When ceramics, particularly clays, are fired in a kiln, the carbon and organic compounds they contain undergo a process called oxidation, where they burn off. This combustion is essential to prevent defects in the final product, such as bloating or discoloration, which can occur if the carbon is not fully removed. The process involves heating the material to high temperatures, typically between 500°C to 900°C, where the carbon reacts with oxygen to form carbon dioxide and other gases, which are then vented out of the kiln. After firing, the material is cooled and processed further, often involving grinding and pelletizing, before being packaged for transport.
Key Points Explained:
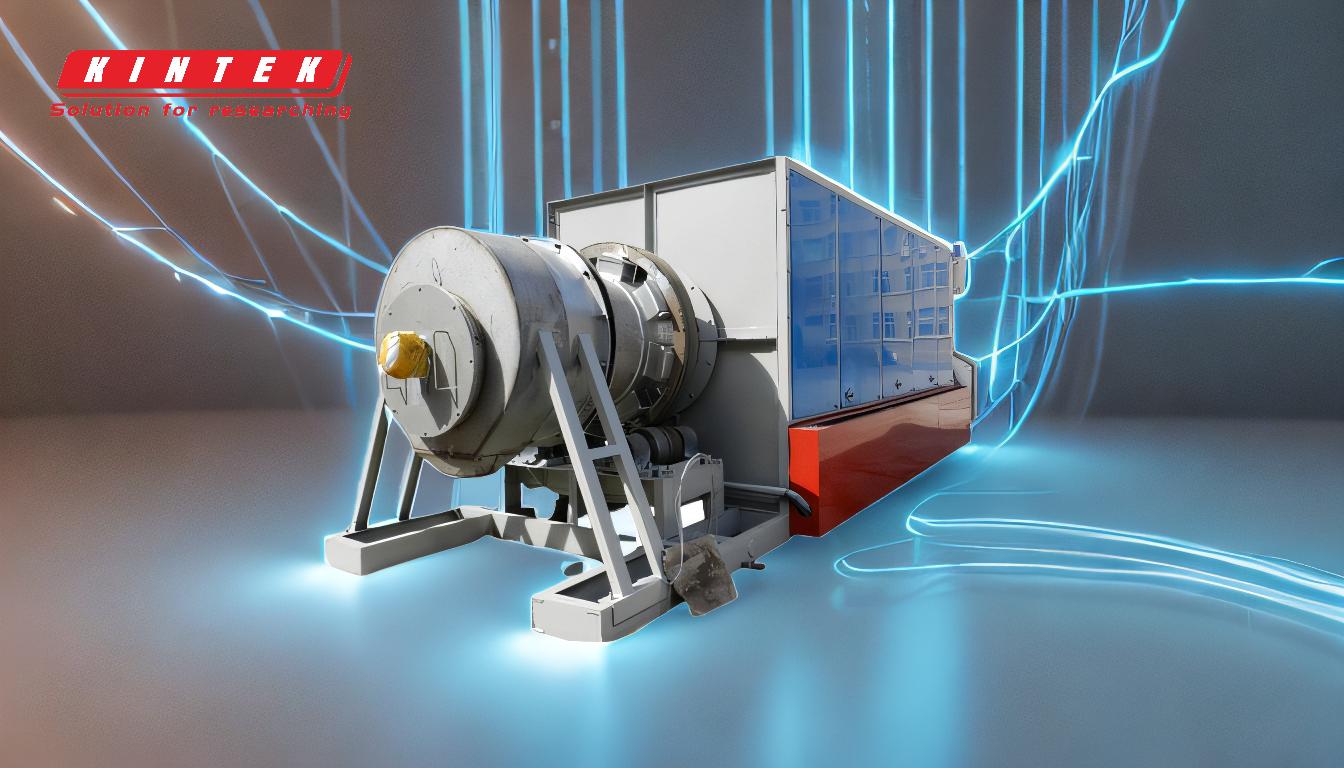
-
Presence of Carbon in Ceramics:
- Ceramic materials, especially clays, naturally contain carbon and organic compounds. These can originate from the decomposition of plant and animal matter in the soil where the clay is formed.
-
The Need to Burn Off Carbon:
- During the firing process in a kiln, it is crucial to burn off the carbon and organic compounds. If not removed, these can cause defects in the ceramic products, such as bloating, black coring, or discoloration, which compromise the structural integrity and aesthetic quality of the final product.
-
Oxidation Process:
- The burning off of carbon occurs through an oxidation process. This involves heating the ceramic material to temperatures typically between 500°C to 900°C. At these temperatures, the carbon reacts with oxygen present in the kiln atmosphere to form carbon dioxide (CO₂) and other gaseous byproducts.
- The oxidation process is carefully controlled to ensure complete combustion of carbonaceous materials. Inadequate oxidation can leave residual carbon, leading to the aforementioned defects.
-
Complications During Firing:
- The combustion of carbon and organic compounds can produce complications during the firing process. These include the release of gases that can cause bloating or pinholes in the ceramic body if not properly vented. Additionally, rapid oxidation can lead to thermal shock, potentially cracking the ceramic pieces.
-
Post-Firing Processing:
- After the carbon has been burned off and the ceramic material has been fired, the material is cooled. This cooling process must be controlled to prevent thermal stress that could lead to cracking.
- Once cooled, the material may undergo further processing, such as grinding to achieve the desired particle size, pelletizing for easier handling, and bagging for transport. This ensures the material is ready for its next use or for distribution.
-
Importance of Temperature Control:
- The temperature at which the carbon burns off is critical. If the kiln temperature is too low, the carbon may not fully combust, leading to defects. Conversely, if the temperature is too high, it can cause other issues, such as over-firing, which can weaken the ceramic structure.
- Kiln operators must carefully monitor and control the temperature throughout the firing cycle to ensure optimal results.
-
Environmental Considerations:
- The release of carbon dioxide and other gases during the firing process has environmental implications. Modern kilns are often equipped with systems to capture and treat these emissions to minimize their environmental impact.
- Efficient combustion of carbon also contributes to reducing the overall carbon footprint of the ceramic manufacturing process.
In summary, the burning off of carbon in a kiln is a critical step in the ceramic manufacturing process. It involves a carefully controlled oxidation process to ensure the complete removal of carbon and organic compounds, thereby preventing defects in the final product. Proper temperature control, venting, and post-firing processing are essential to achieve high-quality ceramics. Additionally, environmental considerations play a role in managing the emissions produced during this process.
Summary Table:
Key Aspect | Details |
---|---|
Presence of Carbon | Ceramics, especially clays, contain carbon from decomposed organic matter. |
Need to Burn Off Carbon | Prevents defects like bloating, discoloration, and black coring. |
Oxidation Process | Carbon reacts with oxygen at 500°C–900°C to form CO₂, ensuring combustion. |
Complications During Firing | Gas release can cause bloating or cracking if not properly vented. |
Post-Firing Processing | Cooling, grinding, pelletizing, and packaging ensure material readiness. |
Temperature Control | Critical to avoid under-firing or over-firing, which can weaken ceramics. |
Environmental Impact | Emissions are managed to reduce the carbon footprint of ceramic production. |
Ensure high-quality ceramics with expert firing solutions—contact us today for more information!