Copper foam is a lightweight, porous material with high thermal and electrical conductivity, making it ideal for applications like heat exchangers, filters, and battery electrodes. It is typically fabricated using a powder metallurgy method involving copper powder and a sacrificial template, such as sugar particles. The process involves mixing copper powder with sugar, compacting the mixture, sintering it at high temperatures, and dissolving the sugar to create a porous structure. The density and porosity of the foam are controlled by adjusting the weight fraction of sugar and the sintering temperature.
Key Points Explained:
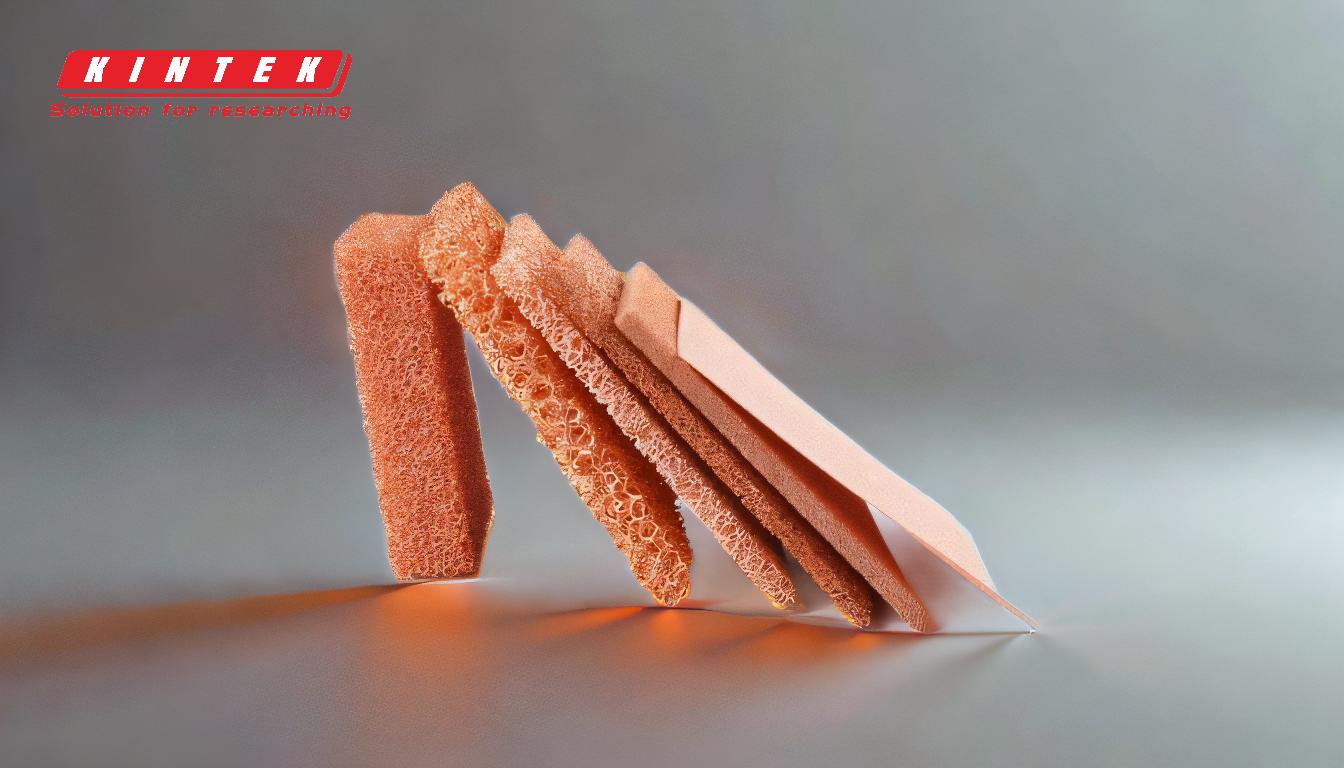
-
Materials Required:
- Copper Powder: The primary material used to form the foam's structure.
- Sacrificial Template (Sugar Particles): Acts as a placeholder to create pores in the foam. Sugar is chosen because it is inexpensive, easy to dissolve, and leaves minimal residue.
- Binder (Optional): Sometimes added to improve the cohesion of the mixture.
-
Mixing Process:
- Copper powder and sugar particles are thoroughly mixed to ensure uniform distribution.
- The weight fraction of sugar determines the final porosity and density of the foam. A higher sugar content results in more pores and lower density.
-
Compaction:
- The mixture is compacted into a mold under pressure to form a green body (a pre-sintered structure).
- Compaction ensures the particles are in close contact, which is crucial for sintering.
-
Sintering:
- The green body is sintered at a high temperature (e.g., 875 °C) in a controlled atmosphere (e.g., inert gas or vacuum) to prevent oxidation.
- During sintering, the copper particles bond together, forming a solid structure, while the sugar particles remain intact.
-
Sugar Dissolution:
- After sintering, the sugar is dissolved in water or another solvent, leaving behind a porous copper structure.
- The size and distribution of the pores depend on the size of the sugar particles and their weight fraction in the mixture.
-
Factors Affecting Foam Properties:
- Weight Fraction of Sugar: Higher sugar content increases porosity but reduces mechanical strength.
- Sintering Temperature: Affects the bonding between copper particles. Too low a temperature may result in weak bonding, while too high a temperature may cause excessive shrinkage.
- Particle Size: Smaller sugar particles create finer pores, while larger particles result in coarser pores.
-
Applications of Copper Foam:
- Heat Exchangers: The high surface area and thermal conductivity make it ideal for heat transfer applications.
- Filters: The porous structure allows for efficient filtration of gases or liquids.
- Battery Electrodes: The conductivity and porosity enhance the performance of batteries.
By carefully controlling the process parameters, such as the weight fraction of sugar and sintering temperature, copper foam with tailored properties can be produced for specific applications.
Summary Table:
Aspect | Details |
---|---|
Materials Required | Copper powder, sugar particles (sacrificial template), optional binder |
Mixing Process | Uniform mixing of copper powder and sugar; sugar weight fraction controls porosity |
Compaction | Mixture pressed into a mold to form a green body |
Sintering | Heated at high temperatures (e.g., 875°C) in a controlled atmosphere |
Sugar Dissolution | Sugar dissolved in water, leaving a porous copper structure |
Key Factors | Weight fraction of sugar, sintering temperature, particle size |
Applications | Heat exchangers, filters, battery electrodes |
Need copper foam for your next project? Contact us today to learn more!