electric stirrers are indispensable for tasks that require robust mixing capabilities and durability. Their force-enhancing features ensure that even the most viscous materials can be mixed efficiently, reducing processing time and improving overall productivity. Similarly, in light industry settings, these stirrers offer the flexibility and precision needed for delicate operations, such as the creation of various formulations and solutions.
The pharmaceutical industry benefits significantly from electric stirrers due to their ability to maintain a sterile environment and ensure accurate mixing ratios. This precision is crucial in the preparation of drugs and medical solutions, where even minor deviations can have significant implications. The digital interface of these stirrers allows for real-time adjustments, ensuring that each batch meets the stringent quality standards required by the industry.
Moreover, the adaptability of electric stirrers extends beyond their industrial applications. In research laboratories, these devices are frequently used for a variety of experimental setups, providing reliable and consistent results. Their ease of use and the ability to handle different types of materials make them a preferred choice among researchers and scientists.
In summary, the electric stirrer, with its digital display and force-enhancing capabilities, is a pivotal tool across multiple industries, offering precision, durability, and adaptability in various mixing tasks.
Disperser
The disperser is a versatile piece of equipment that integrates multiple functions, including stirring, sanding, and dispersing. Its compact design ensures that it occupies minimal space in the laboratory, making it an ideal choice for researchers working in confined areas. Additionally, the disperser operates with remarkably low noise levels, contributing to a quieter and more comfortable working environment.
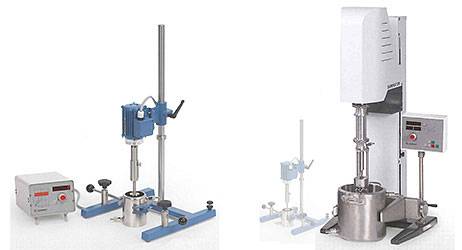
One of the standout features of the disperser is its digital speed display, which allows users to precisely control and monitor the operation speed. This digital interface not only enhances the user experience but also ensures consistent and reliable performance, which is crucial for accurate experimental results. Whether it's blending different substances or achieving a uniform dispersion, the disperser's advanced functionalities make it an indispensable tool in various laboratory settings.
Emulsifier
High-shear emulsifiers are crucial in laboratory settings for achieving precise and uniform emulsions. These devices operate by applying intense mechanical forces to break down liquid mixtures into ultra-fine particles, typically in the nanometer range. The process of high-speed nano-emulsification is amplified through specialized blades or impellers that generate significant shear forces, ensuring that even the most challenging mixtures can be homogenized effectively.
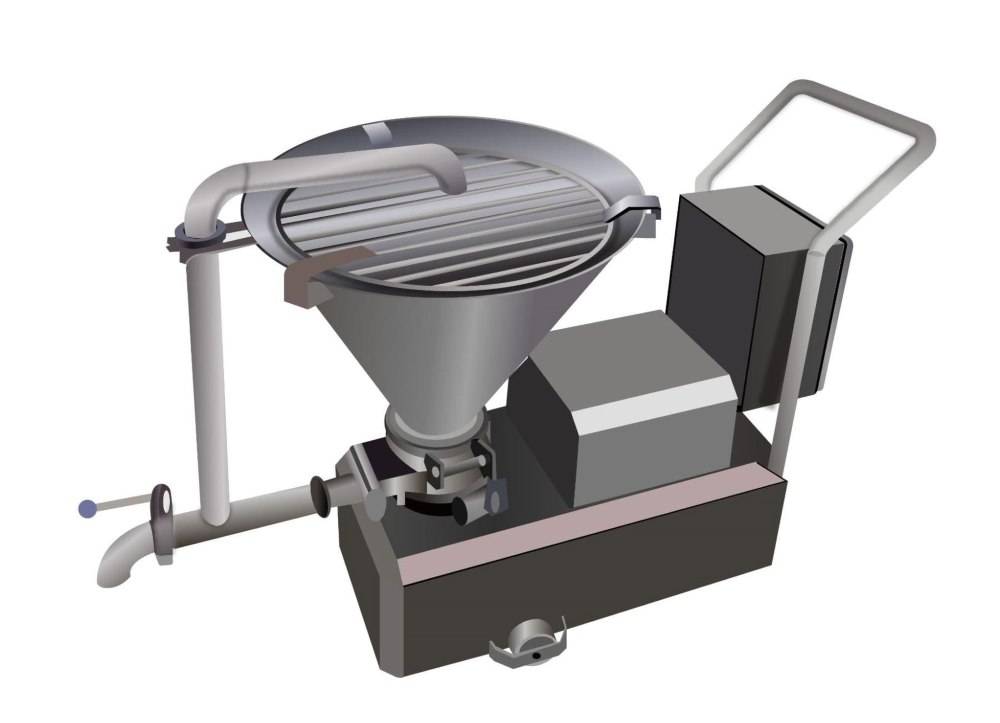
This technology is particularly advantageous in applications where uniformity and particle size are critical, such as in pharmaceutical formulations, food processing, and cosmetic production. The ability to create ultra-fine particle sizes not only enhances the stability of the emulsion but also improves the overall quality and consistency of the final product. High-shear emulsifiers are designed to handle a variety of viscosities and can be fine-tuned to meet specific requirements, making them an indispensable tool in modern laboratory workflows.
Homogenizer
Homogenizers are versatile devices used across multiple industries, including biotechnology, medicine, food processing, and more. In biotechnology, homogenizers are essential for tissue dispersion, breaking down cell walls to extract cellular components for further analysis. In the medical field, they play a crucial role in sample preparation, ensuring that biological samples are uniformly processed for accurate diagnostic results.
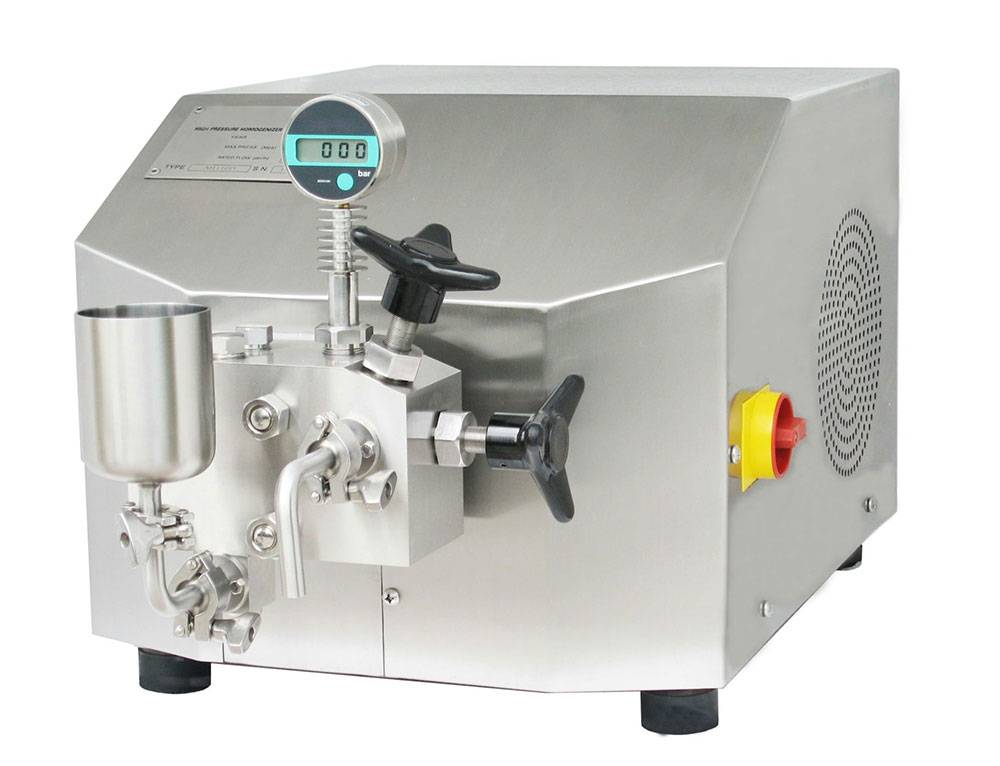
In the food industry, homogenizers are employed for enzyme treatment, which is vital for enhancing the texture and stability of food products. For instance, homogenizers are commonly used in the dairy industry to homogenize milk, preventing cream from separating and ensuring a consistent product. This process involves forcing milk through tiny valves or tubes under extremely high pressures, typically up to 1,500 bar (21,750 psi), using high-pressure pumps or piston homogenizers.
Ultrasonic homogenizers, also known as sonicators or sonic disruptors, utilize ultrasonic cavitation to achieve component disruption. This method involves generating rarefaction and compression periods at ultrasonic frequencies, creating cavitation bubbles that implode and break down materials. This technique is particularly effective for applications requiring fine particle dispersion and uniform mixtures.
Overall, homogenizers are indispensable tools in various scientific and industrial processes, facilitating efficient and precise mixing, dispersion, and homogenization of materials.
CONTACT US FOR A FREE CONSULTATION
KINTEK LAB SOLUTION's products and services have been recognized by customers around the world. Our staff will be happy to assist with any inquiry you might have. Contact us for a free consultation and talk to a product specialist to find the most suitable solution for your application needs!